Sensor solutions for labeling
Labels identify foods and pharmaceuticals and give products an attractive brand appearance. The variety of labels is growing constantly: New, sustainable materials are used and many manufacturers make their products stand out by using eye-catching prints, metalized labels or labels with transparent areas.
With our range of innovative sensors consisting of fork sensors, diffuse reflection sensors, retro-reflective photoelectric sensors, cut mark sensors, code readers or Vision sensors, we are able to provide solutions for all applications along the process chain of a labeling machine. The world's first optical label fork was a Leuze invention. Through the introduction of the first ultrasonic label fork we again laid the foundation for the further developments in the market. With the GSX combined fork sensor, unique worldwide, we go a step further and combine both detection principles – light and ultrasonics – in one compact housing. This fork sensor is the flexible solution for all labeling machines that process many different label types.
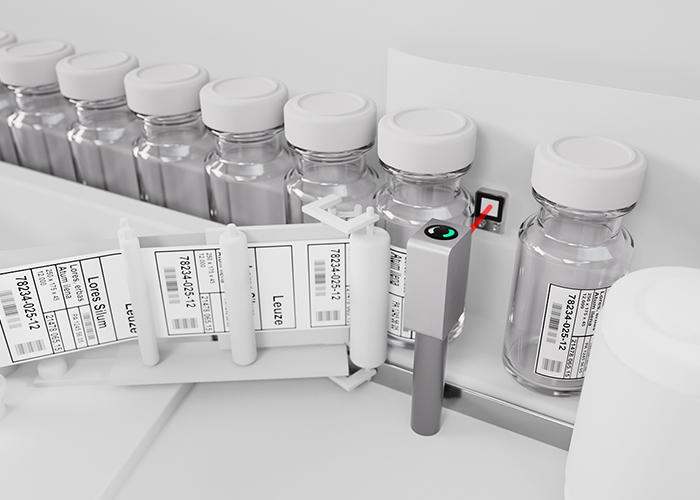
Requirement:
For precise labeling, the objects must be detected with as much precision as possible in order to activate the dispensing process. In doing so, a sensor should reliably detect all types and shapes of objects, including transparent ones. A change of products should have no effect on the labeling process.
Solution:
The PRK53C.T retro-reflective photoelectric sensor is developed for the detection of transparent objects. The sensor in a stainless steel housing for hygiene-sensitive production processes has a short response time and an integrated IO-Link interface.
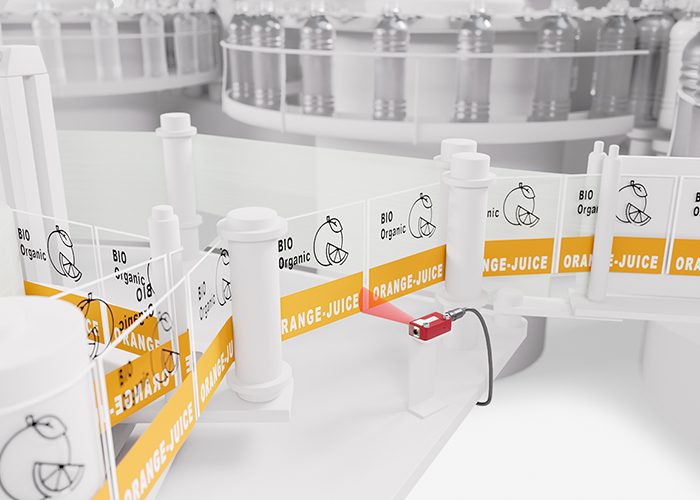
Requirement:
In labelers with a longer tape path, e.g. as a buffer between the roll and the dispenser, it is necessary to detect a possible tape tear.
Solution:
Diffuse sensors with particularly long light-spot geometry, such as the HT3C.XL, are suitable for monitoring the label tape. The sensor tolerates fluctuations and reliably detects only the actual tape tear. The compact design makes it easy to integrate the sensor.
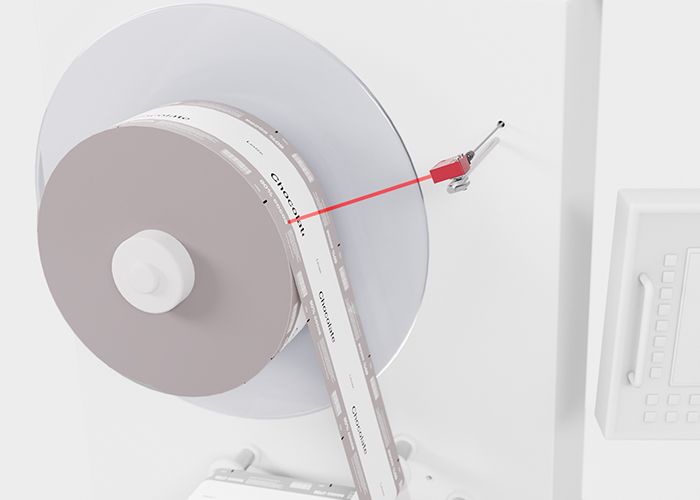
Requirement:
In high-performance labelers, the label roll is motor-driven. The diameter of the label roll should be permanently detected, e.g. in order to be able to adapt the speed to the decreasing roll diameter.
Solution:
The ODS 9 measuring sensor provides an analog distance signal for optimal adaptation of the drive. The distance sensors are available with different distance ranges, parameterization options as well as an integrated display. Thanks to the integrated IO-Link interface, the sensors can be used universally.
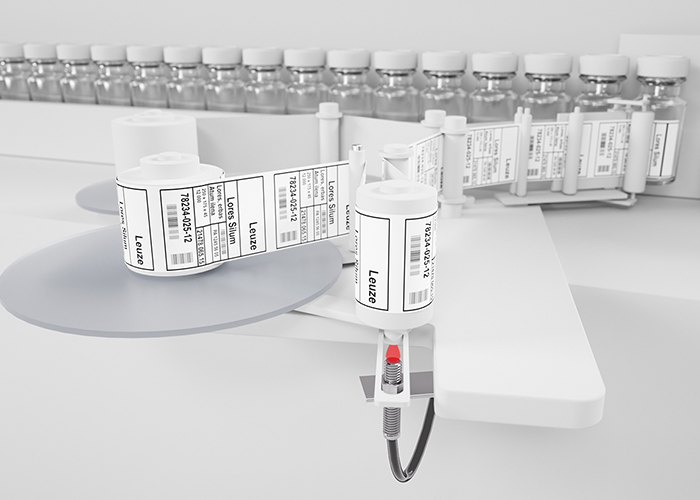
Requirement:
In order to regulate the carrier tape tension for self-adhesive labels evenly, deflection rollers pretensioned with springs are usually used. This so-called tension roll should ideally always be between the two end positions.
Solution:
The IS 200 inductive sensor detects the predominantly metallic roll mount and thus the two end positions of the tension roll. The IS 288, IS 212 or IS 218 inductive sensors offer the appropriate switching distances for embedded or non-embedded installation.
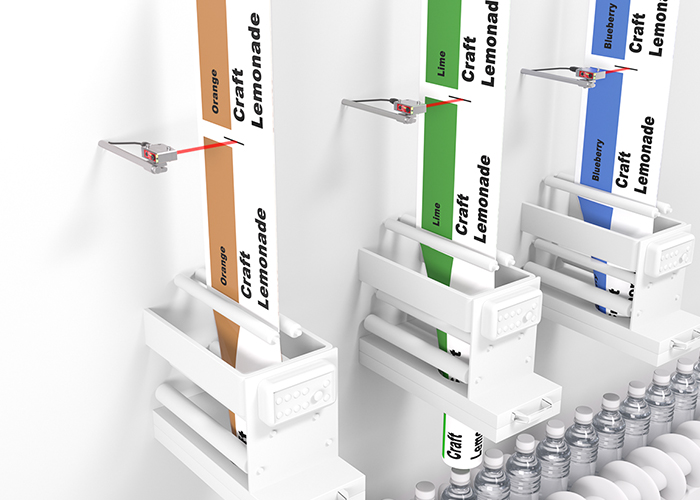
Requirement:
Sleeve labeling is frequently used in the beverage industry. Here, the label comes off the roll as a continuous film and is cut to the required length using print marks. This task requires special color mark sensors or contrast sensors that are optimized for high precision and speed.
Solution:
KRT 18B contrast sensors with signal display and multicolor transmitter LEDs provide high flexibility for the detection of cut marks. The integrated IO-Link interface simplifies commissioning as well as the adjustment of the contrast sensor when changing labels.
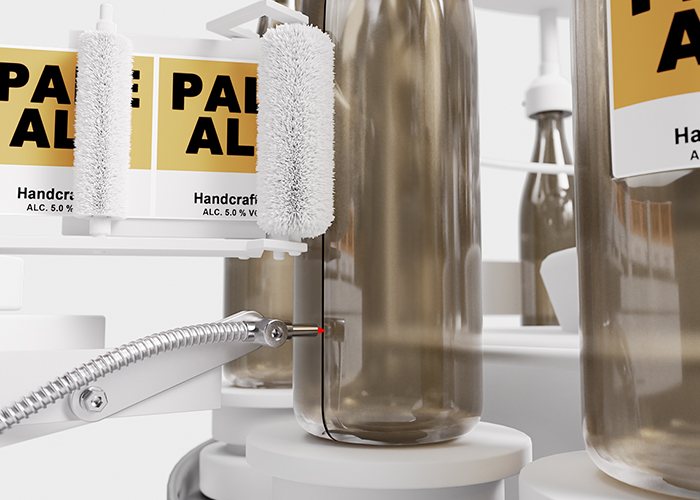
Requirement:
Labels should be applied at specified positions on the bottle. In addition, the alignment of the bottle must be detected and corrected on the basis of small features, such as embossing lugs or the joining seam. In compact machines, there is usually little installation space available for sensor systems.
Solution:
The GF glass fiber optics with different optical outlets and the LV 463 amplifiers are very suitable for checking the bottle alignment. Fiber optic sensors are particularly sophisticated and powerful at the same time. The sensors have an IO-Link interface and an optional analog output.
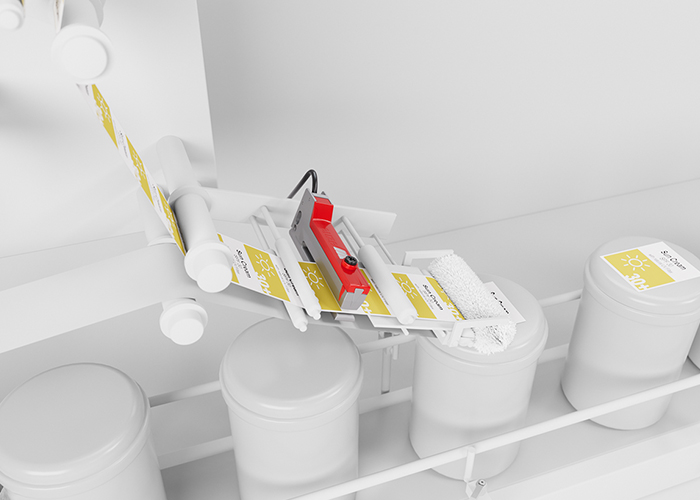
Requirement:
Non-transparent labels should be dispensed on packaging. To do this, the gap between two labels on the carrier tape must be precisely detected. The sensor should also reliably detect labels with complex shapes in order to avoid inaccurate dispensing or machine downtimes.
Solution:
The GS61 and GS63B optical fork sensors reliably detect the complete range of non-transparent labels. The sensor can be adjusted either with a potentiometer or via a teach function. The slimline design of the lower fork enables installation directly at the dispensing edge.
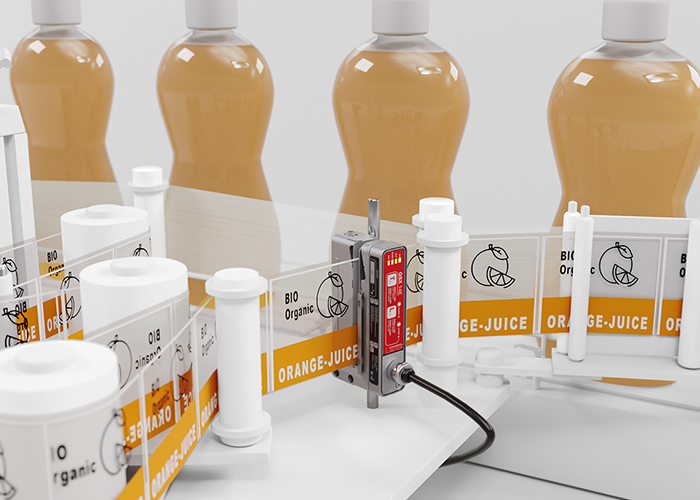
Requirement:
For a position-accurate dispensing process of labels onto products or objects, the labels must be detected on the carrier tape. Transparent, partially transparent or metallized labels in different shapes are also to be detected precisely. The sensor should be easy to set for all types of labels.
Solution:
The GSU12, GSU14E and IGSU14E ultrasonic fork sensors detect transparent and partially transparent labels. The GSX14E sensor combines an ultrasonic and an optical detection system in one housing and can even process labels made of inhomogeneous cavitated BOPP material. The IO-Link interface simplifies the setting.
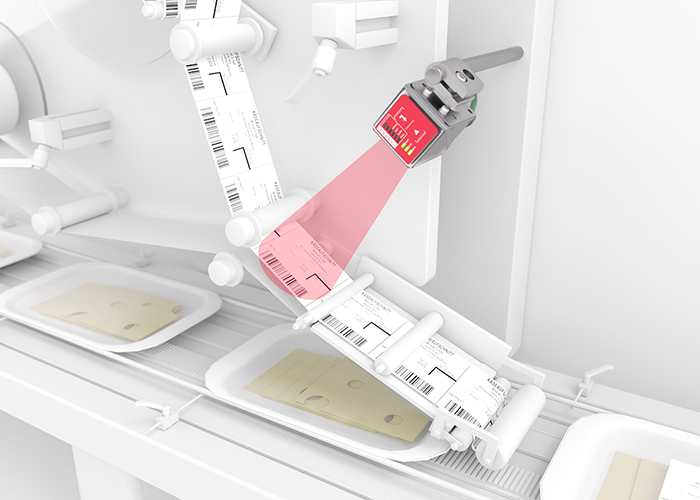
Requirement:
Primary packaged products are often provided with directly printed labels for high process flexibility. After printing, the readability of the codes on the labels as well as the plausibility should be checked.
Solution:
The DCR 200i universal code reader is suitable for identifying and checking bar codes or 2D-codes on labels. For use in the food industry, the sensor is also available in a stainless steel housing with plastic screen.
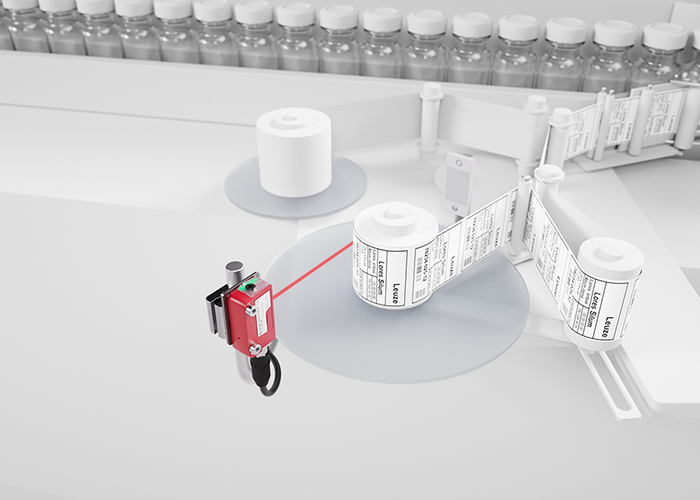
Requirement:
The roll diameter of self-adhesive labels is to be monitored with a sensor in order to warn the operator of the labeling system in good time before a roll end. The sensor should be able to be adjusted according to the roll diameter.
Solution:
Sensors of the 3C series, such as the HT 3C diffuse sensor or the PRK 3C retro-reflective photoelectric sensor - with or without laser light - with a precise switching point are very well suited for checking the roll diameter in compact labeling machines.
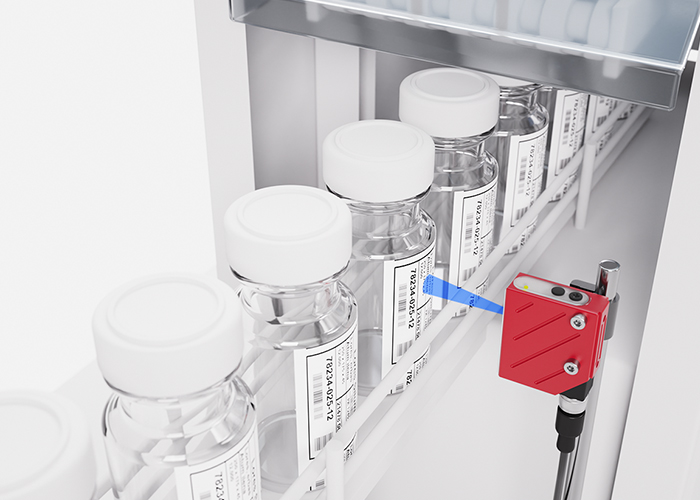
Requirement:
On containers such as bottles or vials, it is often necessary to check that the paper labels are on the objects after the dispensing process. The labels should be detected independently of the bottle or filling.
Solution:
The LRT 8 luminescence sensor detects paper labels very reliably on different objects, even at large distances. An alternative solution are energetic diffuse sensors with infrared light and special parameterization, e.g. the FT328I P1 or FT5I P1.
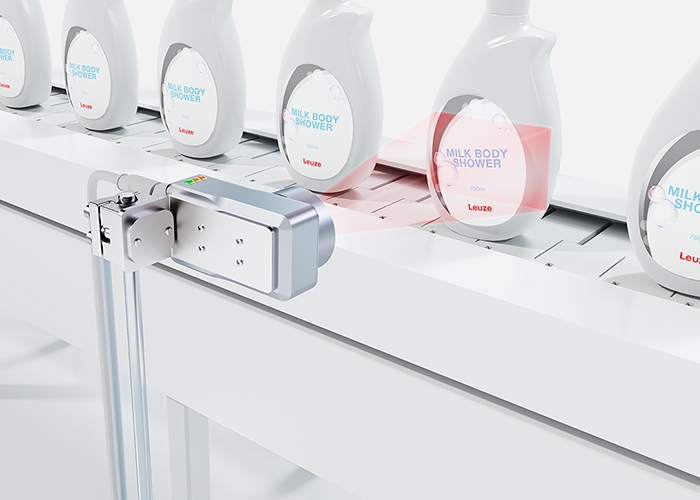
Requirement:
For high-value products or decorative labels, it should be ensured that the label is positioned correctly. Products with incorrectly aligned labels are to be detected and discharged.
Solution:
Simple Vision sensors of the IVS 1048i series can easily detect labels on products with their large field of vision and check whether they have been attached correctly. Parameterization is performed via the Leuze Vision Studio software. An integrated, switchable LED high-performance illumination ensures an optimal image.