integrated connectivity
시스템 내 센서와 인터페이스의 완벽한 팀워크는 시운전, 기계 모니터링, 프로세스 최적화에 이점이 됩니다. 로이체는 "integrated connectivity" 컨셉을 통해 이를 가능하게 합니다.
모든 것을 담은 센서
integrated connectivity는 모든 산업용 이더넷 인터페이스를 지원하여 이를 통해 중앙 장치 기능을 사용할 수 있도록 하는 것을 말합니다. 간단해 보이지만 이는 아직 시장에서 기본형으로 통용되고 있지 않습니다. 제조사는 이와 같은 제품 대신 산업용 이더넷 인터페이스를 지원하지 않는 제품을 제공함으로써 개발 비용을 절감하는 경우가 많습니다. 이 경우 인터페이스는 게이트웨이를 통해 제공됩니다. 다음 예시는 이것이 최적의 솔루션이 아닌 이유, 그리고 시스템 운영자로서 로이체의 integrated connectivity를 사용하는 것이 큰 이점이 되는 이유를 보여줍니다. 시운전(Device Management), 기계 모니터링(Condition Monitoring)부터 프로세스 최적화에 이르기까지 이점은 다양합니다.
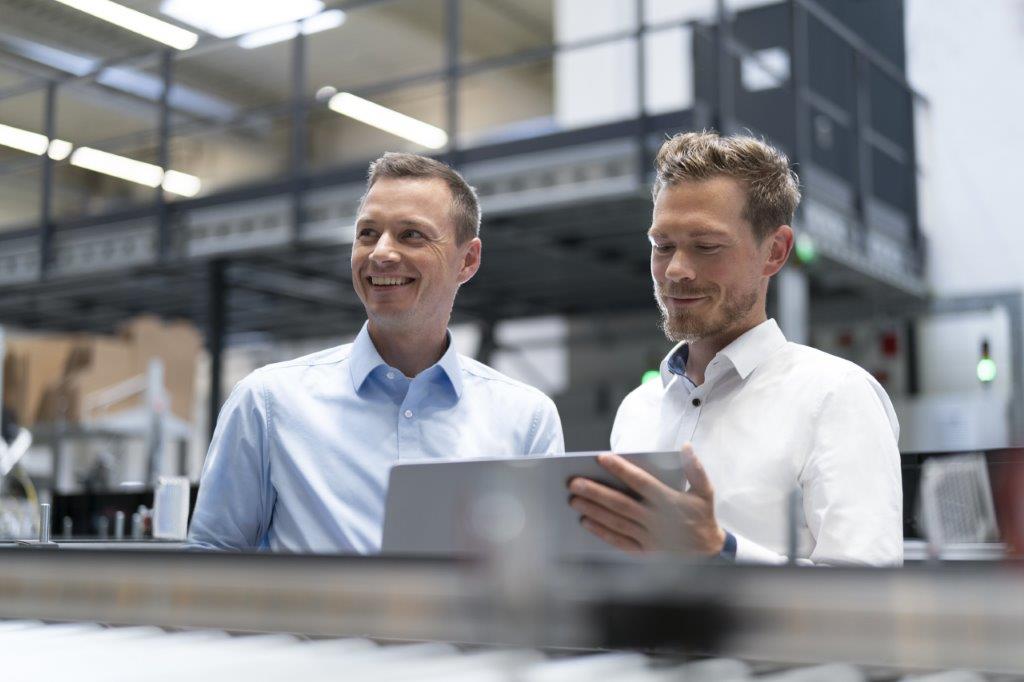
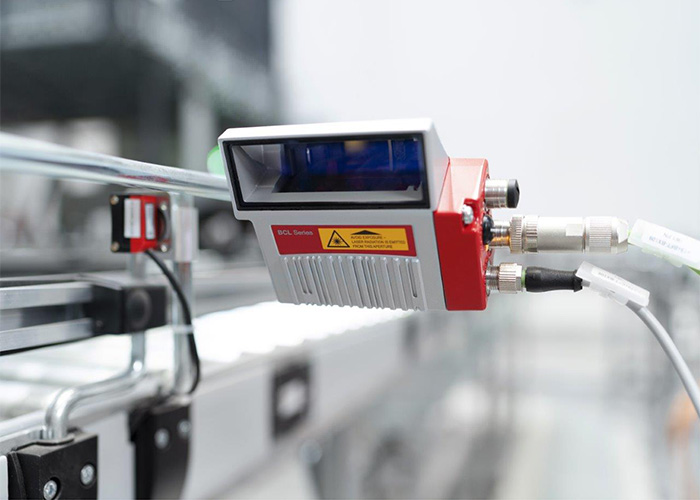
Device Management, Condition Monitoring 및 프로세스 최적화 시 integrated connectivity의 이점
훨씬 더 슬림해진 시스템 레이아웃
로이체는 PROFINET, Ethernet/IP, EtherCAT용 통합 인터페이스를 갖춘 장치를 제공합니다. 이것이 시운전 시 얼마나 많은 이점을 제공하는지는 integrated connectivity가 구현된 시스템 디자인과 그렇지 않은 시스템 디자인의 예를 보면 알 수 있습니다. 먼저 통합 인터페이스를 갖추지 않은 바코드 리더의 시스템을 살펴보겠습니다. 이 시스템에서는 각 스캐너를 별도의 게이트웨이에 연결해야 합니다. 자체 전원 공급 장치가 있는 추가 게이트웨이를 바코드 리더당 하나씩 연결해야 한다는 것입니다. 따라서 설치 비용과 케이블 수는 두 배가 되고 파라미터 설정 과정도 확실히 복잡해집니다. 또 잊지 말아야 할 점은 게이트웨이가 필요해지면서 장애를 일으킬 수 있는 시스템 장치가 늘어나 점검해야 할 장치도 많아진다는 것입니다. 그에 비해 integrated connectivity가 구현된 동일 시스템의 각 바코드 리더에는 산업 Ethernet 인터페이스가 이미 통합되어 있어 별도의 게이트웨이가 필요하지 않습니다. 또한 시스템이 훨씬 간결해져 필요한 케이블 수가 줄어들고. 궁극적으로 점검해야 할 장치가 줄어 장애 해결 시간도 단축됩니다.
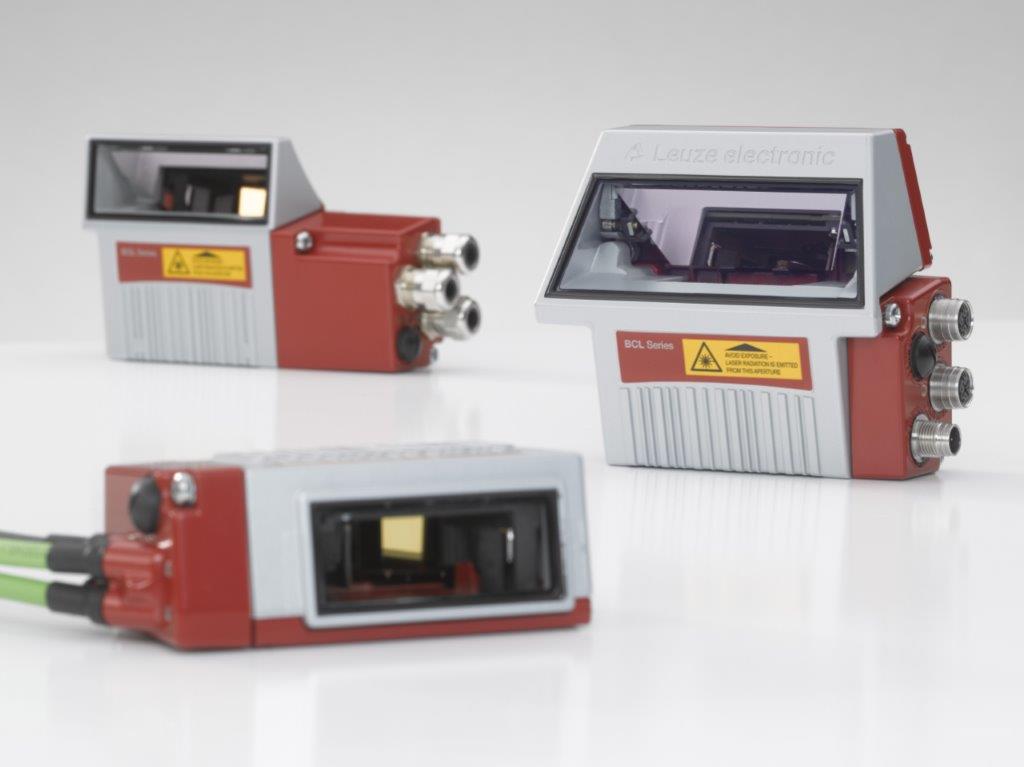
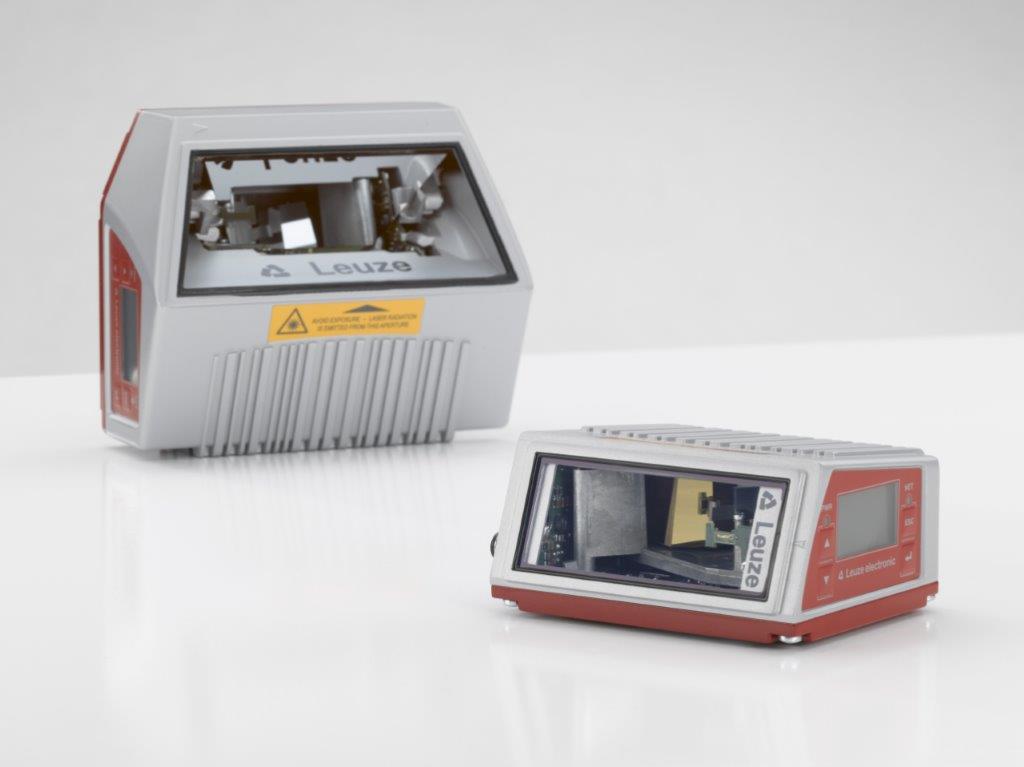
Leuze의 BCL 시리즈 바코드 리더에는 "integrated connectivity" 기능이 탑재되어 있습니다.
Switch included
로이체의 integrated connectivity 콘셉트 센서가 주목받는 또 다른 이유는 효율적인 시운전입니다. 기본적으로 장치에 Ethernet 입력 포트, 출력 포트당 하나씩 스위치가 포함되어 있어 시스템 운영자는 별도의 외부 스위치가 필요하지 않습니다. 여러 개의 장치도 링 토폴로지 또는 라인 토폴로지 등으로 훨씬 손쉽게 연결할 수 있습니다. 선형 배선 시 시스템 운영자는 통합 스위치를 통해 한 센서를 다음 센서에 연결합니다. 이 열에서 마지막 센서가 제어 장치와 연결됩니다. 이 방식의 경우 시스템 디자인이 더욱 단순해지고, 필요한 케이블 수도 줄어든다는 장점이 있습니다. 반면 통합 스위치가 없는 장치에는 Ethernet 스위치가 필요합니다. 그리고 사용자는 각 개별 센서를 스타 토폴로지로 스위치에 연결한 후 이를 제어 장치에 연결해야 합니다.
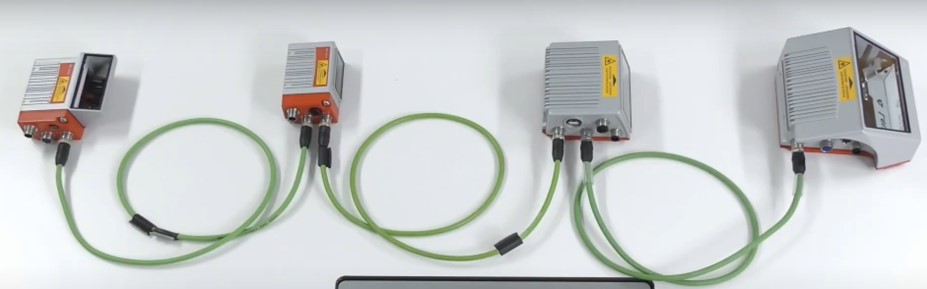
통합 스위치로 라인 토폴로지를 구현하면 배선 작업이 줄어 시간과 비용이 절약됩니다.
익숙한 제어 환경
integrated connectivity는 익숙한 제어 환경에서 작업할 수 있음을 의미하기도 합니다. 전체 장치 파라미터 설정이 PROFINET의 GSDML("Generic Station Description Markup Language") 파일 등에 통합되어 있기 때문입니다. 시중의 다른 여러 Ethernet 기반 장치에서는 일반적으로 웹서버를 통해 파라미터를 설정해야 합니다. 각 제조사가 자체 사용자 인터페이스를 갖춘 자사 웹서버 버전을 제공하기 때문에 이 과정은 복잡할 수 밖에 없습니다. 사용자는 매번 각 웹서버를 익히고, 관련 기능을 찾아봐야 합니다. 또한 Ethernet을 지원하지 않는 장치는 게이트웨이를 통해 연결해야 하므로 파라미터 설정을 위해 제품별 제조사 소프트웨어를 사용해야 하는 경우가 많습니다. 여기서 사용 하드웨어와의 호환성 문제가 발생할 수도 있습니다. 제조사가 몇 년 후 더 이상 소프트웨어를 관리하지 않는 경우 이같은 문제가 발생합니다. 여기서도 integrated connectivity는 여러 방면에서 빛을 발합니다.
- 사용자는 익숙한 소프트웨어 환경을 벗어나지 않아도 되고
- 제조사 소프트웨어 설치와 이 소프트웨어를 익히는 과정이 필요하지 않으며
- 웹서버에 대한 접근도 필요하지 않기 때문입니다.
integrated connectivity가 구현된 Leuze의 장치는 파라미터 설정이 간편합니다. 로이체 웹사이트에서 GSDML 파일을 로드한 후 이를 고객의 엔지니어링 소프트웨어에 한 번 복사하기만 하면 됩니다. 이를 완료하고 나면 하드웨어 카탈로그의 모듈을 사용할 수 있습니다. 여기에는 장치 기능이 상세히 설명되어 있습니다. 이로써 파라미터 설정과 센서 사용이 매우 간편해지고 매뉴얼도 거의 불필요해집니다.
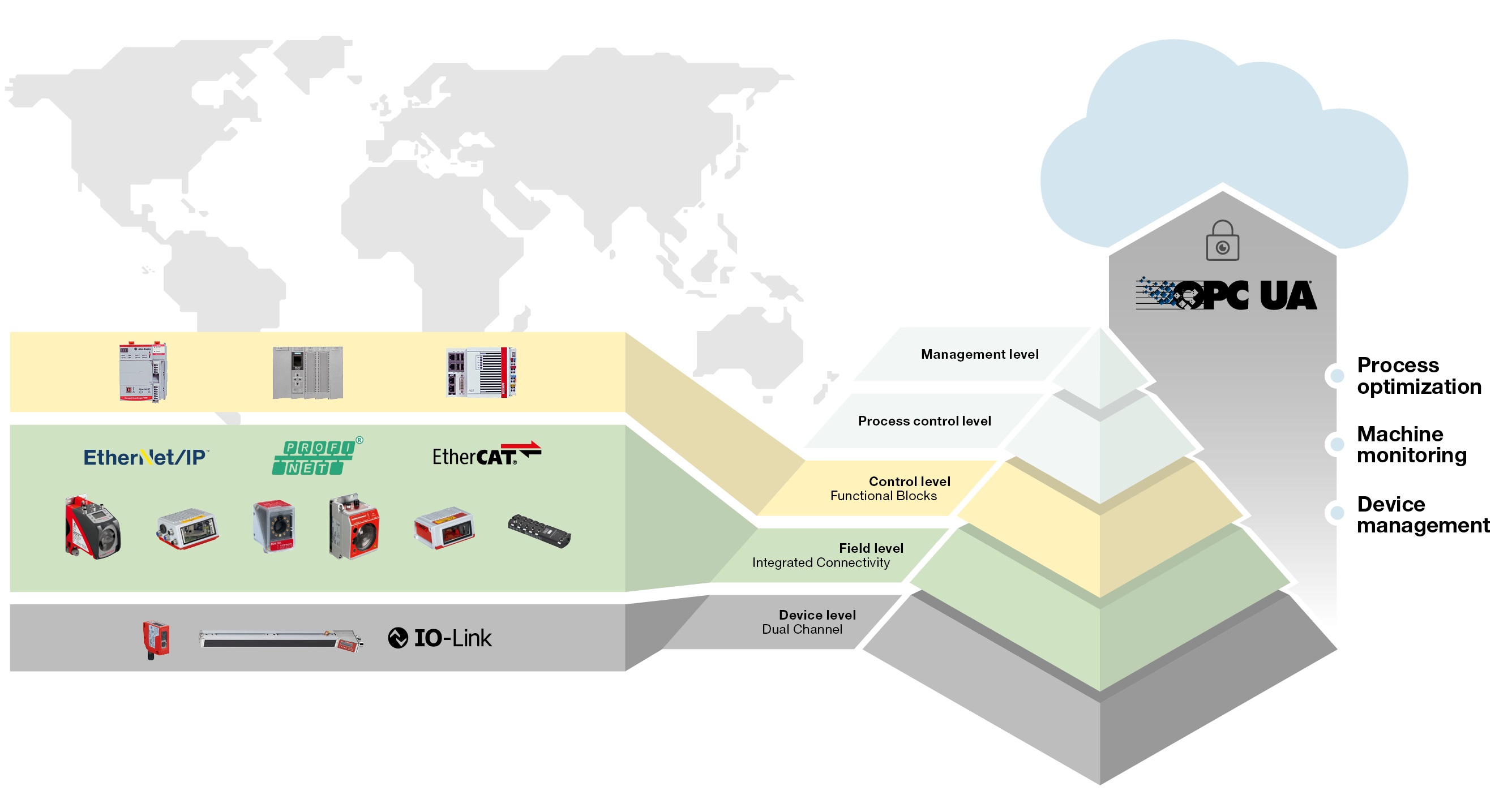
센서의 지원
integrated connectivity가 구현된 센서의 장치 프로필을 살펴보면 프로그래밍이 더욱 단순화됨을 알 수 있습니다. 예를 들어 로이체는 AMS 및 BPS 위치 설정 센서에 위치값과 계산된 속도값을 모두 제공합니다. 따라서 시스템에 이 값이 필요한 경우 직접 계산하는 데 걸리는 시간을 절약할 수 있습니다. 또 integrated connectivity 기능 없이 특정 바코드만 필터링하려는 경우에는 제어 장치를 통해 이를 수행해야 합니다. 이때 로이체의 바코드 리더 BCL을 사용하면 특정 기준에 따른 사전 필터링이 가능해 더욱 효율적입니다. BCL에서는 원하는 패턴과 일치하는 코드만 제어 장치에 전송되고 PROFINET 장치를 엔지니어링 도구에서 복제하는 데 걸리는 시간도 절약됩니다. 사용자는 파라미터를 한 번 설정하기만 하면 됩니다. 설정을 완료한 후에는 원하는 대로 설정을 복사할 수 있습니다. integrated connectivity 기능은 장치 교체 시에도 도움이 됩니다. 손상된 센서를 교체해야 할 때 시스템은 제어 장치에 저장된 모든 파라미터를 새 장치로 자동 전송합니다. 따라서 새 센서를 바로 사용할 수 있게 됩니다.
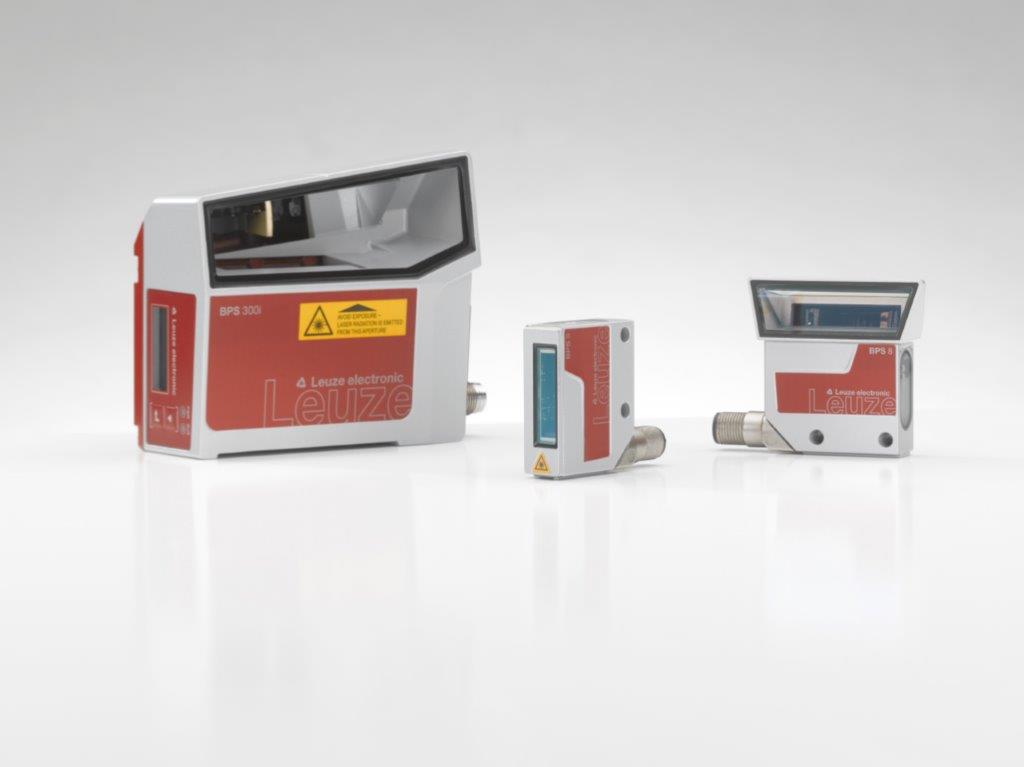
바코드 위치 확인 시스템 BPS 300i(그림 좌측)에는 integrated connectivity 기능이 탑재되어 있습니다.
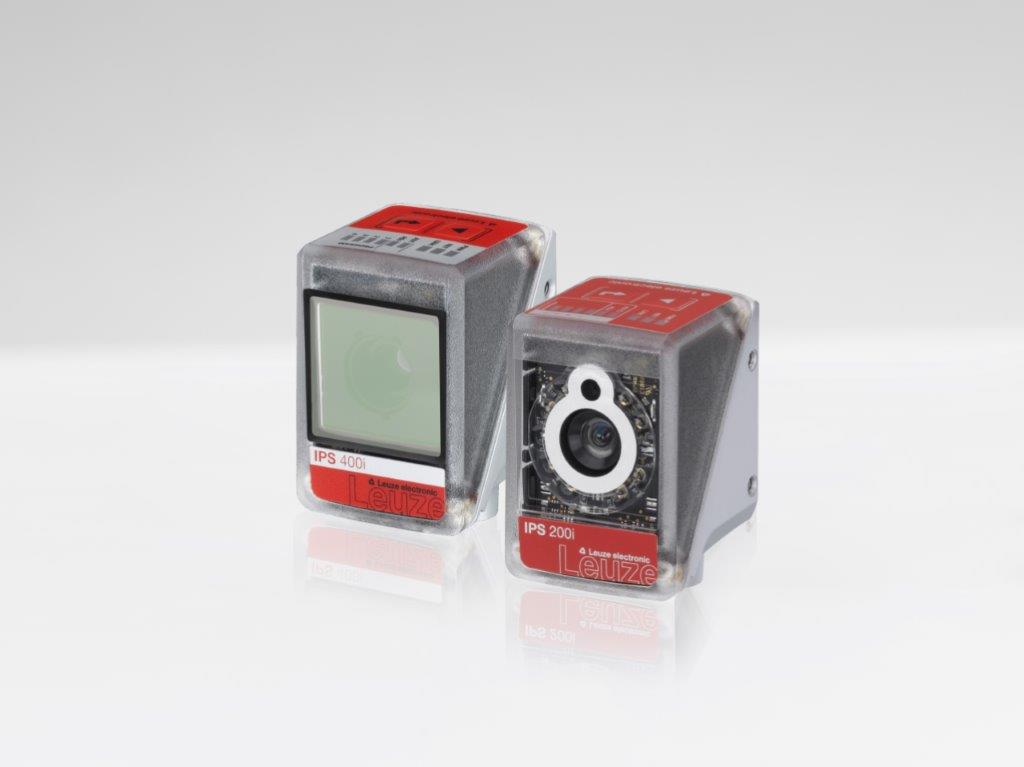
물류 산업 분야의 정밀 위치 설정을 위한 센서 IPS 200i/400i에는 integrated connectivity 기능이 탑재되어 있습니다.
한 눈에 품질 확인
integrated connectivity는 시운전뿐만 아니라 기계 모니터링(Condition Monitoring) 과정도 지원합니다. 효율적인 운영을 위해 시스템 운영자는 시스템이 오류 없이 작동되고 있는지, 유지 관리를 언제 계획해야 할지에 대한 질문에 답해야 합니다. 통합 인터페이스는 그 대답을 제공합니다. 통합 인터페이스는 산업 Ethernet 통신을 통해 제어 장치에서 사용할 수 있는 실제 프로세스 값과 진단 데이터를 전송합니다. 따라서 하나의 바코드 리더로 장치 관리에 필요한 모든 식별 데이터를 판독할 수 있습니다. 여기에는 센서의 소프트웨어/하드웨어 버전 또는 일련번호와 OK/NOK 판독값 수 등의 다양한 진단 파라미터도 포함됩니다. 특히 바코드 리더가 있는 시스템은 각 개별 코드 판독건에 품질 마크도 제공합니다. 이는 판독건의 품질 정보를 나타냅니다. 일반적으로 90~95% 사이의 값이 표시되며, 이를 통해 작동 중 발생하는 편차를 확인할 수 있습니다(예: 오염 또는 기계 손상으로 인한 편차). OPC UA를 추가 통신 채널로 사용해 원격 모니터링을 구현하는 것도 가능합니다. 제어 장치를 통해 이를 구현할 수도 있지만, 로이체 센서를 사용하면 훨씬 더 편리해집니다. OPC UA를 통해 직접 액세스할 수 있기 때문입니다. 따라서 시스템 운영자는 진행 중인 프로세스와 장치를 동시에 지켜봄으로써 시스템이 얼마나 원활히 작동 중인지를 언제든지 파악할 수 있게 됩니다. 원하는 경우 이 데이터를 제한 없이 클라우드에 업로드할 수도 있습니다.
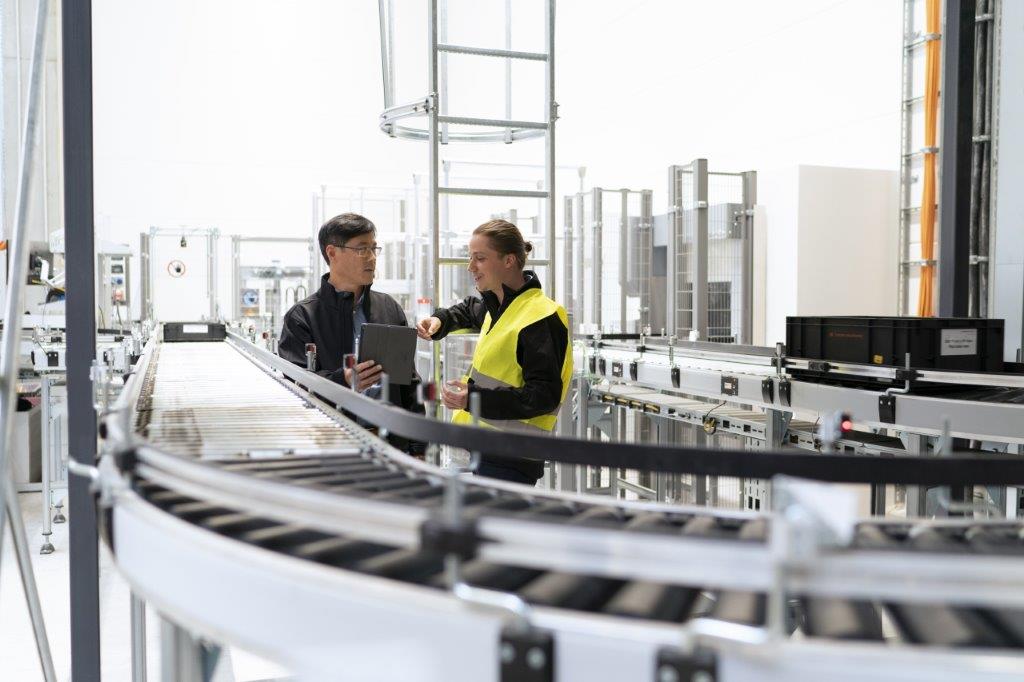

integrated connectivity는 시운전 시 이점을 제공하고 프로세스를 최적화하며 최상의 시스템 운용 조건을 만들어줍니다.
손쉽게 프로세스 최적화
수집된 데이터로 어떻게 프로세스를 최적화할까요? 바코드 리더를 사용한 두 가지 사례를 보면 답을 알 수 있습니다. 첫 번째 사례는 센서의 확인창이 오염된 경우입니다. 이러한 상황이 몇 년 후에야 발생하는 시스템도 있고, 더 빨리 발생하는 시스템도 있습니다. OPC UA를 통해 데이터를 평가하면 어떤 센서가 오염되었는지를 제때 확인할 수 있습니다. 소프트웨어는 데이터를 이용해 각 개별 디코딩 절차의 판독 품질을 기록하고, 판독 성능이 나빠진 바코드 리더에 대한 유지 관리를 제안합니다. 두 번째 사례는 라벨 자체가 문제의 원인이 되는 경우입니다. 코드가 손상되었거나 인쇄 상태가 불완전한 상황이 여기에 포함됩니다. 이러한 경우 개별 센서를 관찰하는 것만으로는 오류를 확인하기 어려우므로 여러 측정 스테이션에 걸쳐 이상이 있는 라벨을 추적하여 이를 식별해야 합니다. 이같은 방식으로 평가 결과가 유사한 곳을 파악한 후 식별 번호를 이용해 어떤 라벨에 이상이 있는지 결론을 도출할 수 있습니다.
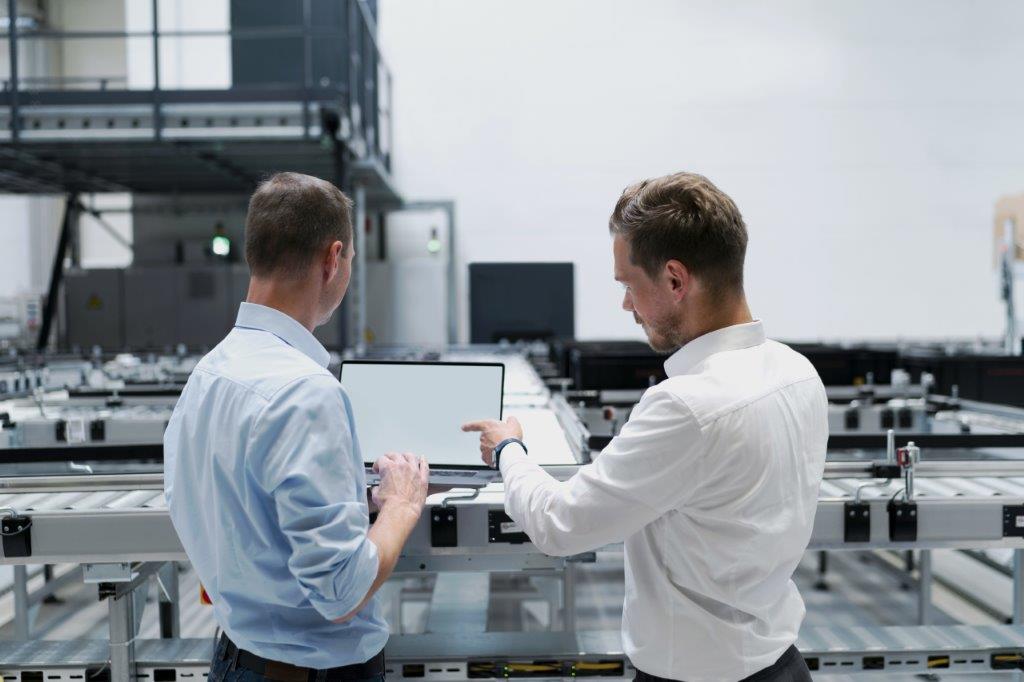
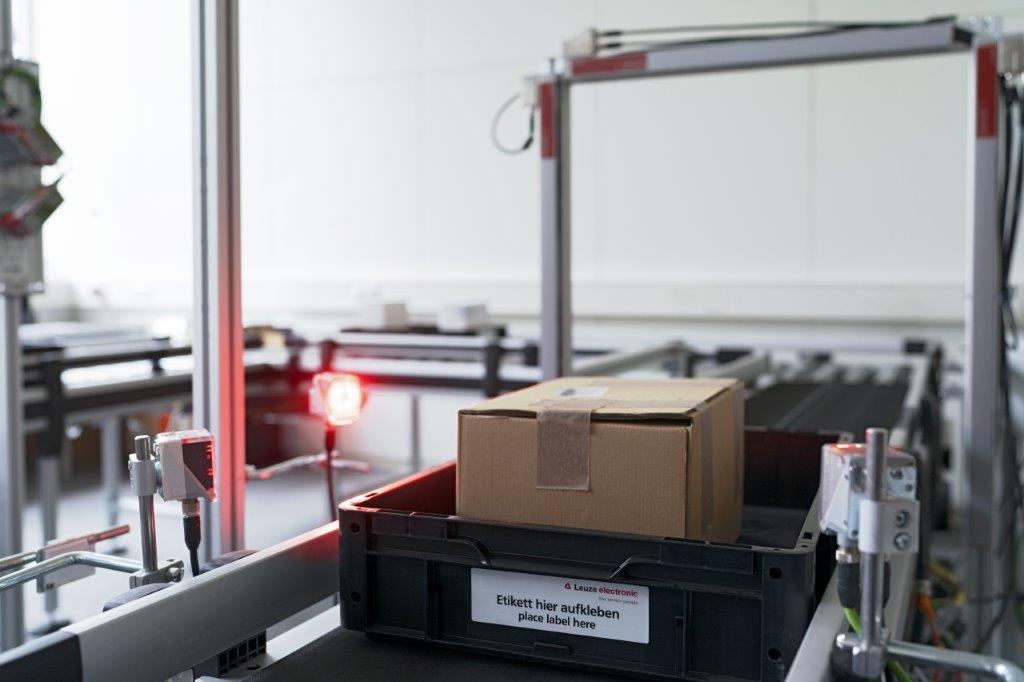
최적의 시스템 작동을 위한 integrated connectivity
3차원의 효율 향상
integrated connectivity는 여러 방면에서 이점을 제공합니다. integrated connectivity를 구현하면 시운전이 간편해지고, 기계 모니터링에 관한 추가 정보가 제공됩니다. 이 정보를 토대로 특히 프로세스가 최적화되면 시스템을 최상의 조건으로 운용할 수 있게 됩니다. 물류 산업 등의 필드버스 제어식 자동화를 위해 로이체가 개발한 모든 센서에는 integrated connectivity가 구현되어 있습니다. 이 기술은 시스템 운영자의 시간과 비용을 줄여줍니다.