Przegląd usług
Status Check „Oznaczenie CE na maszynach”
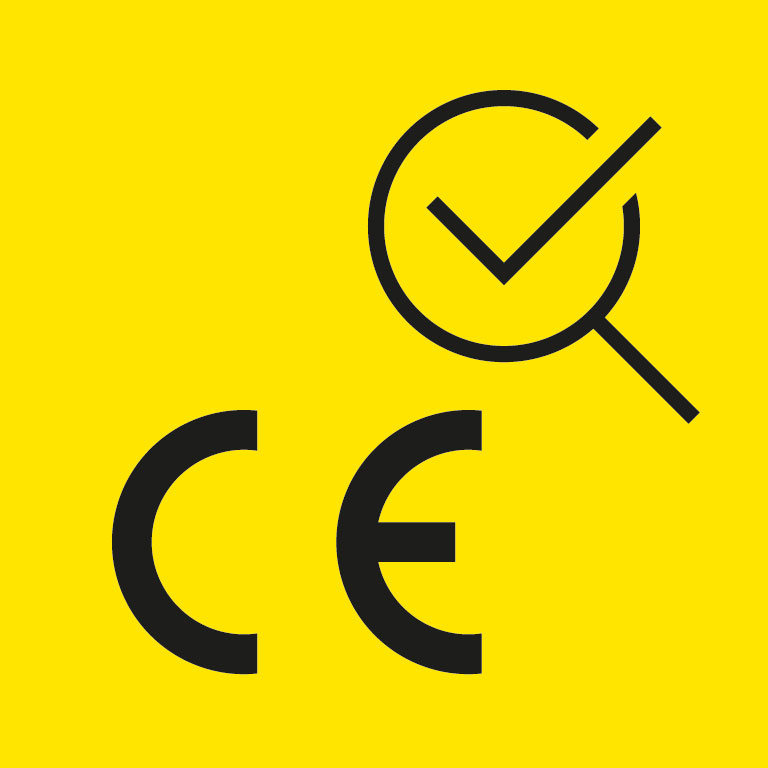
Twoje wymagania
Jako producent musisz
- przygotować dokumentację podczas konstrukcji i po wyprodukowaniu maszyn zgodnie z wymaganiami Dyrektywy Maszynowej
- zwracać uwagę na kompletność dokumentacji i zgodność z odpowiednimi normami
- potwierdzić prawidłową procedurę poprzez deklarację zgodności UE i oznakowanie CE
Dla Ciebie, jako użytkownika
- oryginalna instrukcja obsługi stanowi pomoc w przygotowaniu oceny ryzyka
Nasze rozwiązanie
Sprawdzamy przestrzeganie wymagań dyrektywy maszynowej dla
- deklaracji zgodności/deklaracji wbudowania i oznaczenia CE
- oryginalnej instrukcji eksploatacji i wymagań wobec bezpieczeństwa
- dostosowania bezpiecznej części sterownika na podstawie odnośnych norm UE
- dokumentacji maszyny
Korzyści dla Ciebie
- Niezależna weryfikacja kompletności i zawartości dokumentacji zgodnie z wymaganiami Dyrektywy Maszynowej
- Zalecenia poprawy w razie ewentualnych odchyleń
Ocena ryzyka
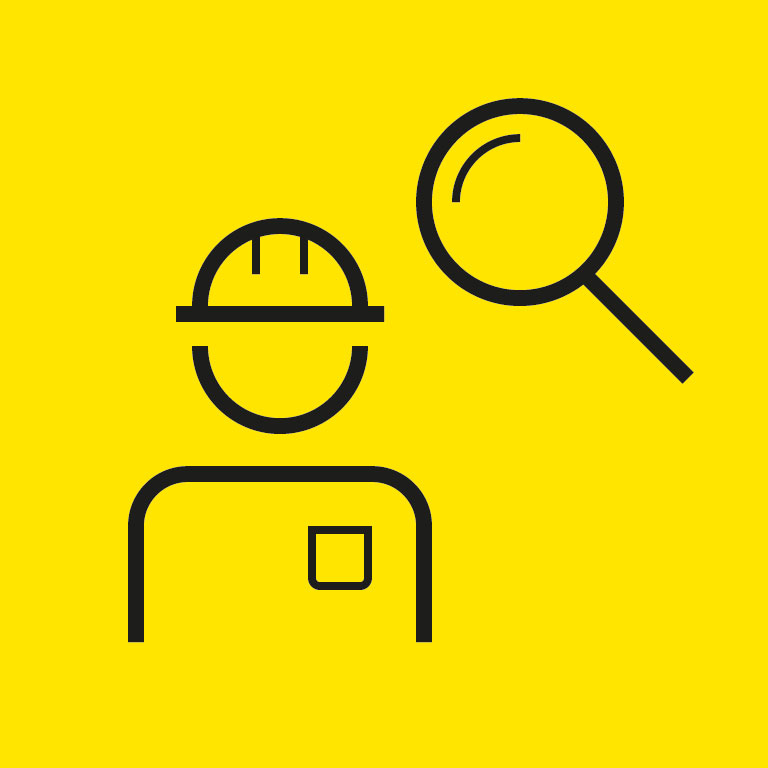
Twoje wymagania
- W ramach procesu oceny zgodności maszyny należy przeprowadzić ocenę ryzyka. Należy uwzględnić wymagania prawne i wymagania normatywne specyficzne dla maszyny.
- W przypadku przebudowy lub rozbudowy istniejącej maszyny należy dostosować ocenę ryzyka
- Ocena i ocena zagrożeń i ryzyka powinna być przeprowadzona przez niezależną osobę
Nasze rozwiązanie
- Analiza istniejących zagrożeń
- Ocena istniejących ryzyk i kalkulacja wskaźników ryzyka z wykorzystaniem procesu oceny ryzyka Leuze HARMONY (Hazard Rating for Machinery and prOcess iNdustrY)
- Opis działań zmniejszających ryzyko
- Dowód skuteczności na drodze ponownej oceny ryzyk po zastosowaniu działań zmniejszających ryzyko
Korzyści dla Ciebie
- Skorzystaj z naszego wieloletniego doświadczenia przy tworzeniu ocen ryzyka
- Rozwiązania odpowiednie do potrzeb: od celowego wsparcia po kompletne wdrożenie
- Szczegółowy opis czynników ryzyka i określenie wskaźników ryzyka
- Stosujemy proces oceny ryzyka Leuze HARMONY (Hazard Rating for Machinery and prOcess iNdustrY): zapewnia to szczególnie dokładne wskaźniki ryzyka
- Ocena zagrożeń i ryzyka przez niezależne osoby
Ocena zgodności według dyrektywy maszynowej
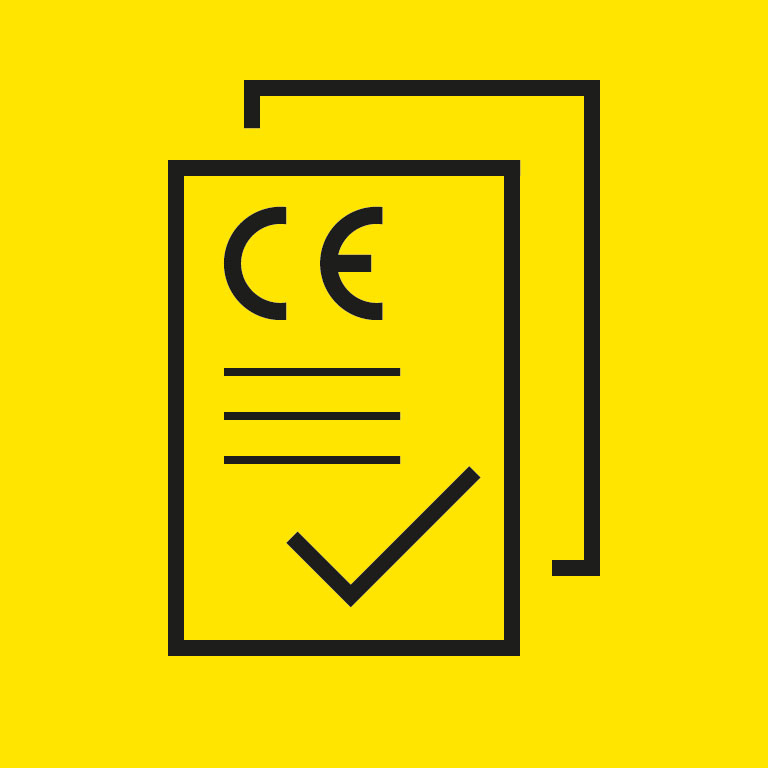
Twoje wymagania
- Jeśli maszyna jest wprowadzana do obrotu na rynku europejskim, ocenę zgodności należy przeprowadzić wcześniej. Dyrektywa maszynowa 2006/42/WE określa procedurę w tym zakresie.
- Producent potwierdza spełnienie wymagań dyrektywy poprzez deklarację zgodności UE oraz oznakowanie CE
Nasze rozwiązanie
- Wsparcie oparte na potrzebach podczas całego procesu w celu spełnienia wymogów prawnych
- Kontrola dotychczasowego stanu projektu pod kątem zawartości i kompletności, np. pod względem oceny ryzyka, konstrukcji i dokumentacji
- Propozycja treści deklaracji zgodności UE
Korzyści dla Ciebie
- Niezależne potwierdzenie, że dotrzymano wymagań dyrektywy maszynowej
- Zalecenia poprawy w razie ewentualnych odchyleń
Koncepcja bezpieczeństwa i projektowanie zgodne z bezpieczeństwem
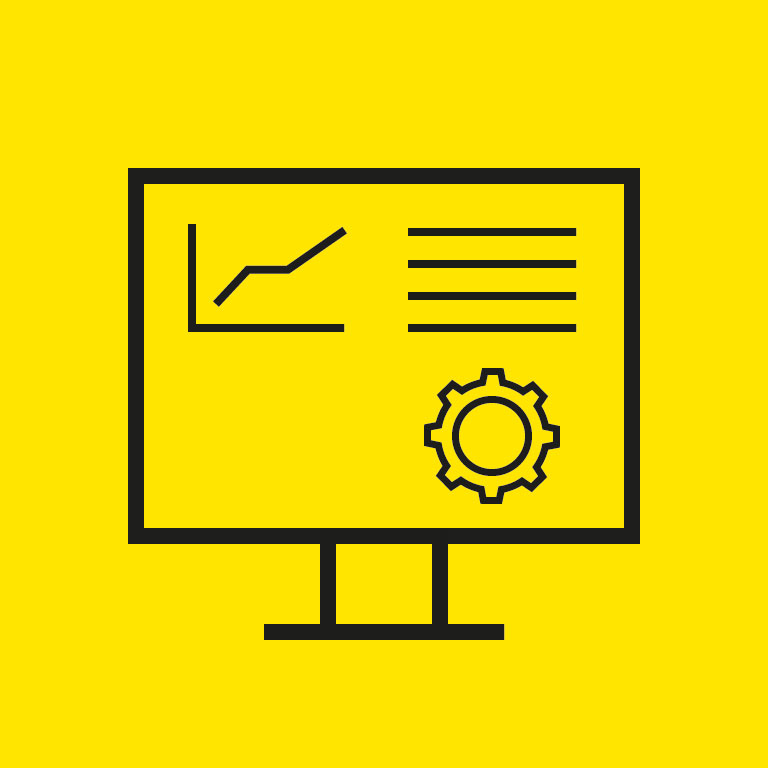
Twoje wymagania
- Stworzenie koncepcji bezpieczeństwa w oparciu o ocenę ryzyka
- Niezbędne funkcje bezpieczeństwa należy przy tym kształtować tak, żeby uwzględniając odnośne normy i przepisy, osiągnąć optimum bezpieczeństwa, ergonomii i ekonomii.
- Ważna jest prawidłowa dokumentacja funkcji bezpieczeństwa. W planie walidacji ustala się testy działania i błędów, które mają wykazać skuteczność funkcji bezpieczeństwa podczas uruchomienia.
Nasze rozwiązanie
- Naszkicowanie propozycji koncepcji zorientowanych na praktykę
- Wybór odpowiednich komponentów i utworzenie planu przyłączenia
- Programowanie części sterownika ukierunkowanych na bezpieczeństwo
- Jednoznaczna i zrozumiała dokumentacja funkcji bezpieczeństwa
- Utworzenie planu walidacji w oparciu o koncepcję bezpieczeństwa
Korzyści dla Ciebie
- Wdrożenie środków kontrolnych w funkcjach bezpieczeństwa zgodnie z wymaganiami normatywnymi
- Dzięki naszej rozległej wiedzy branżowej i wieloletniemu doświadczeniu w zakresie bezpieczeństwa możesz stworzyć optymalną koncepcję bezpieczeństwa
- Sprawdzenie koncepcji bezpieczeństwa pod kątem kompletności
- Przegląd i weryfikacja koncepcji bezpieczeństwa przez niezależnych, zewnętrznych audytorów (zasada czterech oczu)
Weryfikacja i walidacja funkcji bezpieczeństwa
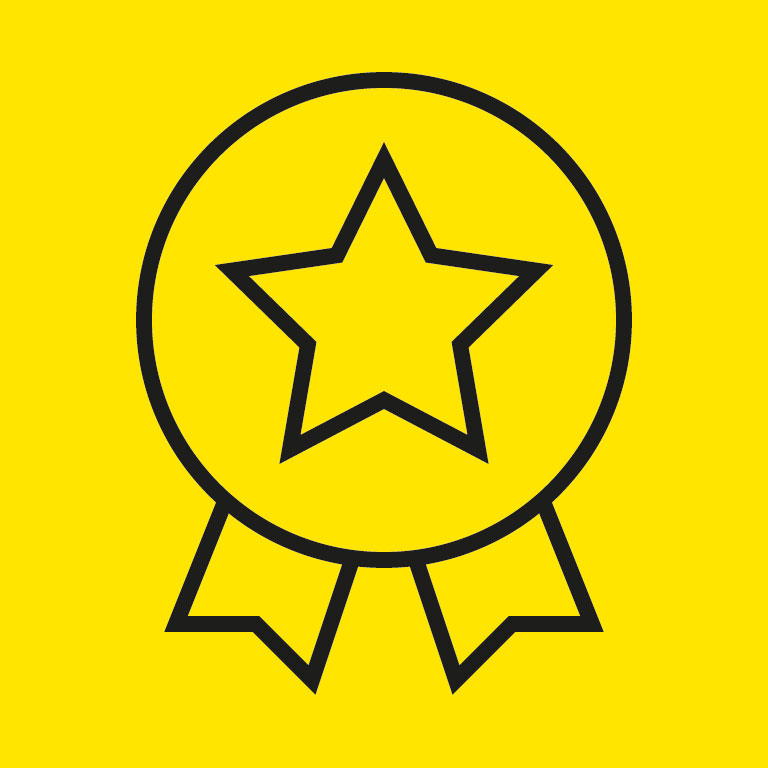
Twoje wymagania
- Należy sprawdzić bezbłędną realizację funkcji bezpieczeństwa w oparciu o koncepcję bezpieczeństwa
- Działanie funkcji bezpieczeństwa należy wykazać poprzez testy funkcjonalne i symulacje błędów
Nasze rozwiązanie
- Odpowiednie do potrzeb wsparcie przez cały czas trwania procesu
- Kontrola stanu projektu pod kątem treści i kompletności
- Planowanie i realizacja poszczególnych etapów procesu, np. definicja testu działania i utworzenie odpowiedniej dokumentacji
Korzyści dla Ciebie
- Gwarancja prawidłowego postępowania podczas implementacji funkcji bezpieczeństwa
- Wydajna realizacja niezbędnych zadań poprzez wsparcie i wskazówki od doświadczonych ekspertów
Wsparcie przy uruchomieniu
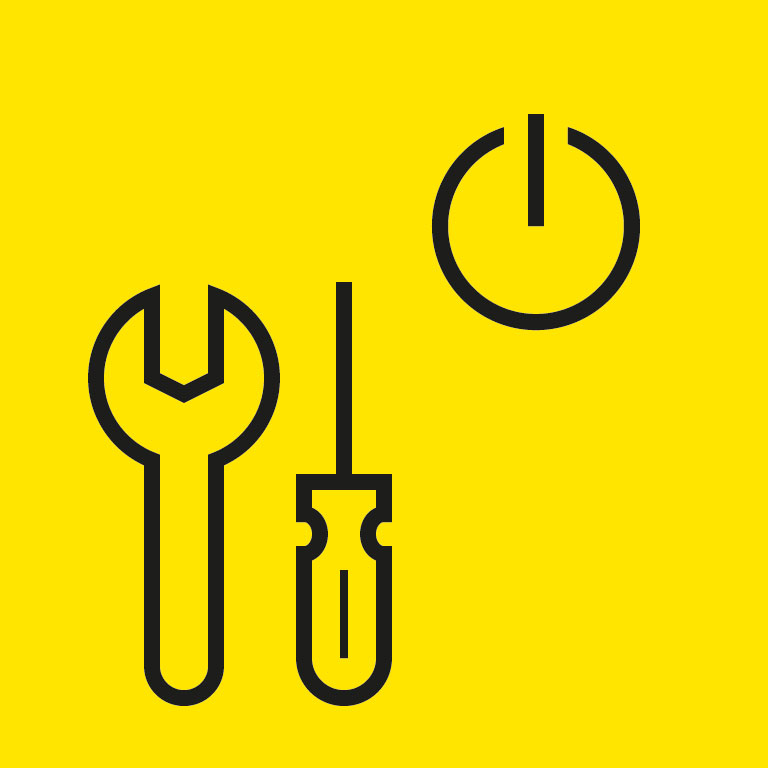
Twoje wymagania
- Szybkie i bezpieczne uruchomienie
- Optymalizacja wydajności urządzeń w aplikacji, np. poprzez ich zestrojenie w oparciu o procedurę opisaną w instrukcji obsługi
- W przypadku wymiany urządzenia
- należy przenieść konfigurację na nowe urządzenie
- należy zminimalizować czas przestoju
Nasze rozwiązanie
- Optymalne ustawienie czujników optycznych
- Wsparcie w konfiguracji i parametryzacji naszych urządzeń m.in. przy wyborze trybu pracy i parametryzacji pól ochronnych dla laserowych skanerów bezpieczeństwa
- Dostosowanie konfiguracji w razie wymiany na urządzenia nowszej generacji
- Pomoc w rozwiązywaniu problemów
Korzyści dla Ciebie
- Szybkie i bezpieczne uruchomienie przez naszych serwisantów
- Możliwe do skalkulowania koszty
- Minimalizuje przestoje w przypadku wymiany urządzenia
Kontrola urządzeń ochronnych
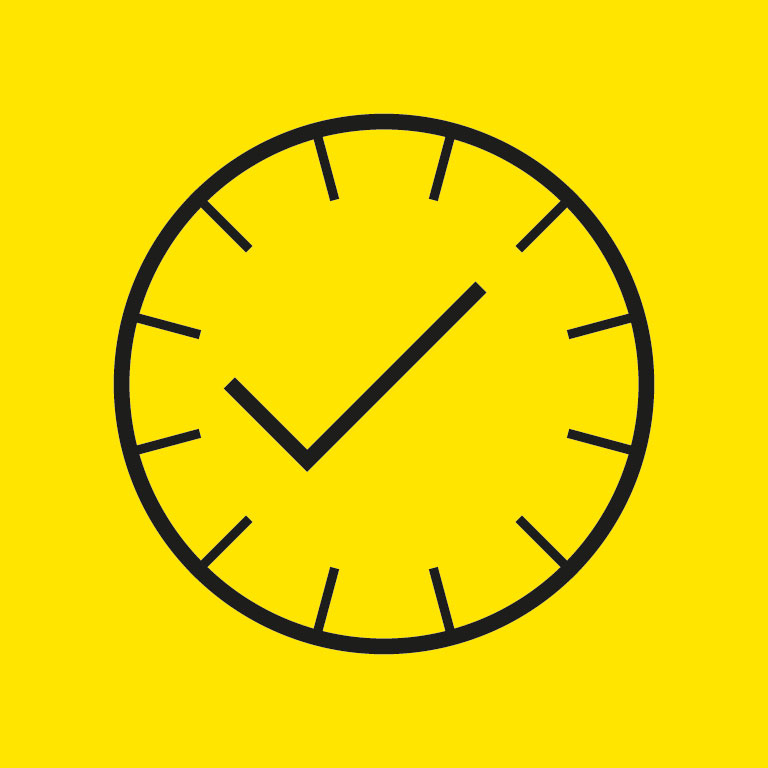
Twoje wymagania
- Bezpieczeństwo pracy jest obowiązkiem pracodawcy. Regularne przeglądy urządzeń ochronnych gwarantują przestrzeganie standardów bezpieczeństwa i jakości.
- Będąc częścią profilaktycznego planu konserwacji, przeglądy minimalizują niepożądane przestoje maszyn.
- W Niemczech rozporządzenie o bezpieczeństwie przemysłowym wymaga sprawdzania maszyn przed pierwszym uruchomieniem, a następnie w regularnych odstępach czasu. Kontrola jest konieczna również po dłuższych przestojach i zmianach wprowadzonych w maszynie.
- Kontrola i przegląd urządzeń ochronnych mogą być przeprowadzane wyłącznie przez osoby wykwalifikowane.
Nasze rozwiązanie
- Przegląd urządzeń ochronnych działających bezkontaktowo (BWS), wyłączników bezpieczeństwa i urządzeń zatrzymania awaryjnego
- Kontrola stanu, prawidłowego montażu i funkcjonowania urządzeń ochronnych oraz pewnej integracji z układem sterowania maszyny
- Sprawdzenie wymaganej normatywnie odległości bezpieczeństwa od punktu niebezpiecznego poprzez pomiar czasu opóźnienia
- Szczegółowy dziennik testowy, umieszczenie naklejki informującej o dokonanym przeglądzie
Korzyści dla Ciebie
- Minimalizacja ryzyka wypadku i przestojów maszyny
- Pewność prawna dla użytkownika dzięki potwierdzeniu standardów bezpieczeństwa i jakości
- Propozycje praktycznych rozwiązań dla szybkiego usuwania usterek bezpieczeństwa
- Niezależna, zewnętrzna ocena dokonana przez wykwalifikowaną osobę zgodnie z TRBS 1203
- Przejrzysta dokumentacja z własną bazą danych testów, opartą na ponad 20-letnim doświadczeniu
- Kontrola urządzeń ochronnych wszystkich producentów
Na miejscu w zakładzie klienta
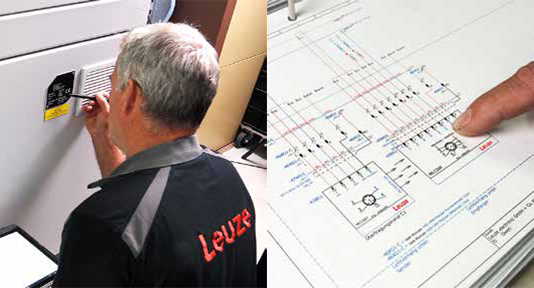
Inspekcja rozpoczyna się od zapisu danych maszyny i urządzeń ochronnych. Następnie kontrolujemy integrację techniczną urządzeń ochronnych oraz ich wyjść przełączających. Czynności te wykonywane są w trakcie pracy i bez ograniczania produktywności maszyny.
W kolejnym kroku kontrolujemy funkcjonowanie urządzeń ochronnych. W przypadku optycznych urządzeń ochronnych obejmuje to między innymi następujące czynności:
- Kontrola zdolności wykrywania i ewentualnego odbicia. Kontrola przeprowadzana jest z wykorzystaniem pręta kontrolnego dopasowanego do rozdzielczości urządzenia.
- Kontrola funkcji specjalnych, takich jak zredukowana rozdzielczość, kontrola cyklu, muting i wygaszanie
- Kontrola funkcjonowania blokady uruchomienia/ponownego uruchomienia
- Kontrola wzrokowa stanu urządzenia
Kontrolujemy prawidłowość montażu urządzenia ochronnego i oceniamy odległość bezpieczeństwa:
- Czy możliwe jest ominięcie urządzenia ochronnego, np. poprzez sięgnięcie nad nim, pod nim lub obok niego albo przechodząc przez nie?
- Czy możliwe jest przeczołganie się pod urządzeniem ochronnym?
- Pomiar czasu zatrzymania w celu określenia odległości bezpieczeństwa (jeśli to konieczne i możliwe, patrz kolejna strona).
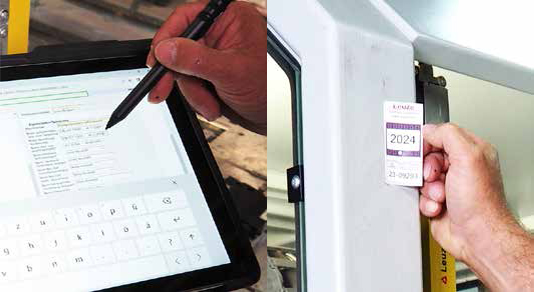
Wszystkie wyniki rejestrujemy w kontrolnej bazie danych i na tej podstawie sporządzamy przejrzysty dziennik testowy. Na zakończenie kontroli umieszczamy na maszynie naklejkę informującą o wykonanym przeglądzie, na której znajduje się także numer kontrolny dziennika testowego.
Pomiar czasu zatrzymania maszyny
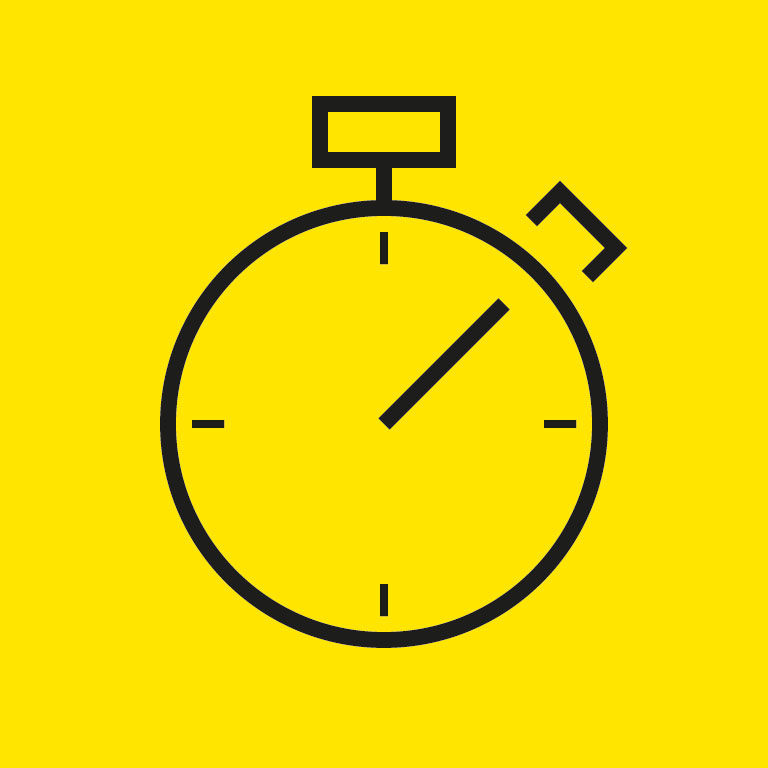
Twoje wymagania
- Do obliczenia niezbędnej odległości bezpiecznej trzeba zmierzyć czas zatrzymania maszyny. Oznacza to, że urządzenie zabezpieczające można ustawić prawidłowo: tylko odpowiednio dobrany odstęp bezpieczeństwa pomiędzy urządzeniem ochronnym a punktem niebezpiecznym gwarantuje, że ludzie nie będą zagrożeni.
- Zużycie, np. hamulców silnikowych, może wydłużyć czas zatrzymania maszyny do takiego stopnia, że urządzenie ochronne nie będzie już w stanie niezawodnie chronić operatora. Mierząc czas kontrolny, można zidentyfikować zmiany i określić niezbędne środki. Pomiar czasu zatrzymania maszyny jest zatem również częścią naszych regularnych inspekcji bezpieczeństwa.
Nasze rozwiązanie
- Fizyczny test dobiegu wszystkich zainstalowanych urządzeń ochronnych, przeprowadzany przy użyciu skalibrowanych urządzeń pomiarowych
- Ocena odległości bezpiecznej na podstawie wyników pomiarów i wymagań normy ISO 13855
- Potwierdzone i udokumentowane wyniki badań, opcjonalnie z graficzną analizą ruchu hamowania
Twoje korzyści
- Fachowo przeprowadzony pomiar czasu zatrzymania maszyny stanowi wiarygodną podstawę do obliczenia odległości bezpieczeństwa i prawidłowego umiejscowienia urządzenia zabezpieczającego
- Regularne przeglądy pozwalają na wczesne wykrywanie zużycia i gwarantują długotrwałe bezpieczeństwo maszyn
Na miejscu w zakładzie klienta
Określanie czasu zatrzymania przy użyciu specjalnego urządzenia pomiarowego
Czas zatrzymania jest określany za pomocą specjalnego urządzenia pomiarowego. Mierzy ono czas od przerwania urządzenia ochronnego aż do zatrzymania ruchów stwarzających zagrożenie:
- Na urządzeniu ochronnym – np. optoelektronicznej kurtynie bezpieczeństwa – zamontowany jest aktuator (Auto Hand), który wyzwala urządzenie ochronne
- Czujnik linkowy rejestruje ruch maszyny. W ten sposób ustalany jest czas do zatrzymania ruchów stwarzających zagrożenie.
- Pomiar wykonywany jest w miarę możliwości przy maksymalnej prędkości ruchu.
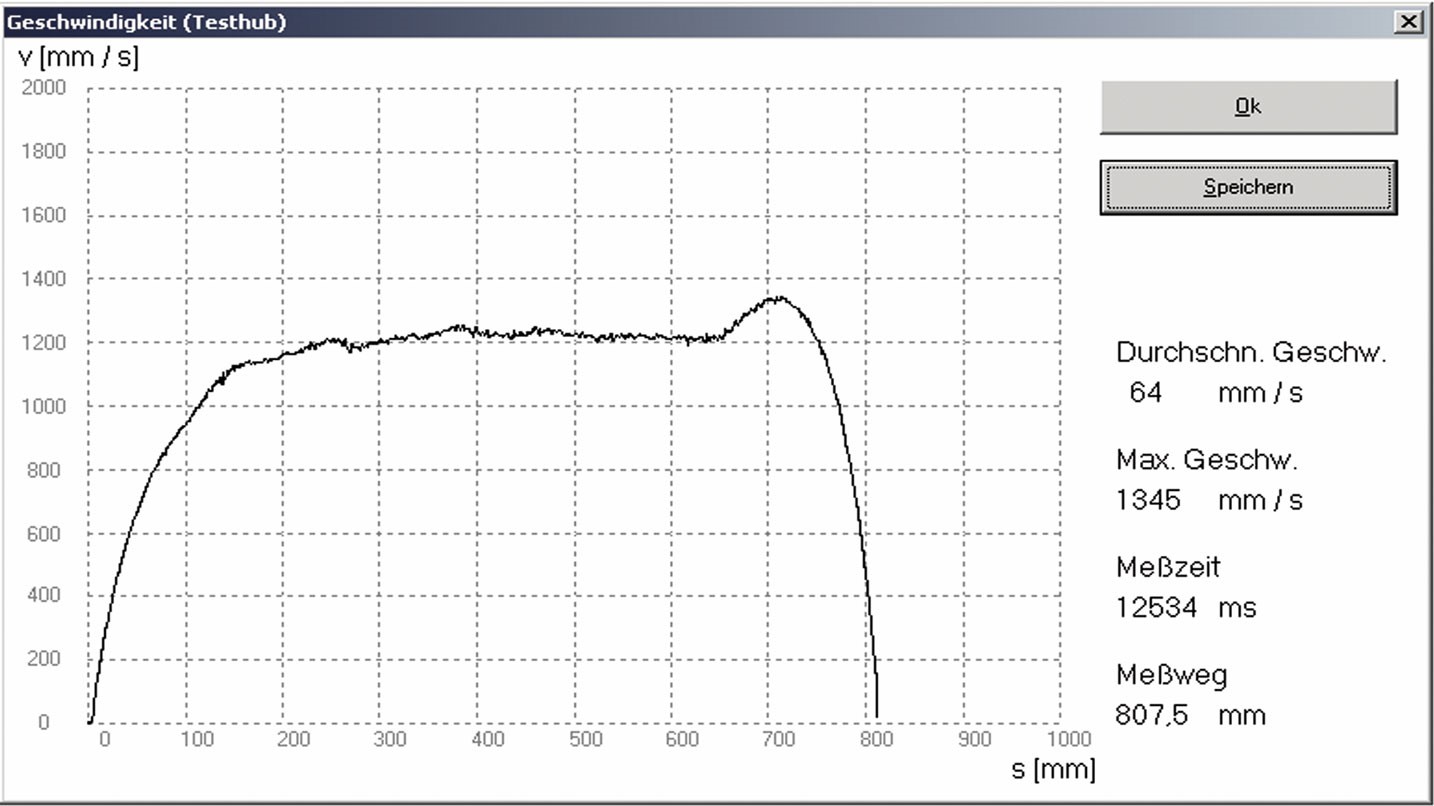
Analiza zdarzeń
Zgodnie z wymaganiami normy ISO 13855 przeprowadzamy kolejno dziesięć pomiarów. Najwyższa wartość z serii pomiarów zostaje następnie udokumentowana jako rezultat dla czasu zatrzymania i jest wykorzystywana do oceny odległości bezpieczeństwa.
W razie potrzeby dostępna jest także graficzna analiza ruchu hamującego.
Status Check „Technika bezpieczeństwa maszyn i urządzeń”
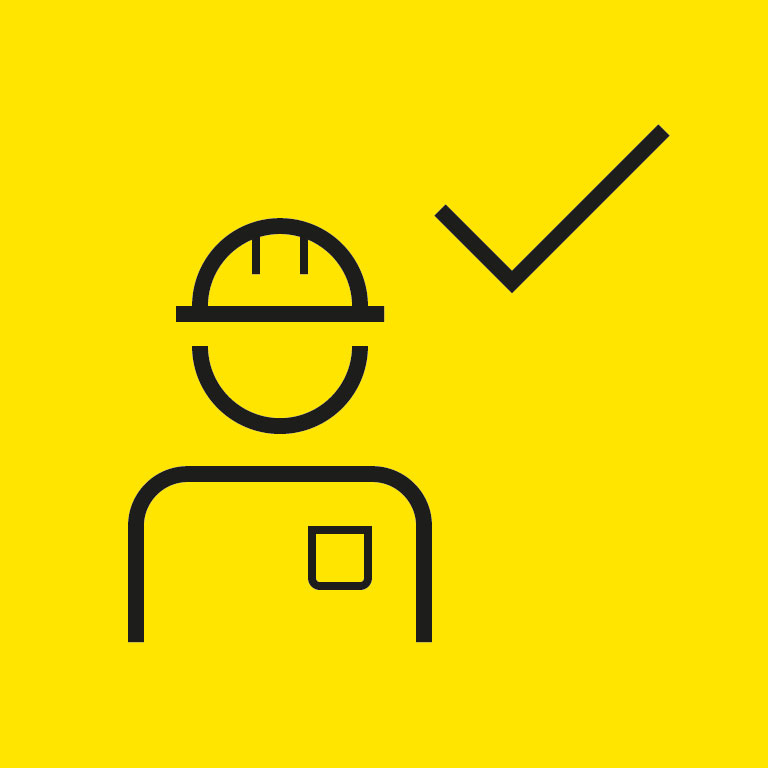
Twoje wymagania
- Jako użytkownik jesteś odpowiedzialny za bezpieczeństwo swoich maszyn. Zmiany, rozszerzenia czy zużycie mają wpływ na stan maszyn i stosowanych urządzeń ochronnych.
- Konieczny jest wiarygodny przegląd stanu parku maszynowego, aby można było określić możliwe zapotrzebowanie na działania związane z bezpieczeństwem maszyn.
Nasze rozwiązanie
- Nasi eksperci zajmą się fachową identyfikacją, opisem i oceną istniejących ryzyk dla zagrożeń mechanicznych w Twoich maszynach i instalacjach
- Zapis rzeczywistej sytuacji jest przeprowadzany na podstawie obchodu na miejscu
- Wyniki kontroli zbieramy w szczegółowym raporcie, obejmującym wskaźnik ryzyka dla każdej maszyny
Korzyści dla Ciebie
- „Status Check” identyfikuje zagrożenia dla pracowników oraz odchylenia od zaleceń ustawowych
- Wyniki są zaleceniami dla szybkich reakcji w razie nagłych zagrożeń
- Dla każdego zagrożenia ustalamy wskaźnik ryzyka. Ułatwia to ustalenie priorytetów niezbędnych działań korygujących.
Ocena zagrożenia
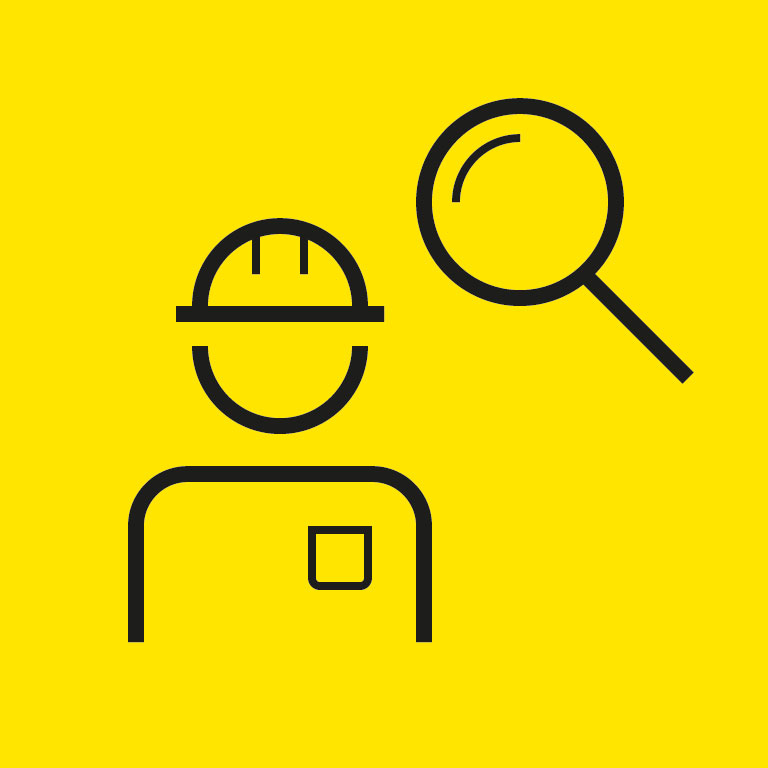
Twoje wymagania
- Jako użytkownik jesteś zobowiązany do regularnego przeprowadzania oceny ryzyka zgodnie z aktualnym stanem wiedzy na podstawie rozporządzenia w sprawie bezpieczeństwa i higieny pracy.
- Jeśli w okresie eksploatacji maszyny wystąpią modyfikacje, rozbudowy lub zużycie, należy wykryć odchylenia pomiędzy stanem docelowym związanym z bezpieczeństwem a stanem rzeczywistym.
Nasze rozwiązanie
- Analiza istniejących zagrożeń mechanicznych
- Ocena istniejących zagrożeń i obliczenie wskaźnika ryzyka
- Raport z opisem potrzebnych działań
Korzyści dla Ciebie
- Zgodne z prawem wdrożenie wymogów rozporządzenia w sprawie bezpieczeństwa i higieny pracy
- Gwarancja bezpiecznego otoczenia roboczego
- Specyficzne dla maszyn wytyczne i badania standardów
- Niezależna, zewnętrzna ocena z szeroką wiedzą na temat zagrożeń związanych z porównywalnymi maszynami