Best quality, non-stop
Traditional beer specialties
Beer lovers in South West Germany are familiar with these traditional brands: Dinkelacker, Wulle Biere, Schwaben Bräu, Sanwald, Cluss or Haigerlocher. They are all regional beer specialties, each with its own character, and are brewed by Dinkelacker. The family brewery has been in existence since 1888. It was founded by Carl Dinkelacker in the Tübinger Straße in the heart of Stuttgart. And it is still headquartered there today. The company has always placed great importance on the best raw materials. They form the basis for the quality of the beers - whether Kellerbier in a swing top bottle, top-fermented wheat beer or non-alcoholic Pilsner. This quality standard is also reflected in the technical components used in production. For this reason, Dinkelacker has long been relying on Leuze application know-how, as well as sensor technology that meets the most stringent requirements for reliability, robustness and hygiene.
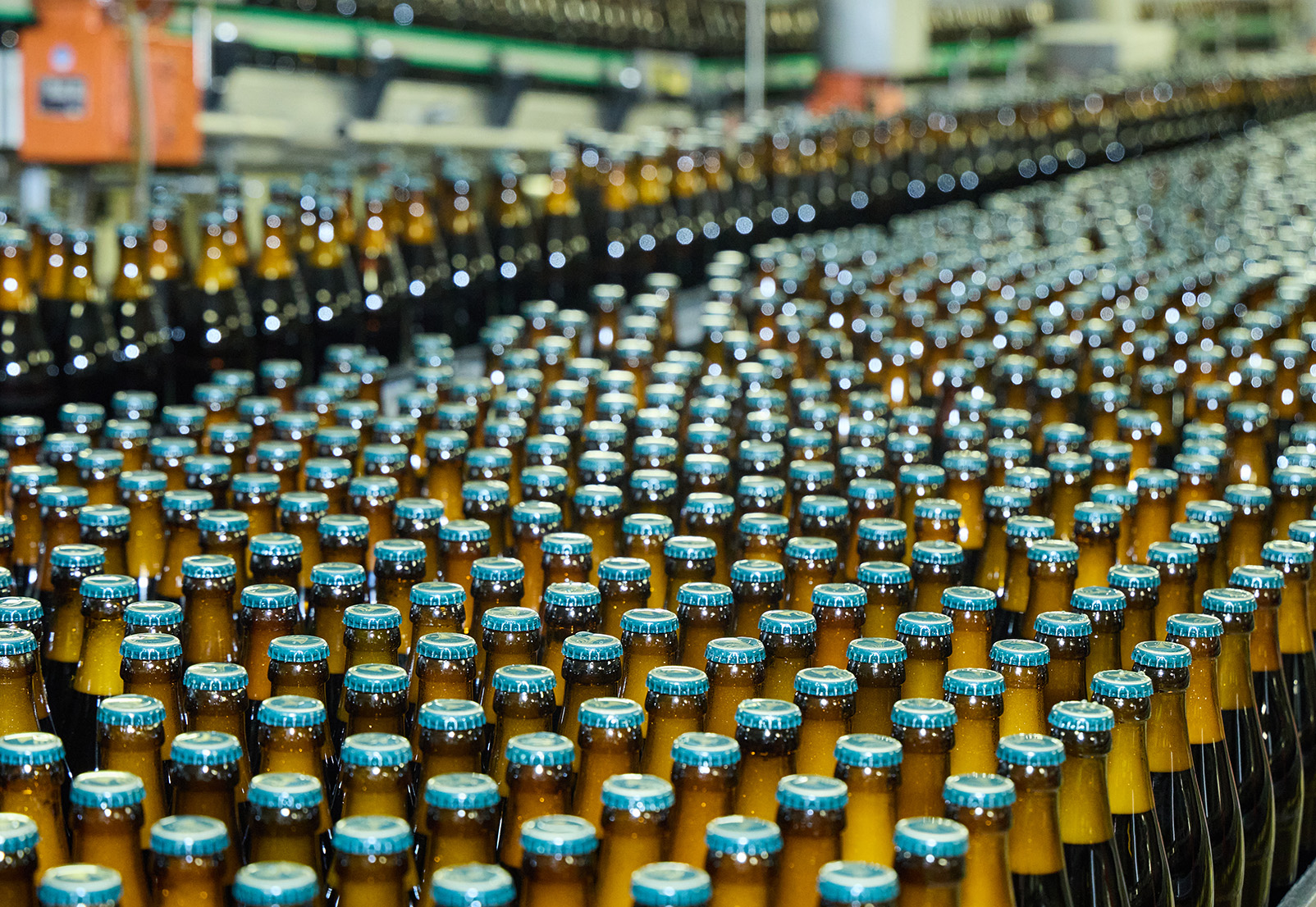
Strictly in accordance with the German purity law
Processes in a brewery follow a precisely defined sequence. Thousands of visitors on guided Dinkelacker brewery tours are impressed by this every year. If you take a look behind the scenes, you can experience the brewing process from start to finish: first, 40,000 liters of brewing water and 8.5 tons of malt from local farmland are mixed to create beer mash. For its malt, which consists of barley and wheat, Dinkelacker uses summer barley from the Strohgäu and the Swabian Alp. Dinkelacker is one of the few breweries in the world who still use a strain master. When it is ready, the mash is pumped there and filtered. Experts call this the "lautering" of the wort. The spent brewer grains remain, which are then used as supplementary animal feed. The mash turns into wort. The wort is then boiled and the hops is added. The brewery procures this from Tettnang near Lake Constance. This is followed by the brewery's own selected yeast, the last ingredient of the beer. The beer wort runs through a cooler into the beer storage cellar into one of 39 huge storage tanks. Each tank contains between 300,000 and 500,000 liters and is up to 25 m high. It is filled from the bottom until it is approx. three-quarters full, as the beer needs space to ferment in the tank. In order to deliver the finished product to the consumer, it is pumped to the filling installation.
Indispensable sensor technology
The sensors installed in the filling installation often look inconspicuous. But they are indispensable for efficient processes. Dinkelacker uses Leuze sensor technology at nearly every station. "To ensure fault-free operation, we depend on particularly robust and reliable sensors", explains Florian Fahr, Head of Technology at Dinkelacker. "The requirements for the technical components in the filling installation are very high. Here, there are strong vibrations and the sensors must be able to withstand frequent cleaning processes." Only selected sensor solutions can rise to the challenge. This is why Dinkelacker relies on the technology provided by the Sensor People from Leuze. Andreas Eberle, Local Industry Manager Packaging at Leuze, explains the advantages: "Primarily, retro-reflective photoelectric sensors of the Leuze PRK series were installed here." This series is particularly well suited for applications in the beverage industry. The metal housing of the optical sensors is resistant. As a result, the devices can also function optimally in harsh environments." Furthermore, the optically switching devices even detect highly transparent objects such as bottles, due to the reflection principle. High-gloss plastic crates with different imprints are also detected. At Dinkelacker, the technology provided by Leuze has proven its high reliability in practice, as Andreas Eberle knows: "Many of the sensors have already been working in the family-owned brewery with great precision for decades. Some were installed at the end of the 1990s, some at the start of the 2000s." Another advantage: by focusing on one sensor series, the brewery has to stock fewer different spare parts and in the rare event of a defect, they can react quickly and exchange sensors easily. And if there should be an urgent problem, they appreciate the close proximity to the headquarters of the Sensor People, who will promptly offer support.
Material flow without jamming or collisions
The Leuze sensors are used at different points in the filling installation and they have specific tasks. The process starts in the filling installation with the cleaning of bottles, beer crates and barrels. Cleanliness and hygiene play an important role. "The PRK optical sensors are installed on the individual conveyor sections and detect pallets, barrels, beer crates or even bottles", explains Frank Karle, Head of Electrical Workshop at Dinkelacker. "Thus the speed of the conveyor belts is automatically regulated to prevent jamming and collisions." In the barrel filling section, Dinkelacker has installed approx. 100 sensors on the conveyor belts. Up to 240 barrels an hour are cleaned and filled there. Two new robots which look like a full beer glass support the employees: they lift the empty or full barrels and place them on the conveyor belt or on pallets. Dinkelacker newly installed the robots while the hospitality sector was shut down during the Corona pandemic. Leuze safety technology also has a part to play at the robots: multiple light beam safety devices of type MLD secure the working range against unauthorized access from outside. Two PRK sensors which are switched crosswise in front of each of the robots reliably detect an incoming pallet. They then start the muting function, which briefly bridges the safety light barriers so that the pallet can pass through.
72,000 bottles cleaned hourly
Empty beer crates are cleaned by running them through a special cleaning machine. The bottles, which were removed previously, end up in a large bottle cleaning machine. There, they are cleaned with water heated to 80°C - the machine can handle up to 72,000 bottles in one hour. Here too, Leuze sensors are indispensable for safe operation: sensors of the PRK series detect immediately when a bottle is not in line on the bottle cleaning machine. Then they stop the machine. Again, access is monitored by safety light curtains. After cleaning, each bottle is checked for residues. If there are any residues in the bottle after the first pass, or remnants of labels are still adhering to the outside, the bottle is put through the bottle cleaning machine for a second time. If this is still the case afterwards, the bottle is rejected. This means: "If beer lovers want to do breweries a favor, they should not put anything in the bottles and open empty swing-top bottles before placing them in the crate", says Frank Karle.
Freshly filled
If the bottles are undamaged and completely clean, they are filled. Leuze sensors make it possible to regulate the conveyor belt speed. The system calculates the optimal speed based on the spacing between two bottles. The reusable bottle installation then fills the bottles with beer. It can manage up to 66,000 bottles per hour. This corresponds to 3,300 crates. The swing-top bottle installation works on a separate production line. It fills 30,000 bottles an hour. That means 1,500 crates per hour. As the filling process continues, checks are carried out to see if the level of the bottle contents is correct. After closing, PRK sensors detect if each reusable bottle has been correctly fitted with crown caps or if the swing-top bottle has been closed correctly. This is followed by labeling: the bottle is aligned and labels are applied to the neck, front and back. Here too, nothing is left to chance: every label is checked for its correct position on the bottle while it is still in the machine.
Every crate in view
Then the crater starts its work. The machine fills several crates at once with 20 beer bottles each. Leuze sensor technology is also employed at this station: "During full-crate monitoring, sensors detect in a fraction of a second if a crate is completely filled", explains Andreas Eberle. "If a bottle is missing or in a horizontal position, the crate is rejected and the error is corrected manually by an employee." When crates are filled with swing-top bottles, they are also aligned so their labels face outwards, for a pleasing look. Leuze sensors detect the labels on the bottles and support the machine with the correct positioning. This is followed by the last step: the crates are placed on pallets and delivered. Here too, sensors are used for presence detection of the pallets and optimize the material flow.
Continued tradition
Six widely known brands, beers for every taste and production which is virtually fully automated and fills many thousands of bottles and quite a number of barrels per hour: the Dinkelacker family-owned brewery from Stuttgart has successfully transitioned into the modern age. The Sensor People from Leuze make an important contribution to efficient production in all process steps, with their reliable and robust sensors. These are things Carl Dinkelacker could not even have dreamed about in 1888. But he would have found that one thing was unchanged even after 135 years: the passion for brewing beer from regional ingredients to the highest quality standards.
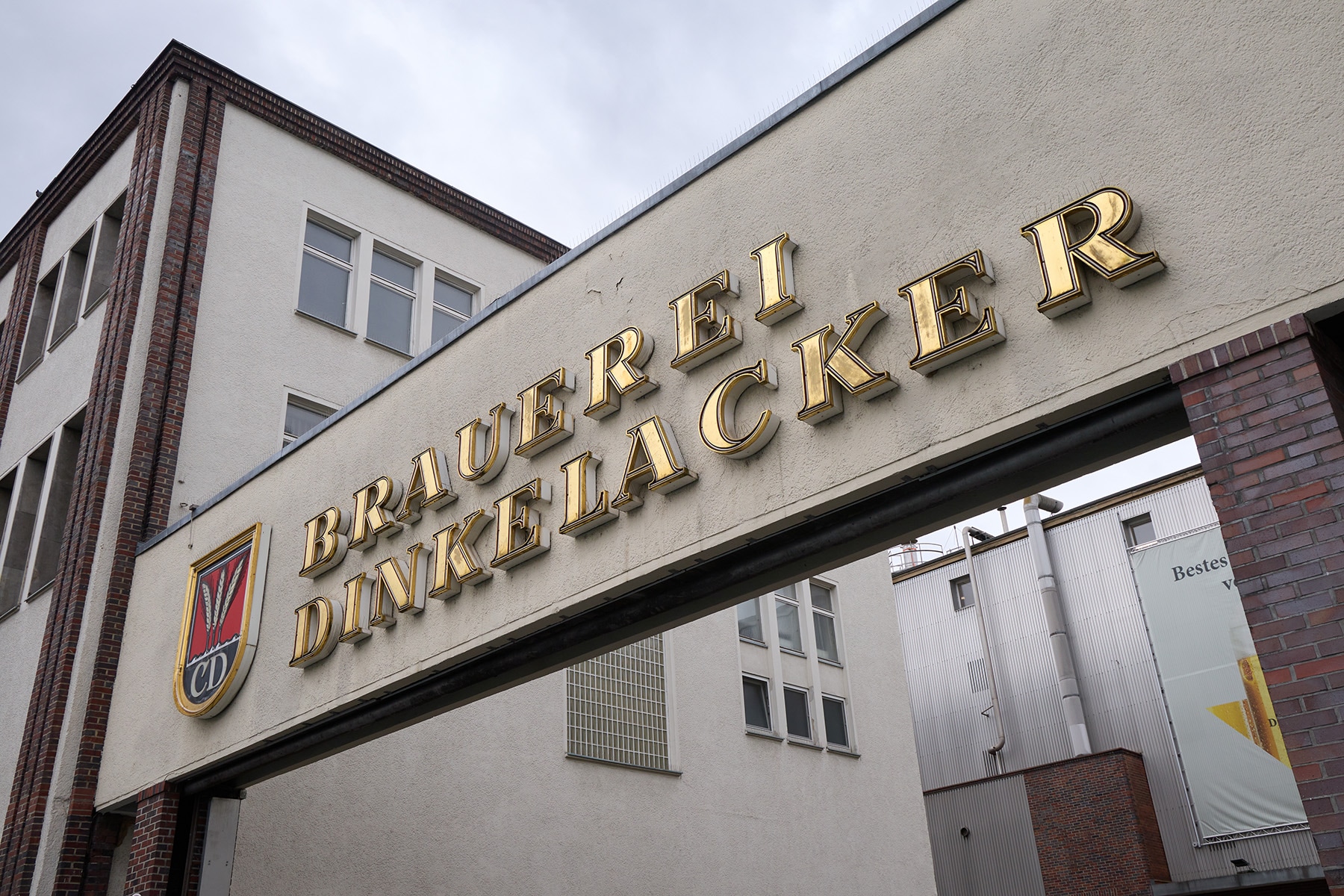
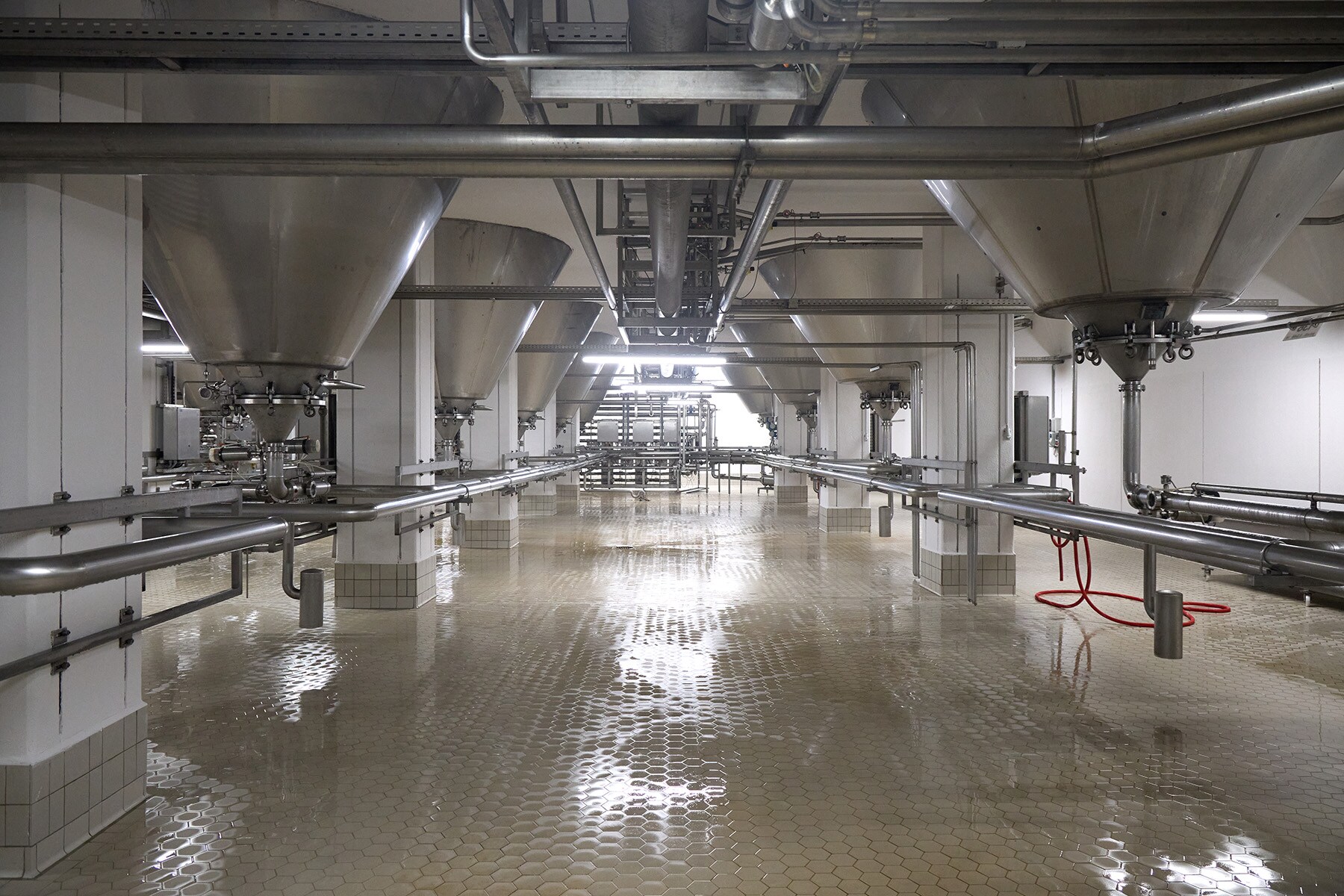
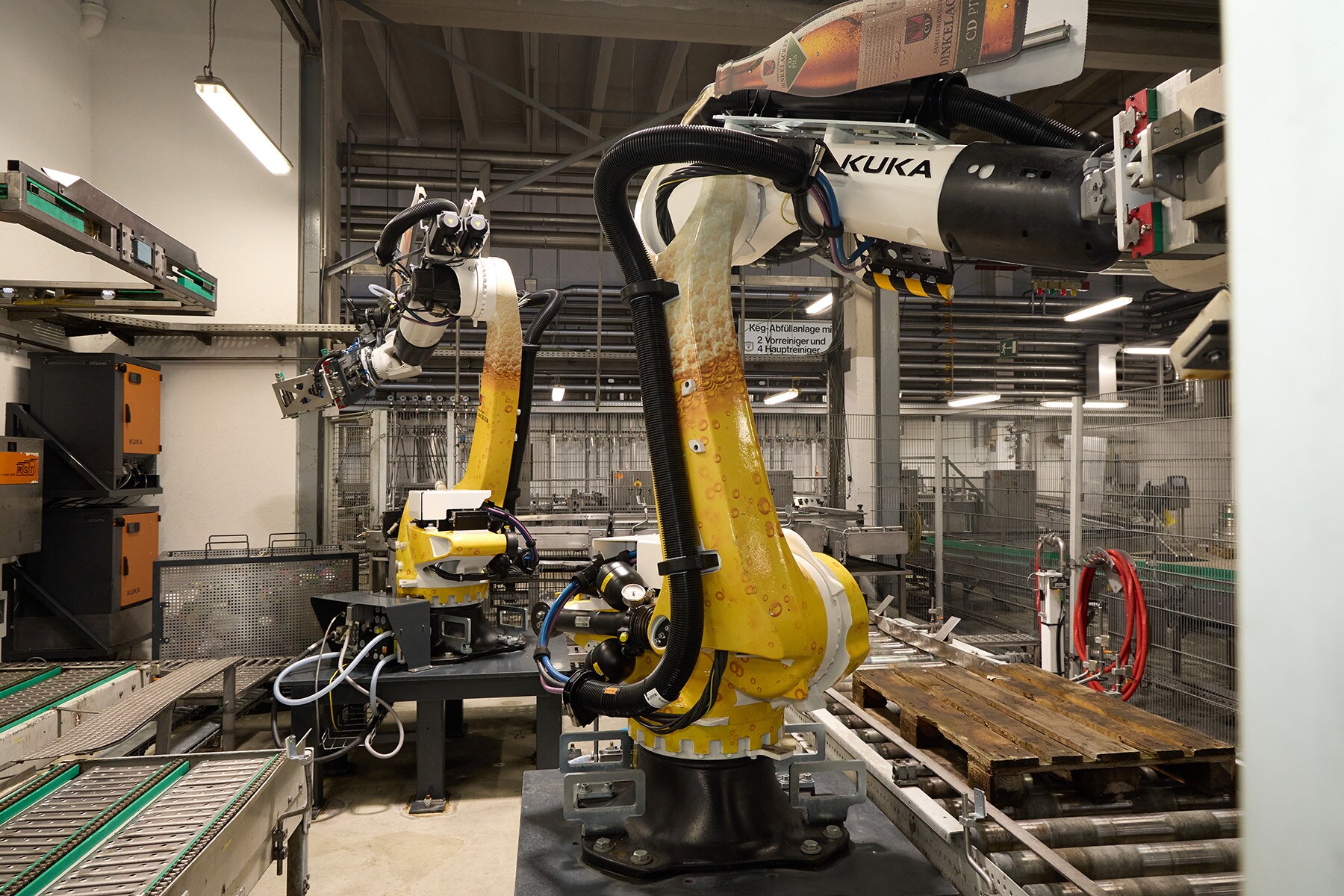
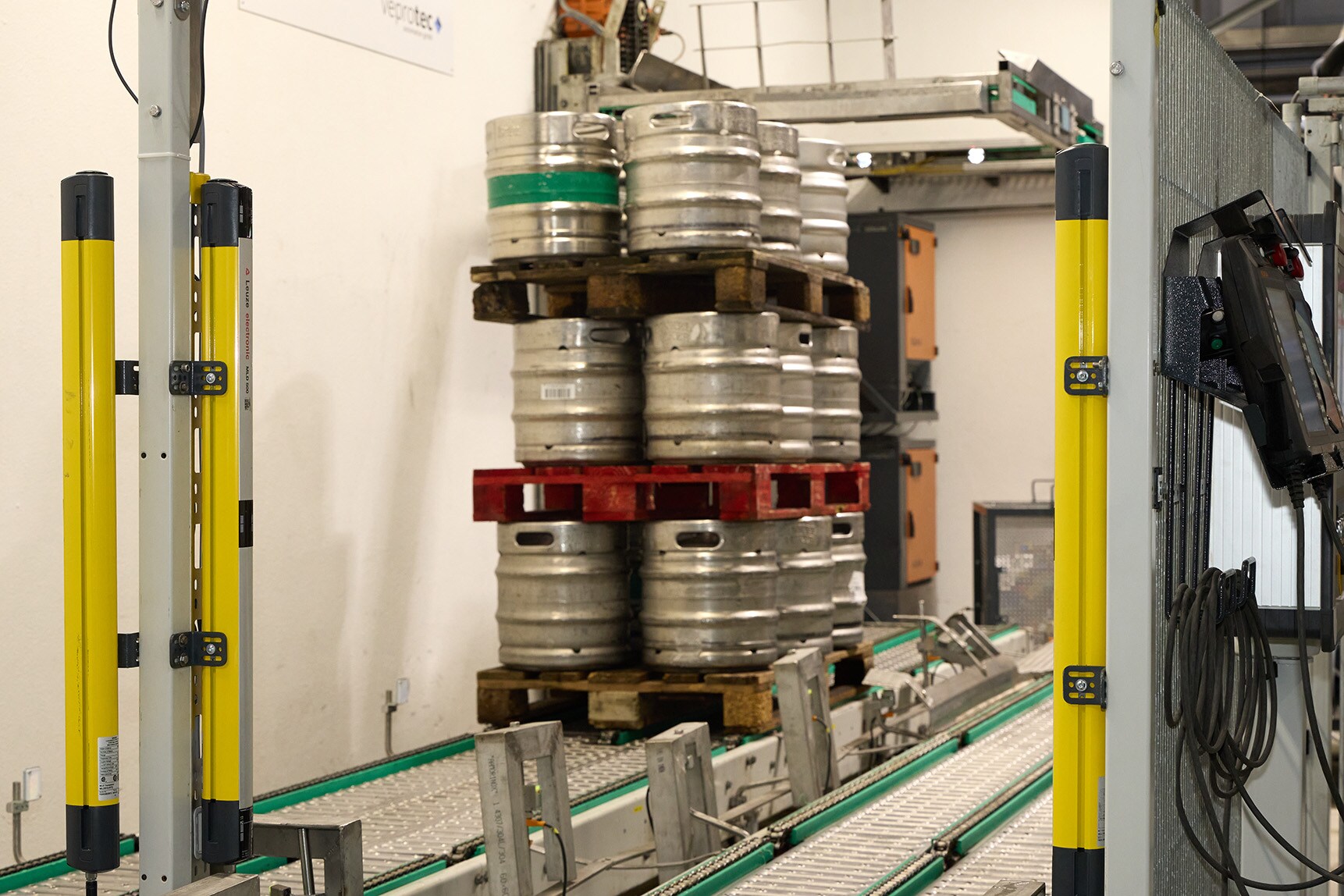
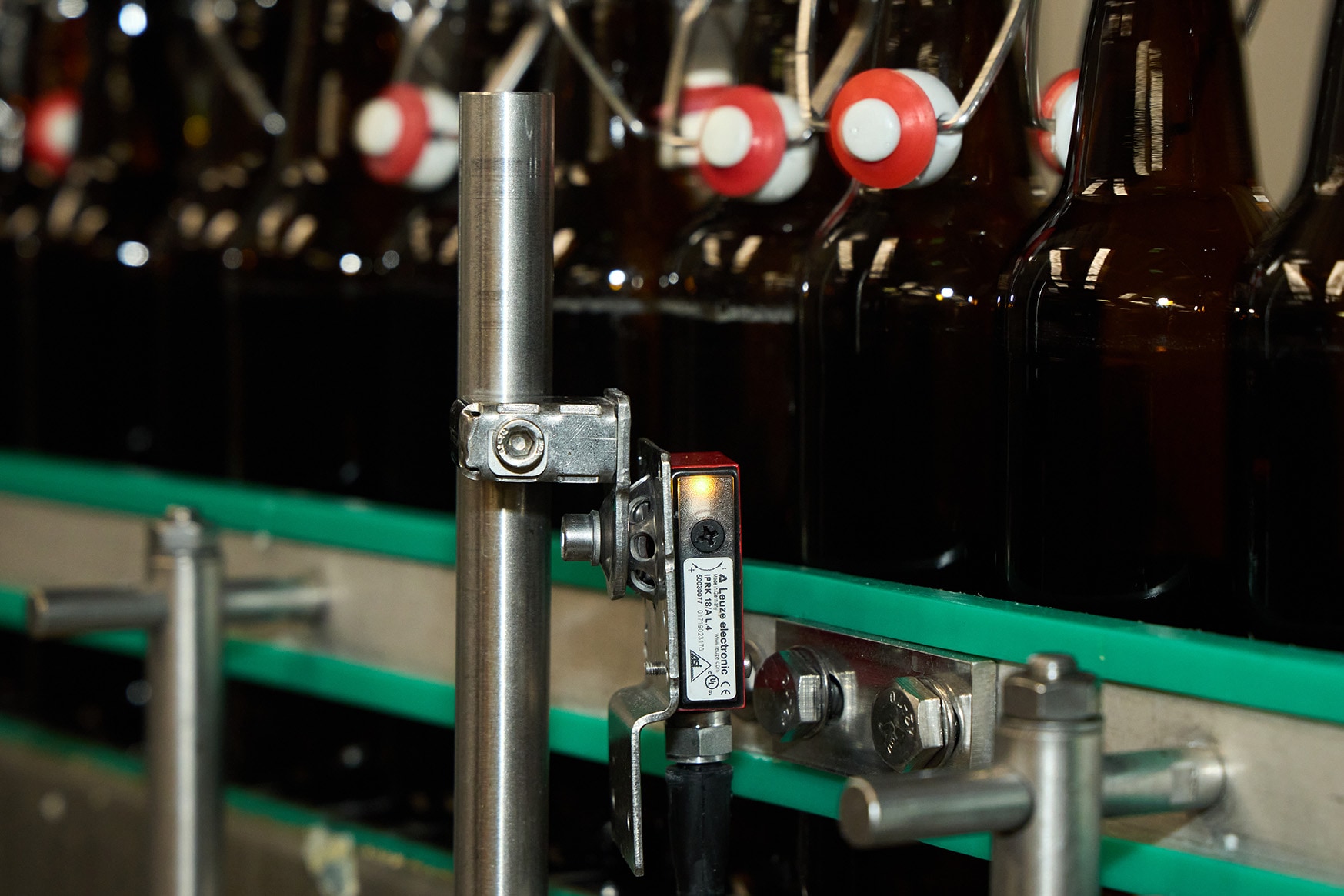
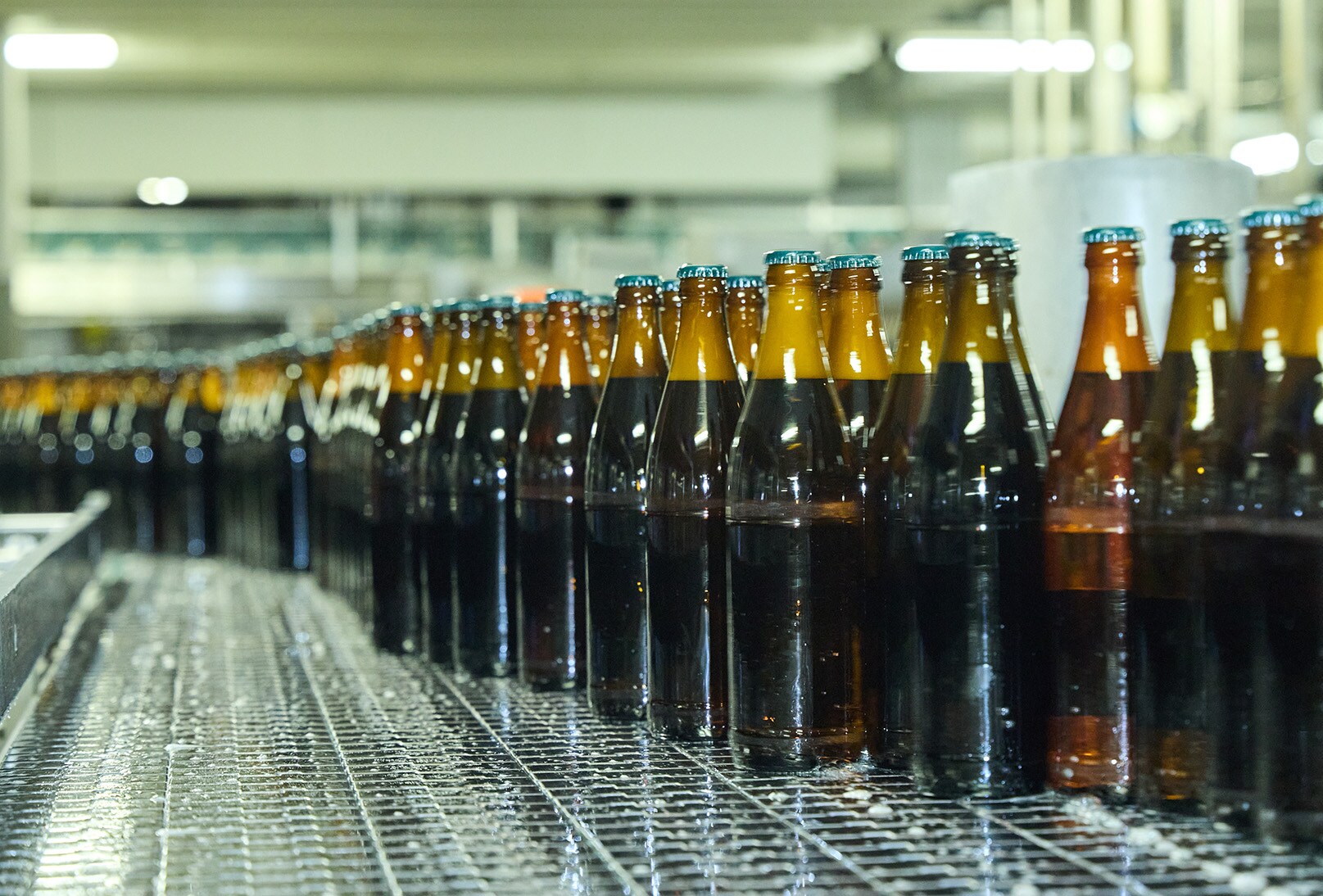
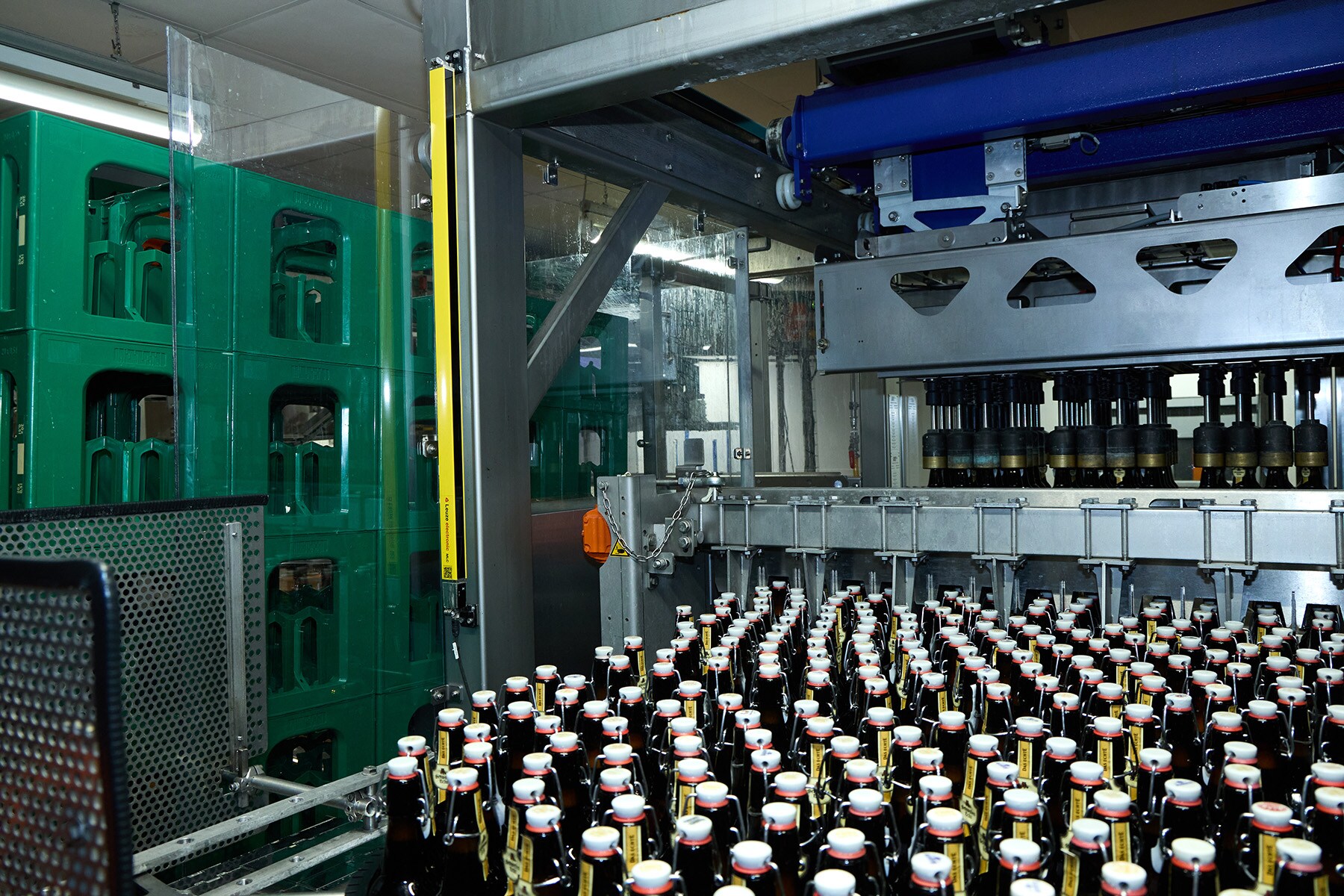
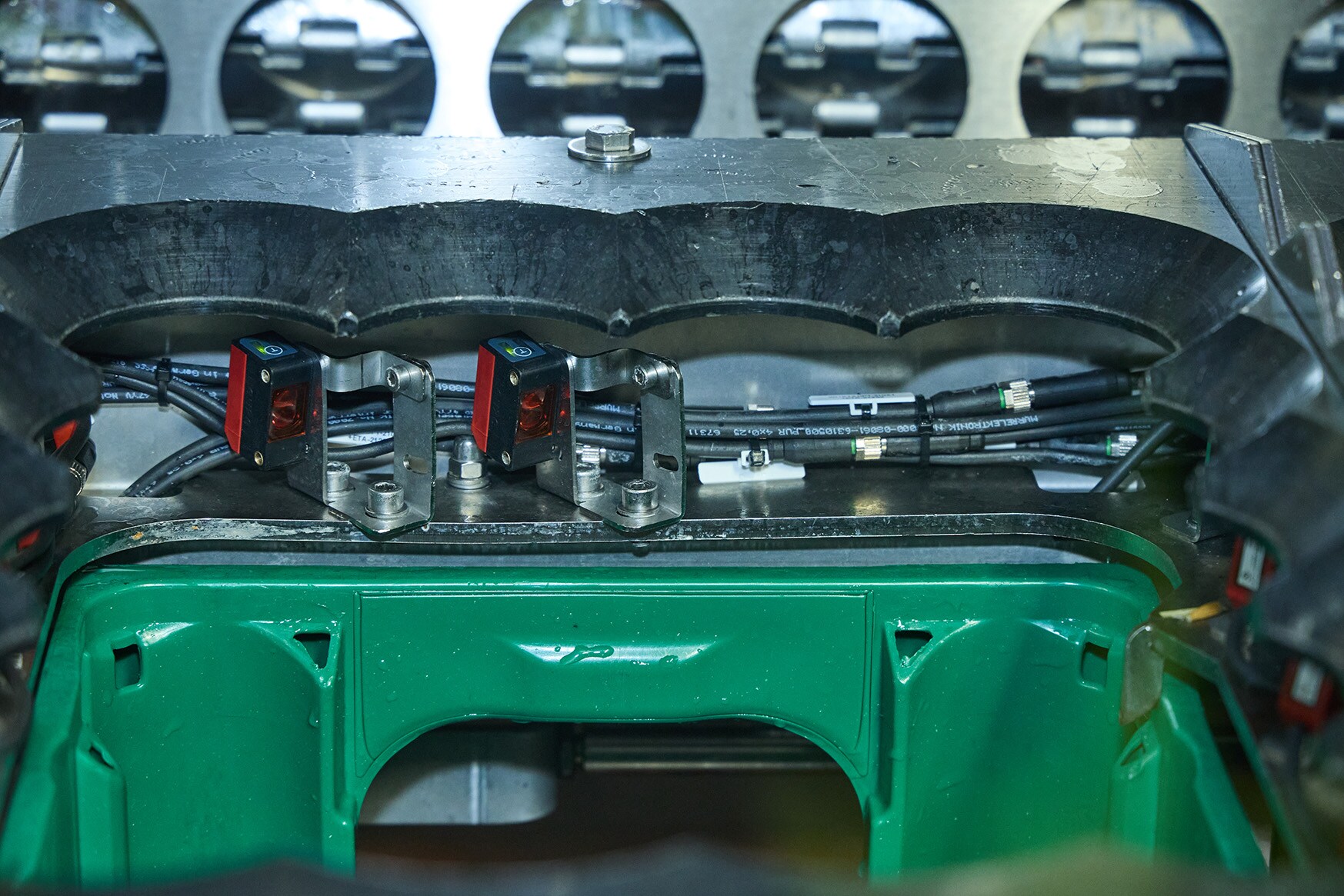
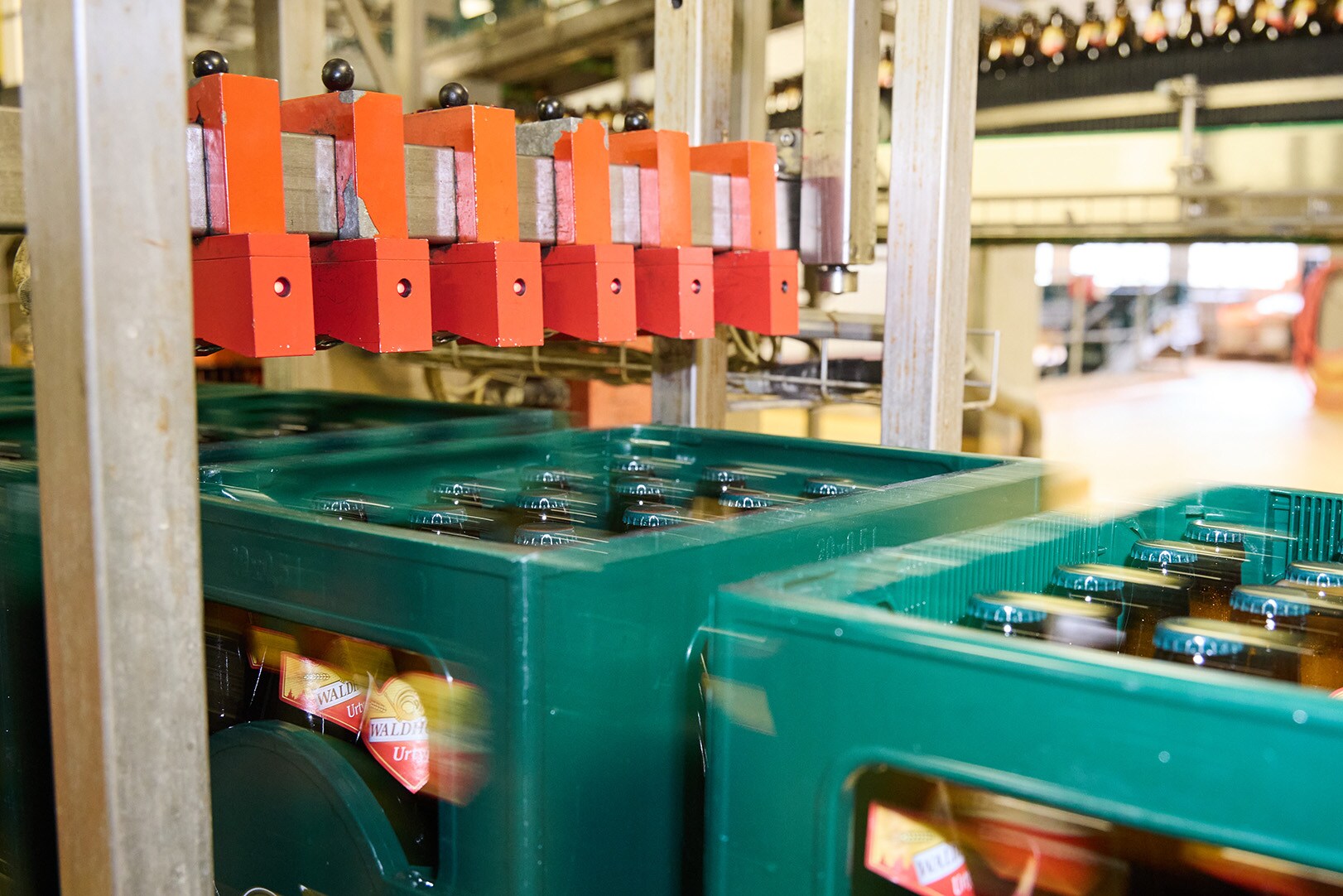
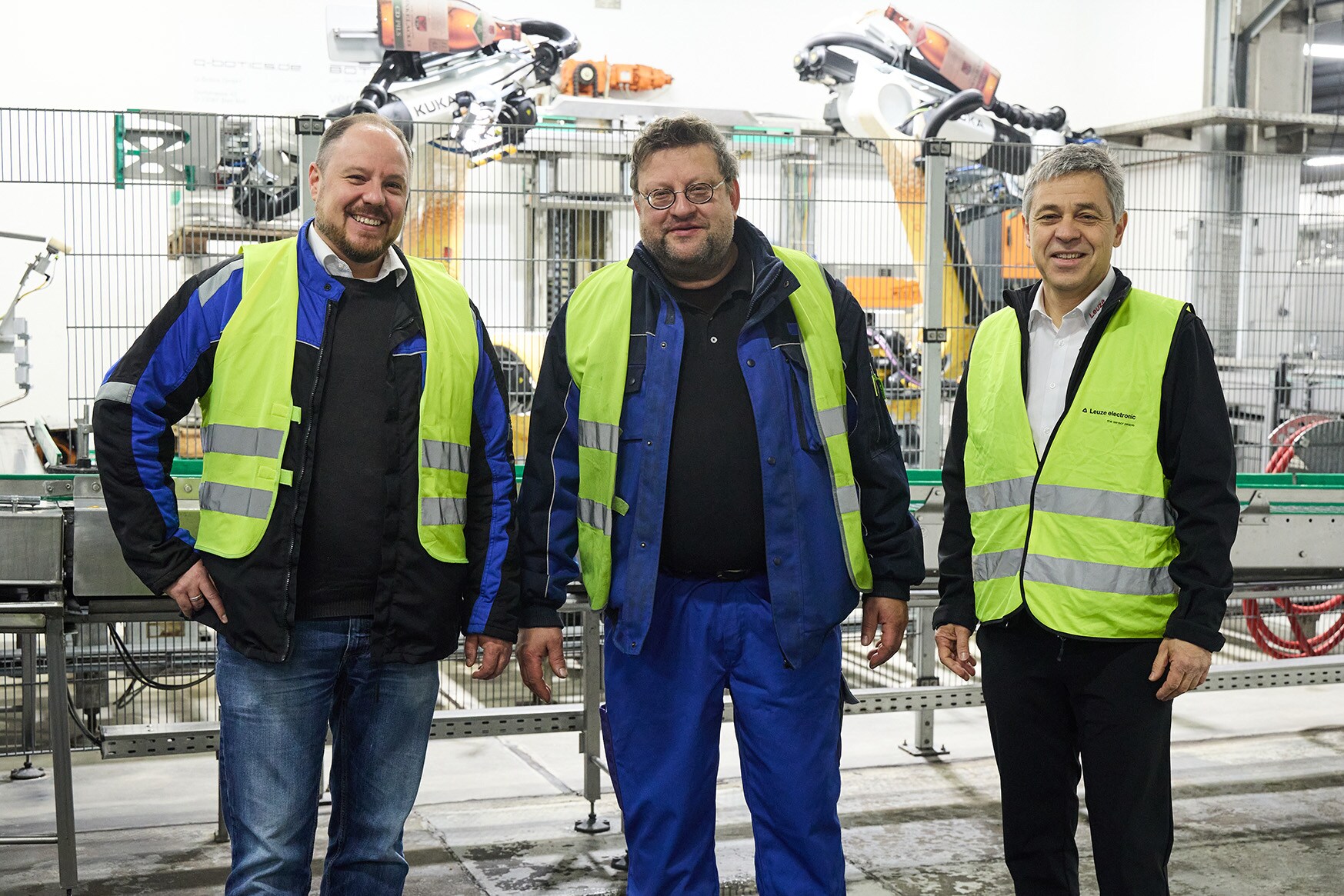