Let it flow
The future of intralogistics is quiet and virtually unnoticeable. Automated guided vehicles glide across the factory floor, loading docking stations with the utmost precision – and this happens almost silently. If it wasn't for the noise of the machines working, you'd be able to hear the hearts of intralogistics providers beat faster with joy.
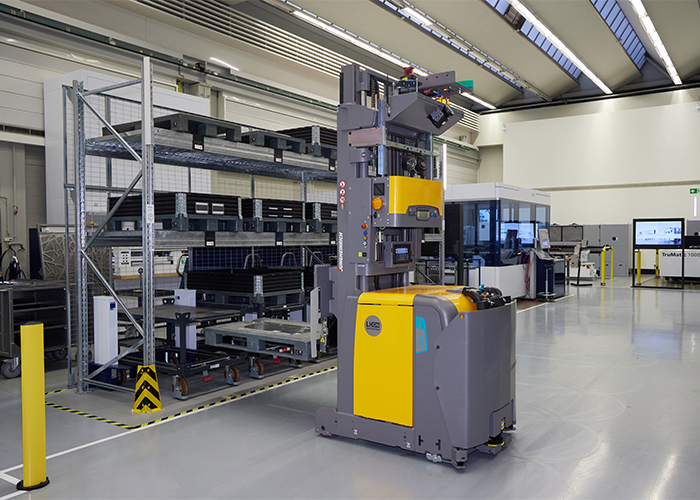
The good news is that this kind of efficient production, in which people, machinery, floor conveyors and storage systems are combined into a unified intralogistics system, is no longer just a vision. It is already possible today – TRUMPF offers its customers this solution under the term "smart material flow". And the sensor expert Leuze is also on board: Its sensors help with presence detection, data acquisition and safety.
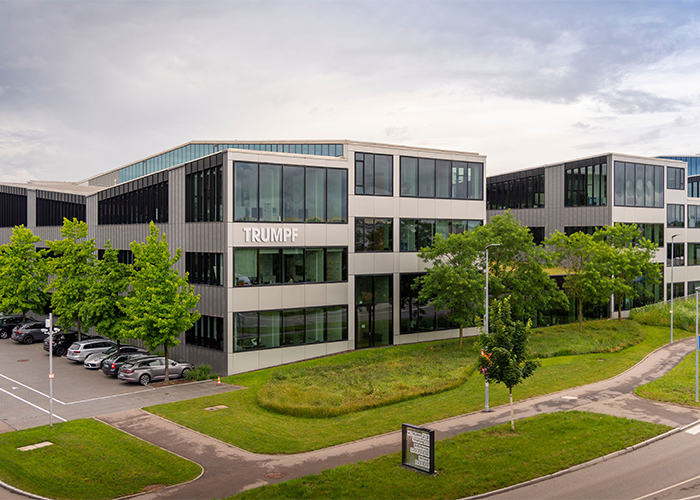
TRUMPF has made a name for itself: With a turnover of around 4.2 billion euro (2021/22), the high-tech company based in Ditzingen (Germany) offers its customers production solutions for machine tools and laser technology. TRUMPF has approx. 16,500 employees at more then 70 locations around the world. The company supports its customers not only with individual machines but, if desired, elevates the entire intralogistics system of manufacturing enterprises to a whole new level. And this pays off for TRUMPF customers: Non-value-adding activities – such as searching for materials, transporting sheet metal parts or administrative order booking activities – account for up to 40 percent of resources in a conventional manufacturing operation. Manuel Schwestka knows that smart material flow makes things much better. The Software & Automation product manager at TRUMPF is an expert in intelligent automation solutions: "With our approach, all machines, processes, interfaces and above all people play a role. We bring everything into harmony." A digital depiction of the production plant, including all components and storage locations forms the foundation. Based on this, the entire production process can be systematically planned and controlled.
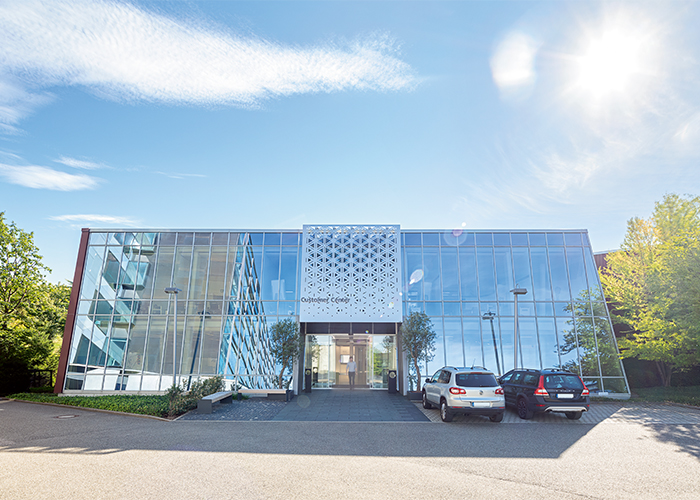
Anyone wanting to get an impression of this kind of smart material flow should visit one of the 16 TRUMPF Customer Centers dotted around the world. For example at the headquarters in Ditzingen. Since 1987, the company has presented the entire process chain for sheet metal plate there based on its current product range – from individual machine tools to fully automatic production solutions. Machines involving different technologies are demonstrated to customers. Time and feasibility studies as well as the production of sample parts also belong to the core activities of the team.
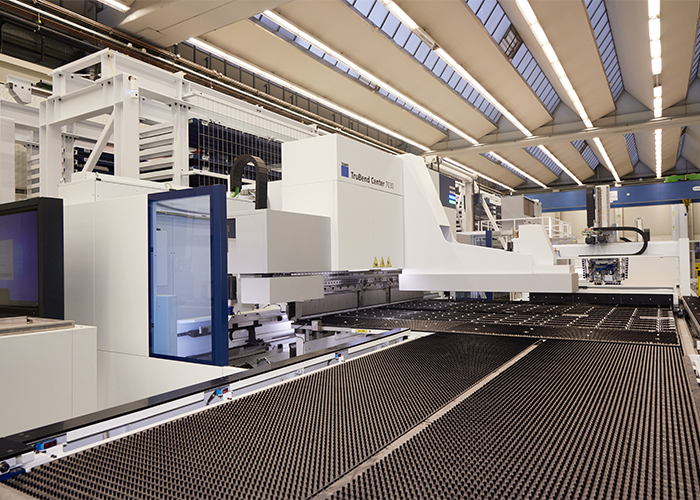
The process chain for sheet metal plates essentially consists of the following steps: e.g. punching, cutting, bending and welding. For each of these steps, TRUMPF offers the appropriate devices: e.g. 2D laser cutters, swing bending and punching machines as well as laser welding systems. Docking stations are the element that connects all workplaces. They are a key part of a smart intralogistics system: "A docking station can best be described as a 'material depot' for workplaces and machine tools," says Manuel Schwestka. "It is therefore the place where, in combination with the TRUMPF software Oseon, all material movements between the workplaces can be automatically captured and registered. Furthermore, the docking station also serves as a safe and defined handover location for automated guided vehicles (AGV)." These vehicles deliver pallets with or without material to the docking stations assigned to them. To ensure that handovers takes place automatically and efficiently, appropriate sensor solutions are needed. During the design phase, the Sensor People from Leuze provided assistance in an advisory capacity: In the area of intralogistics, Leuze has profound application know-how and extensive experience with innovative and reliable sensor solutions for use in automated environments. Based on the requirements of the customer, all docking stations at the Customer Center in Ditzingen were equipped with sensors along the sheet metal process chain.
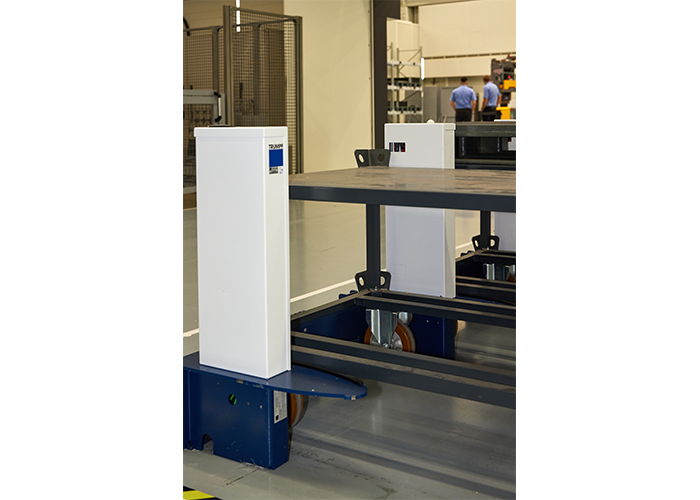
The processes at a docking station are as follows: An AGV – or alternatively a manually operated high-lift truck – loads a station with an empty or full pallet. The pallet is in turn placed on a roller carriage which the employees can pull out of the docking station to e.g. their workplace or machine tool closeby. In this way, workplaces can be conveniently supplied with the necessary parts. Employees do not have to walk far to get more of the parts they need. A major advantage is the digital depiction of the processes: Each docking station registers material movements automatically when depositing or removing a pallet. These movements are fed into the Oseon's transport control system using the OPC UA data exchange standard. The docking station is therefore a source of information for incoming and outgoing material movements and also a temporary storage location in the immediate vicinity of various workplaces.
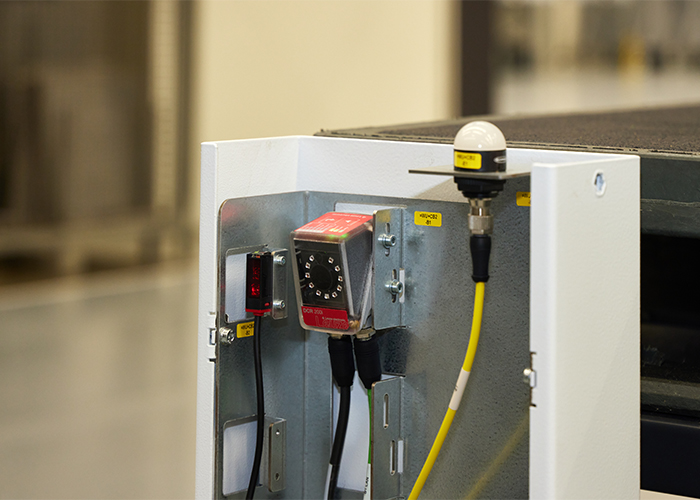
Leuze sensors are used for operation of the docking station as well as for transmitting data to the system. A docking station usually has three sensors: A HT5.1/4X sensor is installed at the bottom of the station. It detects the presence of a carriage. A further sensor of this type is at the top of the docking station. Its task is to register the presence of pallets. If a pallet is detected, the HT5.1/4X starts identification of the pallet via a further sensor.
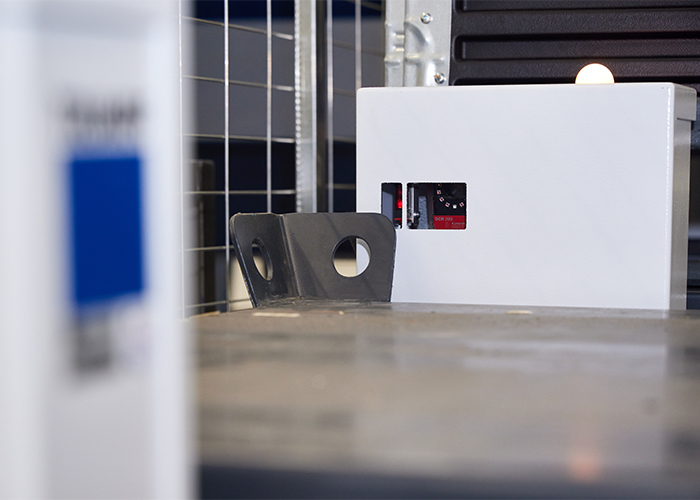
A DCR202iC is installed for this purpose: The scanner captures order and material data via the 2D-code on the pallet and transmits the data to the transport control system. Based on the information from the docking stations, the Oseon software notifies the shopfloor employees exactly when and where which order is to be retrieved or temporarily stored or whether it is to be transported to a specific workplace. To do so, the system orients itself to existing order data from the production plan. From this, the TRUMPF software Oseon automatically generates transport processes from A to B and forwards them to employees or AGVs. Together with the associated docking stations at the workplaces, this results in a truly smart material flow.
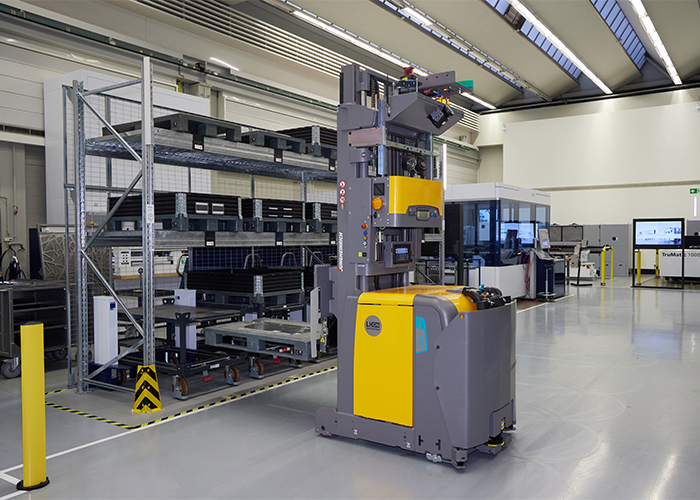
For intralogistics, this interaction between sensor technology and software brings with it considerable benefits, explains Mario Mörk, Software and Process Solutions group manager at TRUMPF: "Thanks to the sensor system of the docking stations, we always know whether there is still space at the material depot of the next workstation. If there is, the Oseon production planning software sees to it that the next load of appropriate material is brought to the workstation or a transport order is generated. The order is then passed on to a person with a tablet or to an AGV and processed following a dynamic sequence." The order in which tasks are completed depends on e.g. the priority of the customer orders. Thanks to the Leuze sensors, pallets are booked or registered at the workplace automatically – this saves time. In addition, a certain degree of flexibility is ensured because employees can, if required, also be inserted into the process using the system. This may be necessary if, for example, a company manufactures products in several, physically separated buildings. In this case, the AGV transports material as far as the boundary of the building and a person then transfers this material across the outer periphery between the buildings. Urgent orders too can be inserted into the workflow at any time by the responsible employees.
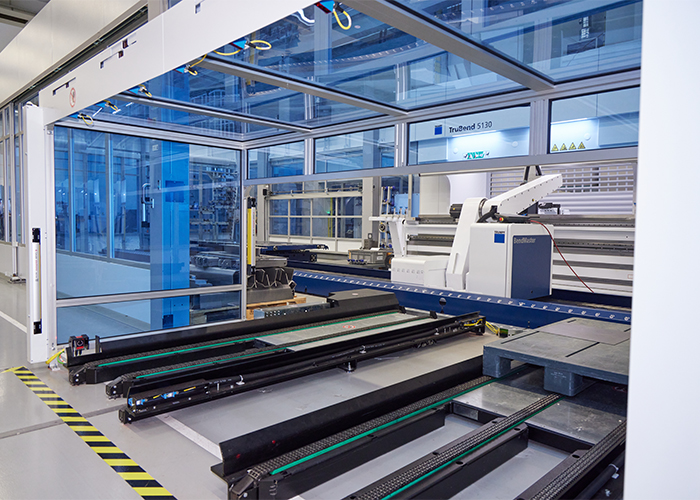
"The installed Leuze sensors are, as it were, the backbone of this intelligent intralogistics solution," says Jörg Beintner, key account manager for machine tools at Leuze. Here each sensor displays its strength. The HT5.1/4X for detecting the presence of carriages and pallets is an LED diffuse sensor with background suppression – it detects objects reliably while simultaneously suppressing the background. The operating range can be set intuitively using a spindle. For TRUMPF, the HT5.1/4X was the ideal choice. Leuze also offers other models of the sensor, tailored to the requirements and application of the customer. The diffuse sensor with background suppression is, for example, also available with a laser or as a sensor version for detecting particularly small objects. There are also sensors with extra large or small light spots or optimized for high-gloss and polished surfaces.
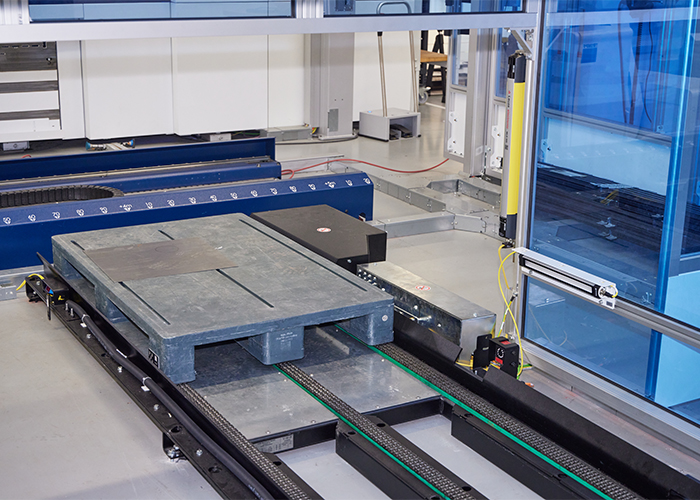
"As the second key component for TRUMPF's intralogistics solution, we opted for our DCR 202iC stationary 2D-code reader," explains Beintner. The Leuze sensor captures 1D and 2D-codes extremely reliably. At the Customer Center, TRUMPF attached the 2D-codes on two sides of each pallet – at diagonally opposed positions. As a result, it doesn't matter which side of the pallet is pushed into the docking station first. In this way, the code can always be captured by just one sensor. The DCR 202iC camera-based code reader is ideal here: It reads codes which, depending on the type, are printed or directly marked, even omnidirectional. The Sensor People from Leuze offer various versions with respect to size, protection classes IP 67 or 69K, speed and interfaces. By the way, the Leuze sensors used for detection are not the only Leuze products used by TRUMPF at Ditzingen: Safety light curtains are installed at the material locks to the sheet metal processing machines. They reliably prevent persons entering the hazardous area. Here too, Leuze provided extensive support during design and implementation. And further joint projects are already in the pipeline.
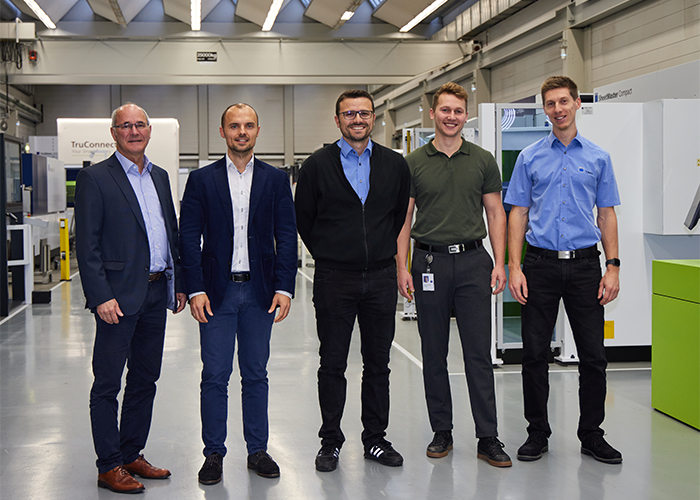
TRUMPF is completely satisfied with the high-performance and reliable Leuze sensor solutions. The sensors detect roller carriages and pallets and identify orders and materials fully automatically by means of 2D-codes. The case example from the Customer Center in Ditzingen shows that anyone wishing to elevate their production to a new, intelligent level can do so easily and conveniently with smart material flow. This applies both to small, handwork-based manufacturing operations and to smart factories. And it has tangible benefits: TRUMPF expects that its smart intralogistics solution will result in a time-saving of up to 25 percent with respect to production throughput times. Leuze sensor technology contributes to the reliable, safe and efficient implementation of a fully networked material flow.
Leuze
Mit Neugier und Entschlossenheit schaffen die Sensor People von Leuze seit 60 Jahren Innovationen und technologische Meilensteine in der industriellen Automation. Ihr Antrieb ist der Erfolg ihrer Kunden. Gestern. Heute. Morgen. Zum Hightech-Portfolio des Technologieführers zählen eine Vielzahl unterschiedlicher Sensoren für die Automatisierungstechnik. Zum Beispiel schaltende und messende Sensoren, Identifikationssysteme, Lösungen für die Datenübertragung und Bildverarbeitung. Einen weiteren Schwerpunkt setzt Leuze als Safety-Experte auf Komponenten, Services und Lösungen für die Arbeitssicherheit. Leuze konzentriert sich auf ihre Fokusindustrien, in denen die Sensor People über tiefgreifendes, spezifisches Applikations-Knowhow und langjährige Erfahrung verfügen. Dazu zählen die Bereiche Intralogistik und Verpackungsindustrie, Werkzeugmaschinen, die Automobilindustrie sowie die Labor Automation. Gegründet wurde Leuze 1963 an ihrem Stammsitz in Owen/Teck, Süddeutschland. Heute sorgen weltweit rund 1500 Sensor People mit Entschlossenheit und Leidenschaft für Fortschritt und Wandel. Und dafür, ihre Kunden in einer sich ständig wandelnden Industrie dauerhaft erfolgreich zu machen. Sei es in den technologischen Kompetenzzentren oder in einer der 21 Vertriebsgesellschaften, unterstützt von über 40 internationalen Distributoren.