Sensor solutions for palletizing
In the final packaging step, cartons and packages are stacked on pallets and passed on to the subsequent storage or transport logistics. An efficient and reliable material flow as well as gapless machine safety determine the requirements in the end-of-line area.
The sensors used in these processes perform many different detection and identification tasks. For example, automated wrapping of pallets in stretch film to ensure safe transport: Here inductive sensors monitor the end positions of individual axes, diffuse sensors detect the upper edge of the pallets, polarized retro-reflective photoelectric sensors detect tears in the film, and diffuse sensors monitor the film supply. On conveyor lines, optical or mechanical access guarding ensures safe operation of the systems. Two function concepts for temporary and controlled bridging of the used electro-sensitive protective equipment each offer specific advantages: Multiple light beam safety devices such as the MLD 530 with predefined muting functions can be integrated quickly and easily into the system control. In the case of the MLC530-SPG safety light curtains with "Smart Process Gating", bridging, i.e. the muting function, is implemented in combination with the process sequence and a control signal from the machine control. The space required is reduced to a minimum and additional muting sensors are no longer necessary.
2 Height measurement of pallet stacks
4 Detection of objects on conveyor belt
5 Detection and positioning of objects
6 Detection of pallets from below
8 Access guarding with Smart Process Gating
11 Monitoring of end positions
12 Detection of winding height
14 Determination of residual quantities
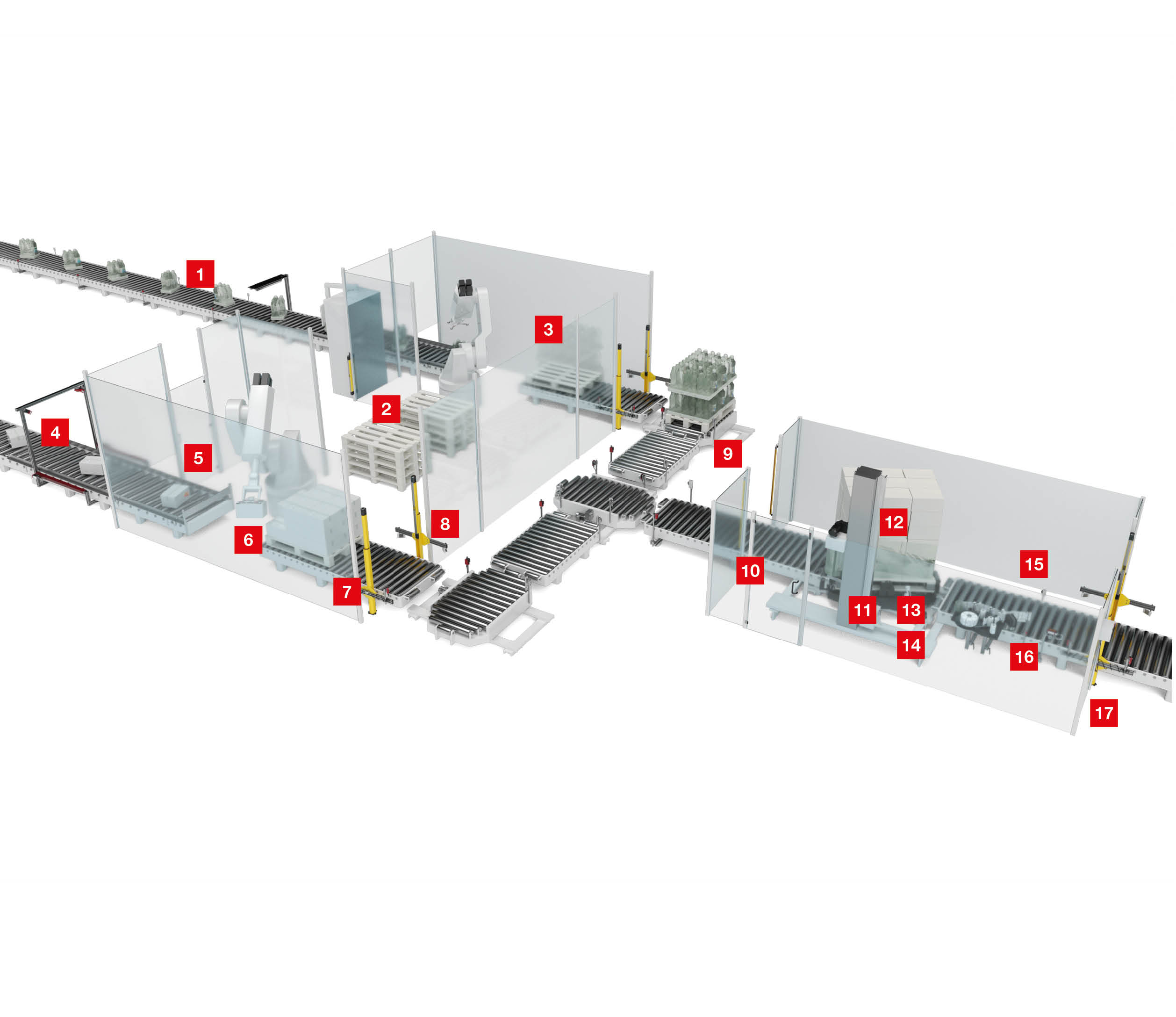
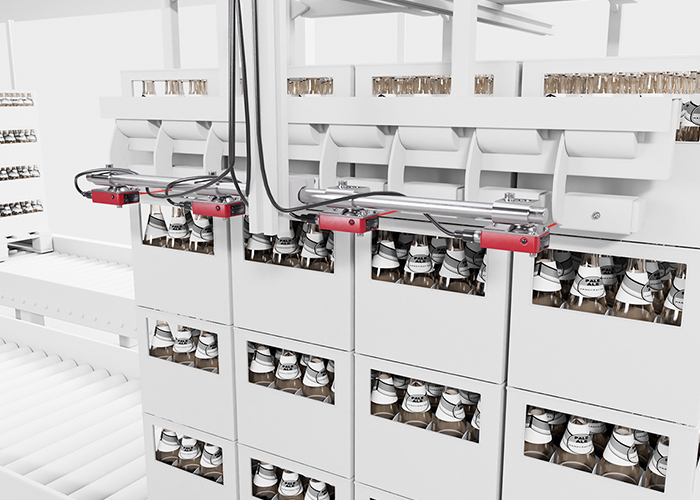
Requirement:
In the final packaging or palletizing of packages, the presence of the objects is to be checked. Objects with gaps must also be reliably detected.
Solution:
The PRK 46C retro-reflective photoelectric sensors have a long operating range and thus a very high function reserve. In other models, the sensitivity can be adjusted, and a Depol function increases the availability of the system. All sensors have a degree of protection IP 69K and ECOLAB certification.
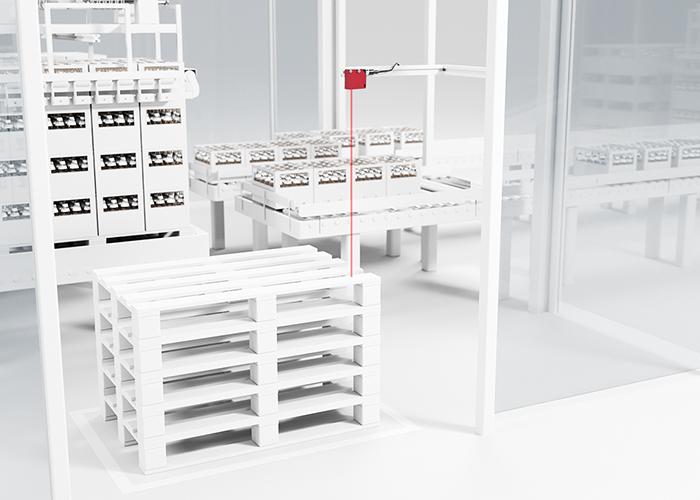
Requirement:
In an automated palletizing process, it must be ensured that sufficient empty pallets are available in a buffer. For a reliable process, the stack height of the pallets must be monitored for this purpose.
Solution:
Optical measuring sensors ensure reliable height measurement. The ODS 110 distance sensor can output the distance either via an analog value or the integrated IO-Link interface. Thanks to the small, clearly visible laser spot with laser class 1, the sensor is eye-safe and easy to position.
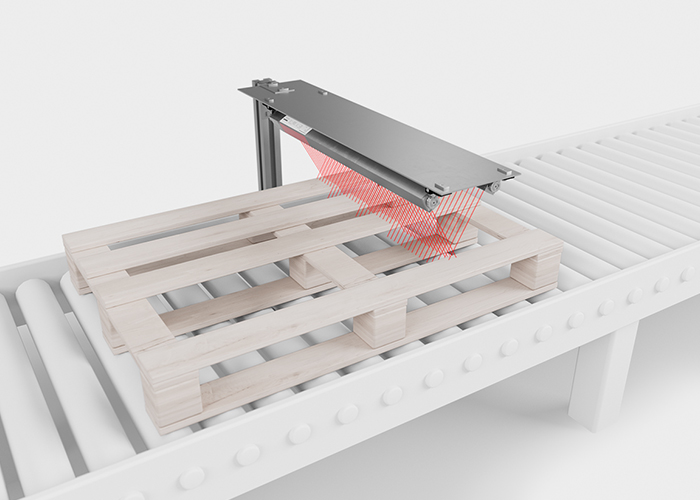
Requirement:
When standard pallets are used, the condition of each pallet is to be checked before it is used again. Among other things, it is necessary to check whether the running boards as well as the pallet blocks are present.
Solution:
With the aid of the single-beam evaluation of the CML 730i measuring light curtains in V-arrangement, the running boards can be detected and evaluated. The sensor array detects any gaps or missing boards and thus enables defective pallets to be removed early on.
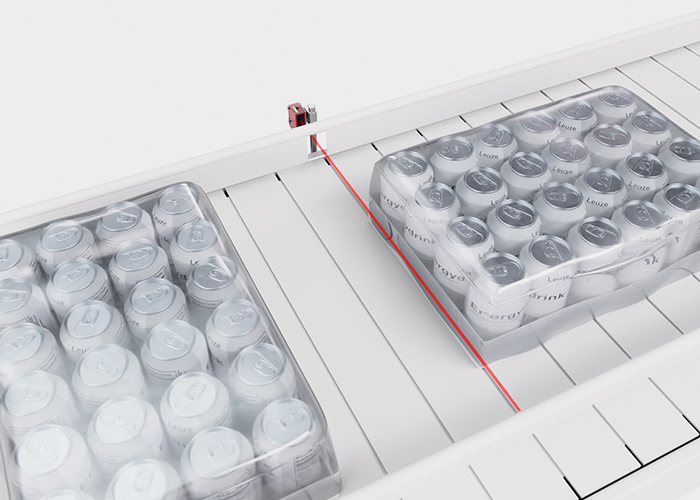
Requirement:
Packages or cartons that are shrink-wrapped with film are transported on a conveyor belt and are to be reliably detected.
Solution:
The PRK25C.D retro-reflective photoelectric sensor is optimized for the detection of shrink-wrapped objects and thus offers a high function reserve. If limited installation space is available, the PRK 5B.D sensors with smaller housing are used.
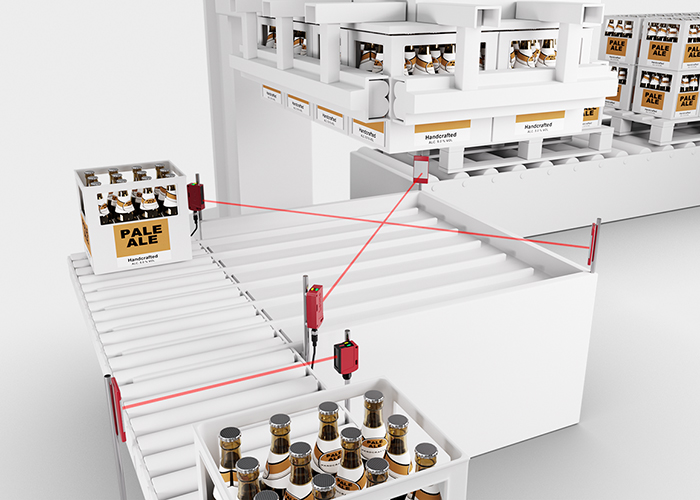
Requirement:
Along transport segments or at transfer points, objects are to be detected or the respective stop positions detected. For this purpose, the sensors used must have good alignment capability and high repeatability. Variations of the objects and possible contamination must also be tolerated.
Solution:
The detection and positioning of packages can be solved with different retro-reflective photoelectric sensors. Depending on the required function reserve and dimensions, the PRK 28, PRK 25C or PRK 46C in cubic form and the PRK 328 in cylindrical form are suitable for these tasks. All sensors have a degree of protection IP 69K and ECOLAB certification.
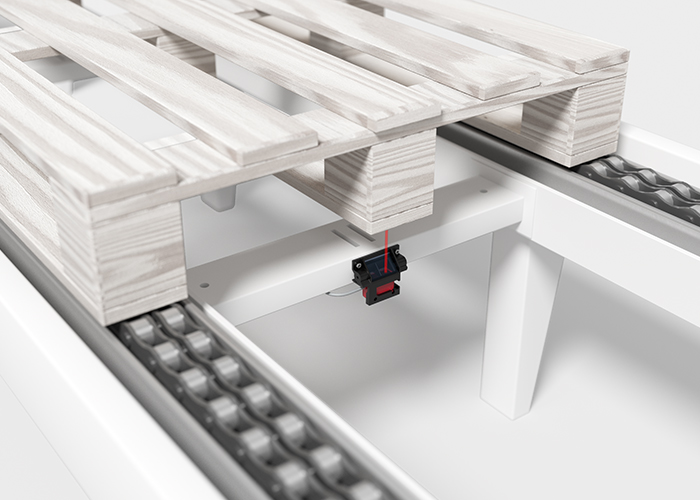
Requirement:
Different types of pallets are transported using a pallet conveyor system. To be able to set up the conveyor segments completely and ready to use, the pallets are to be detected from below. Any high-frequency LED hall lighting or dirt particles must not affect the sensor.
Solution:
The SET-HT25CI mounting system combines a special holder with a HT 25C diffuse sensor. The holder has an integrated front screen positioned at an angle so that any falling dirt particles are deflected automatically. The special parameterization of the sensors efficiently suppresses possible ambient light sources.
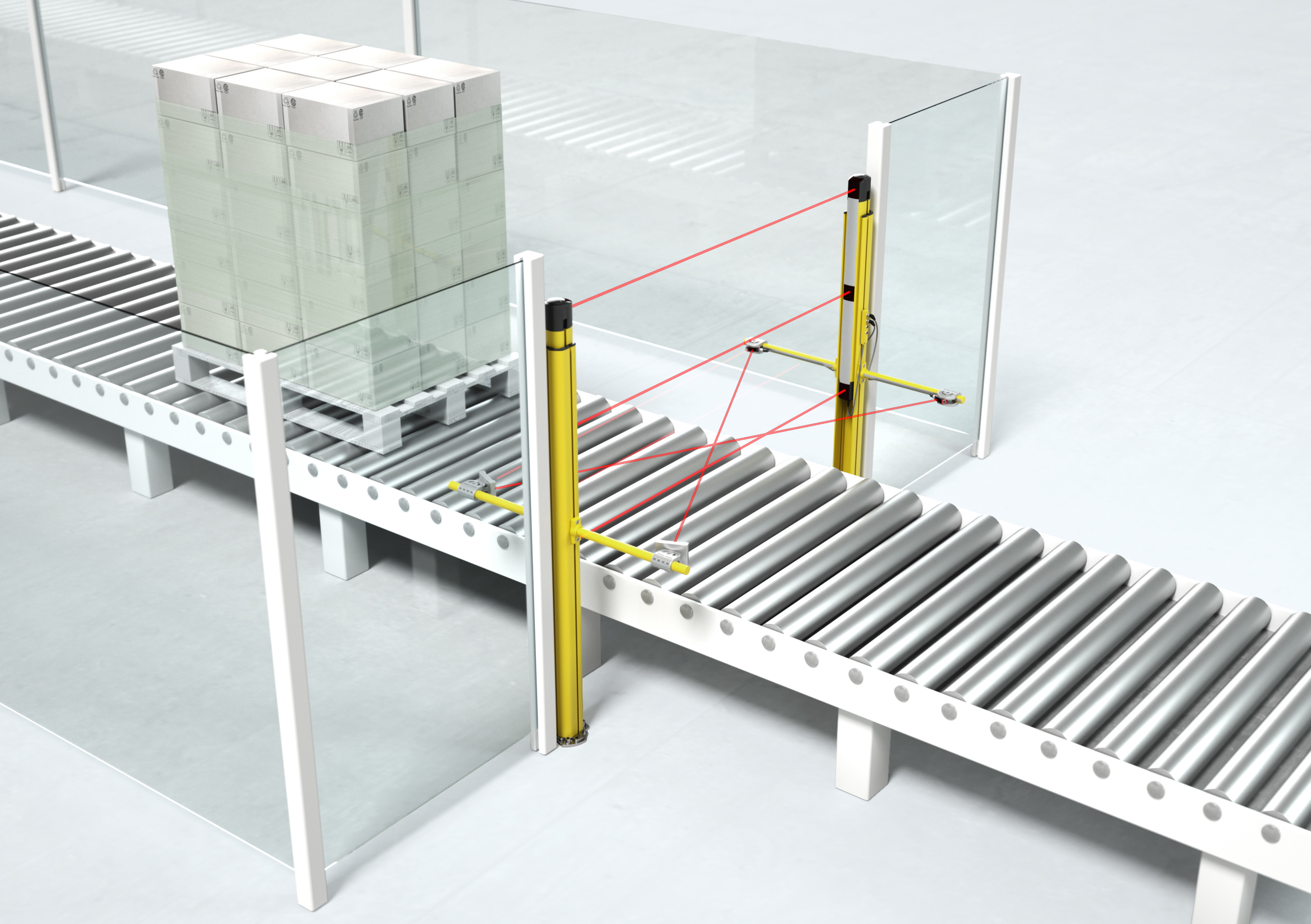
Requirement:
Access guarding on conveyor lines is to prevent persons from accessing a potential danger zone, while at the same time allowing the transported goods to pass through.
Solution:
The muting function bridges the safety sensor during the passage of the transported goods. This function is already integrated in the MLD 530 multiple light beam safety devices and in the MLC 530 safety light curtains.
The MLDSET protective sensor sets offer complete solutions for access guarding with muting function.
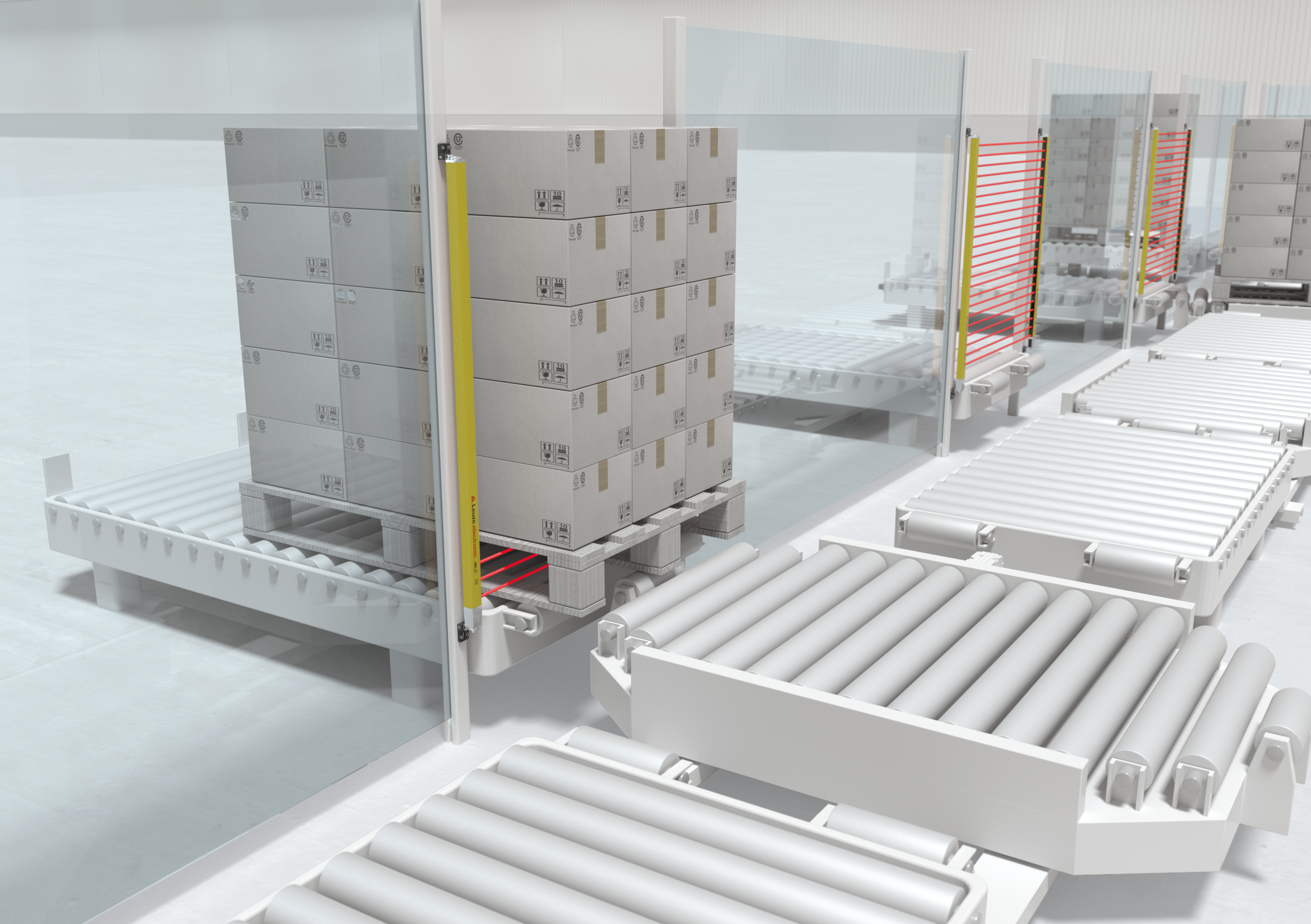
Requirement:
Access guarding on a conveyor line is to prevent persons from accessing a potential danger zone, while at the same time allowing the transported goods to pass through. Ideally, the safety system used for this requires as little space as possible.
Solution:
With Smart Process Gating, the safety sensor is bridged by means of a control signal from the PLC. The function is included in the MLC 530-SPG system. Additional muting sensors are not required and the systems can be designed to be particularly space-saving as well as tamperproof thanks to the SPG function.
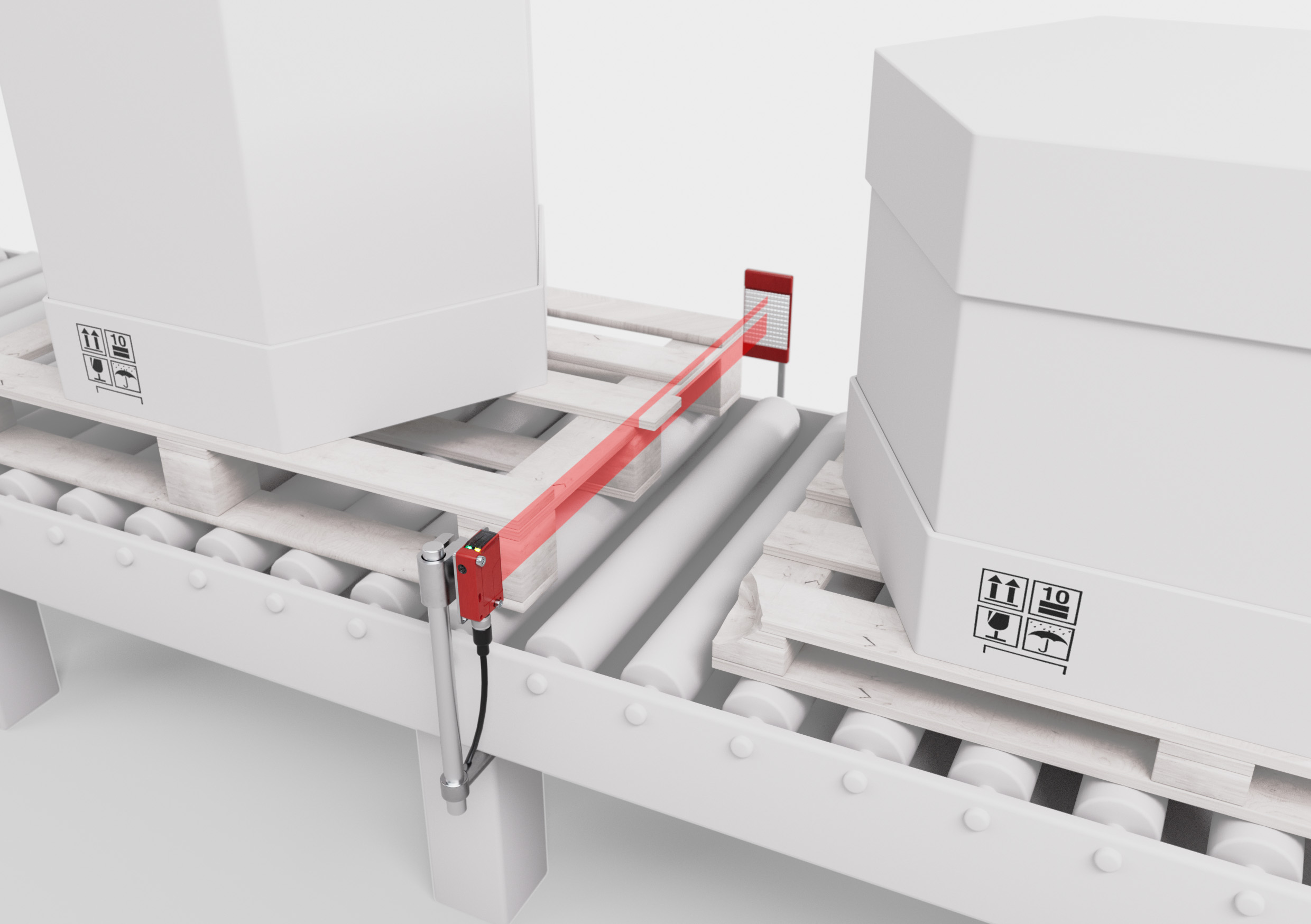
Requirement:
All types of pallets should be reliably detected over the entire length. Damaged pallets or pallets with irregular front edges should also be allowed.
Solution:
The RK 46C VarOS retro-reflective photoelectric sensors also reliably detect objects with irregular shapes and openings. For this purpose, the devices use a homogeneous, clearly visible 40 mm wide light-band and a standard TKS50x100 reflector. The sensors can be adjusted quickly and easily using a teach button.
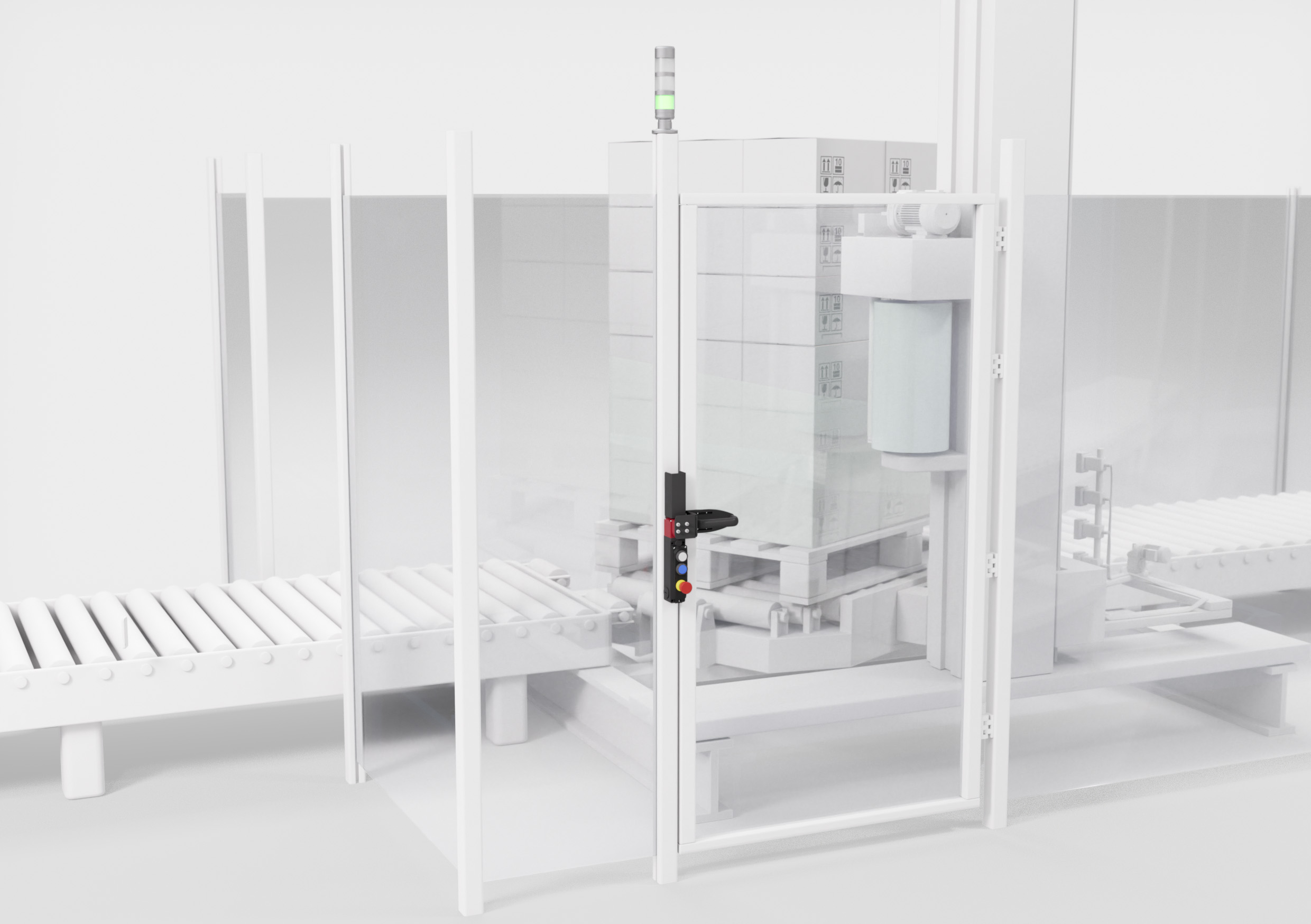
Requirement:
Areas with hazardous movements can be entered via safety doors to allow maintenance. If the movement does not stop immediately after the door is opened, the door is to be guarded by a safety switch with locking device.
Solution:
The robust L100, L250 and L300 safety switches with locking device keep safety doors securely locked until access is released by an electric signal. The series includes standard designs, devices with integrated operational controls as well as devices with RFID‑coded actuators.
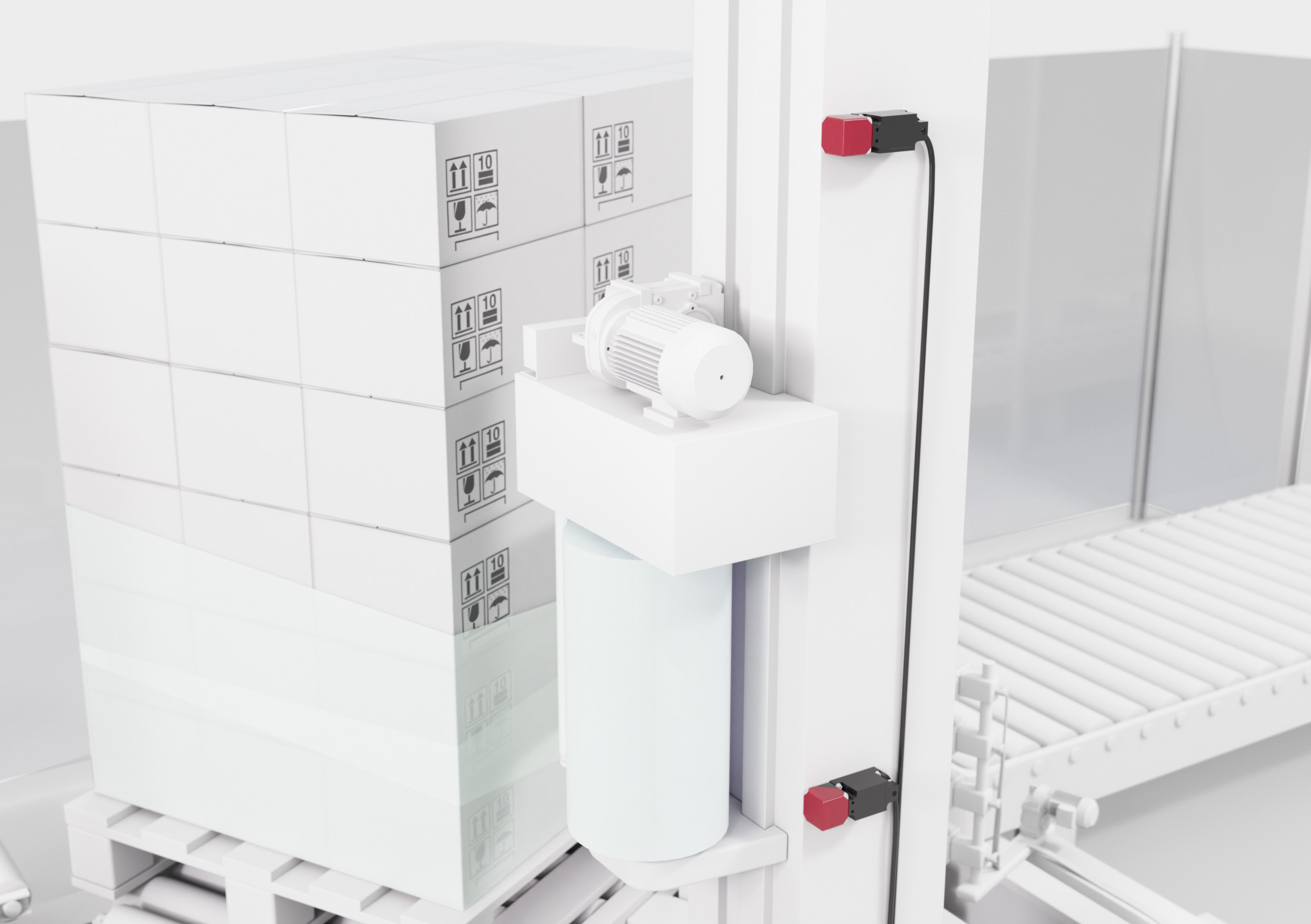
Requirement:
For transport safeguarding, pallet loads are often automatically wrapped in stretch film. In pallet wrapping machines, the respective final position of the film carriage must be monitored to prevent collisions.
Solution:
Inductive sensors detect the film carriage based on the metal parts installed on it. IS 244 cubic sensors with turnable active head and a terminal or M12 connection can be mounted flexibly and cover operating ranges up to 40 mm.
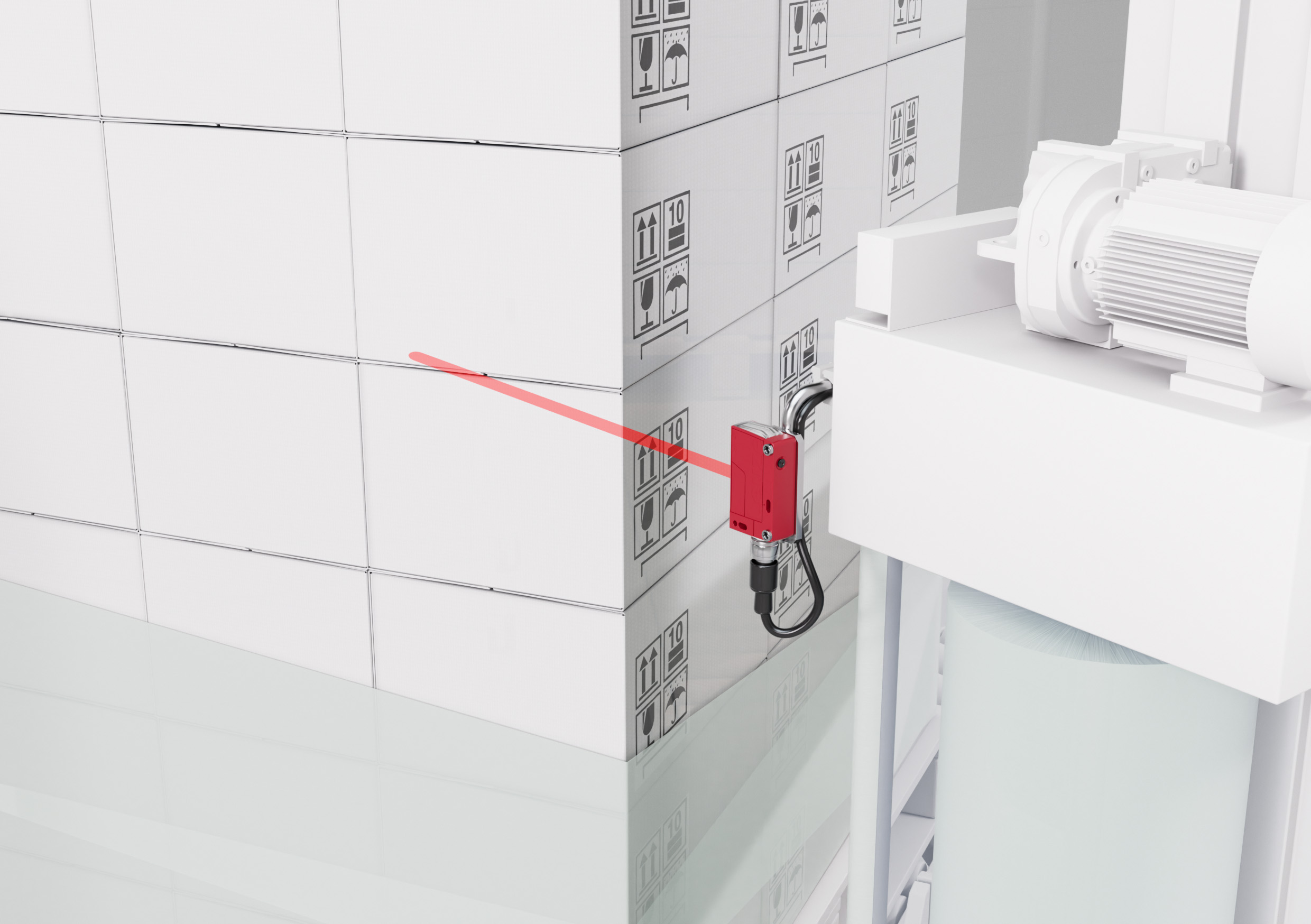
Requirement:
For a correct winding process, the maximum height of the pallet is to be detected. The upper edge of the pallet must be detected in order to control the film carriage.
Solution:
The HT 46C diffuse sensor detects the upper edge of the loaded pallet at an operating range of up to 3 m with defined fading independent of the objects that are on the pallet.
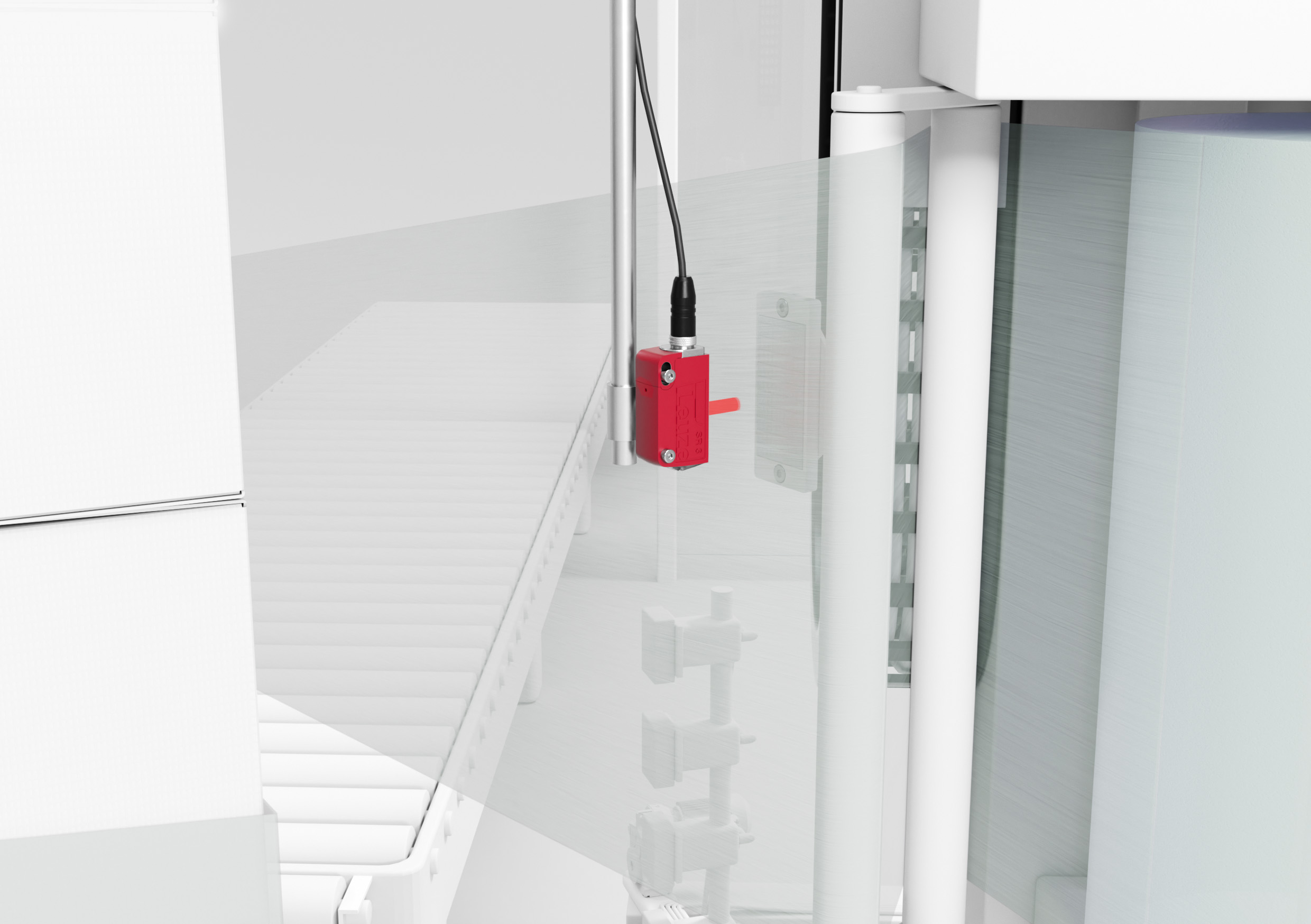
Requirement:
During the winding process, the presence of the film used must be monitored. Any film tears that occur must be reliably detected. A suitable sensor is important for detecting the often transparent or partially transparent film.
Solution:
The polarized PRK3C.A or PRK25C.A retro-reflective photoelectric sensors are suitable for the detection of transparent films. The integrated IO-Link interface provides extensive diagnostic options as well as the possibility to parameterize the devices remotely. MTKS reflectors or REF6 reflective tapes are used as reflectors.
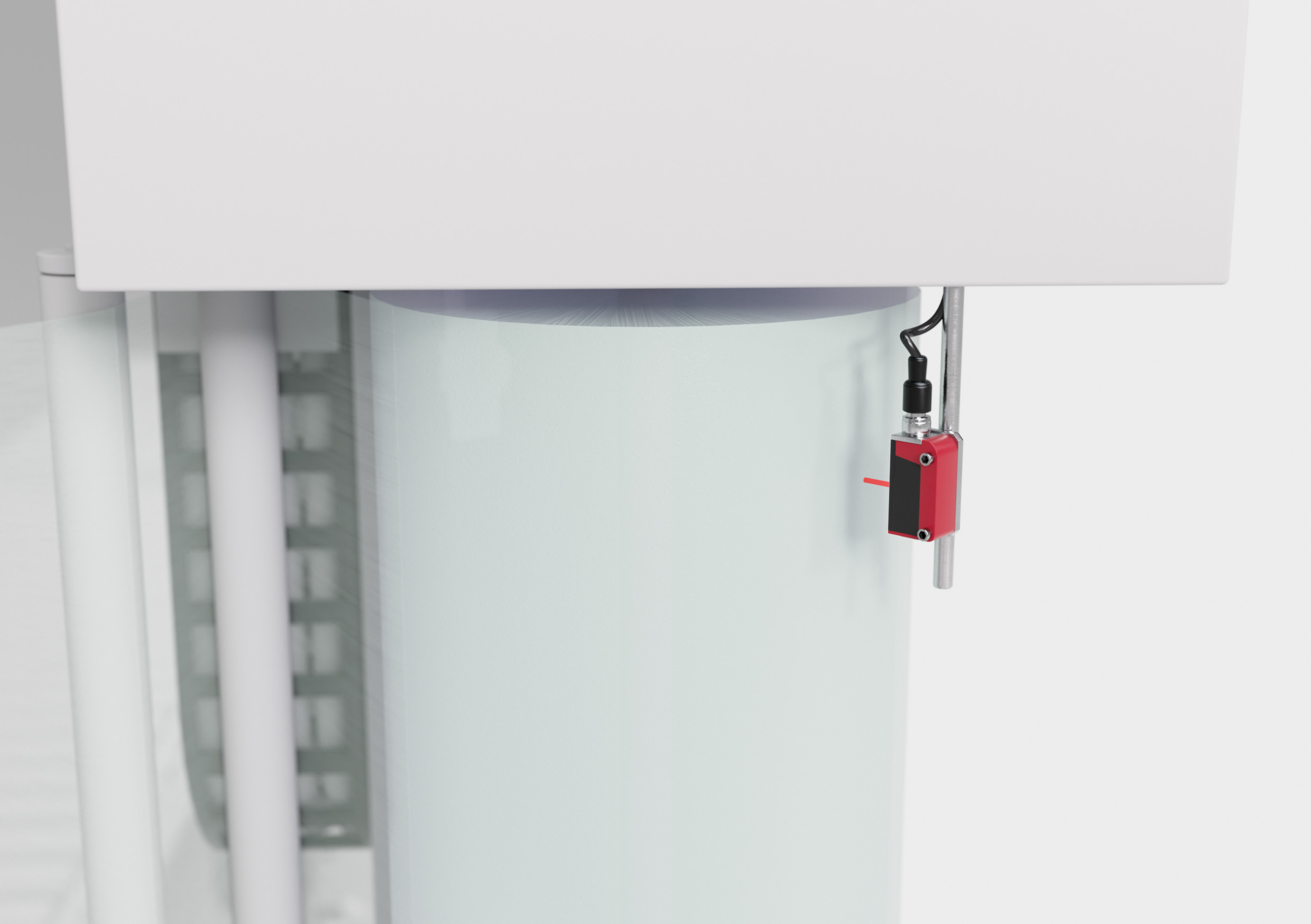
Requirement:
For a reliable winding process, the film supply is to be monitored in order to receive a signal in time for a required roll change. A sensor is to be used that can reliably detect the residual quantity independent of the type of film.
Solution:
The HT3C and HT25C diffuse sensors with highly visible red light spot allow fast alignment in the machine and detect the film roll independent of color and surface. The sensors can be adjusted either with a potentiometer or via the integrated IO-Link interface.
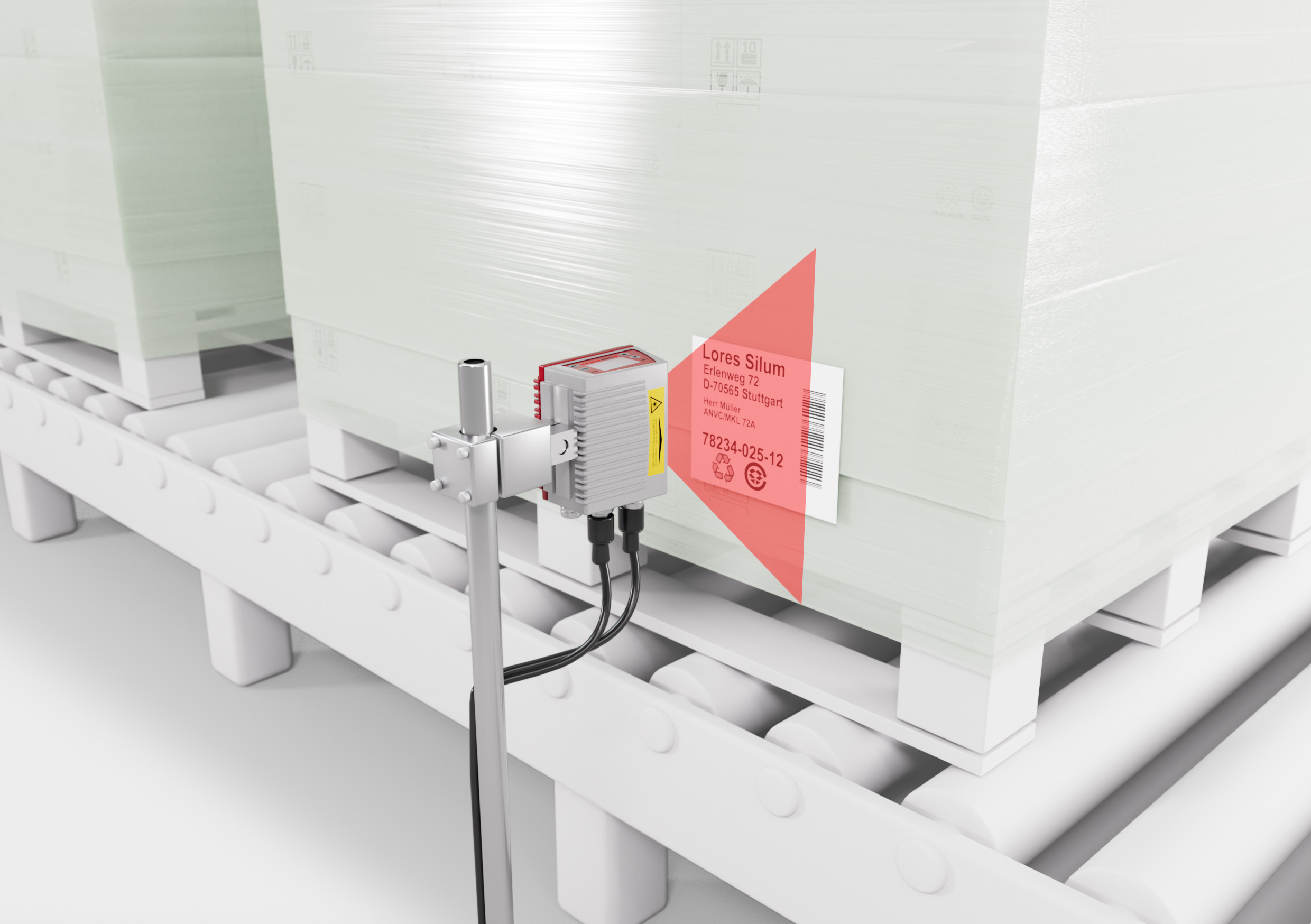
Requirement:
After palletizing and successful load securing, the goods code on the attached bar code labels is to be read in and transferred to the higher-level goods management system.
Solution:
A bar code reader of the BCL 500i / BCL 600i series is used to read the pallet label. Integrated fieldbus networkability is one of the key features of this series and enables fast connection to different controls. The CRT technology enables damaged codes to be read reliably.
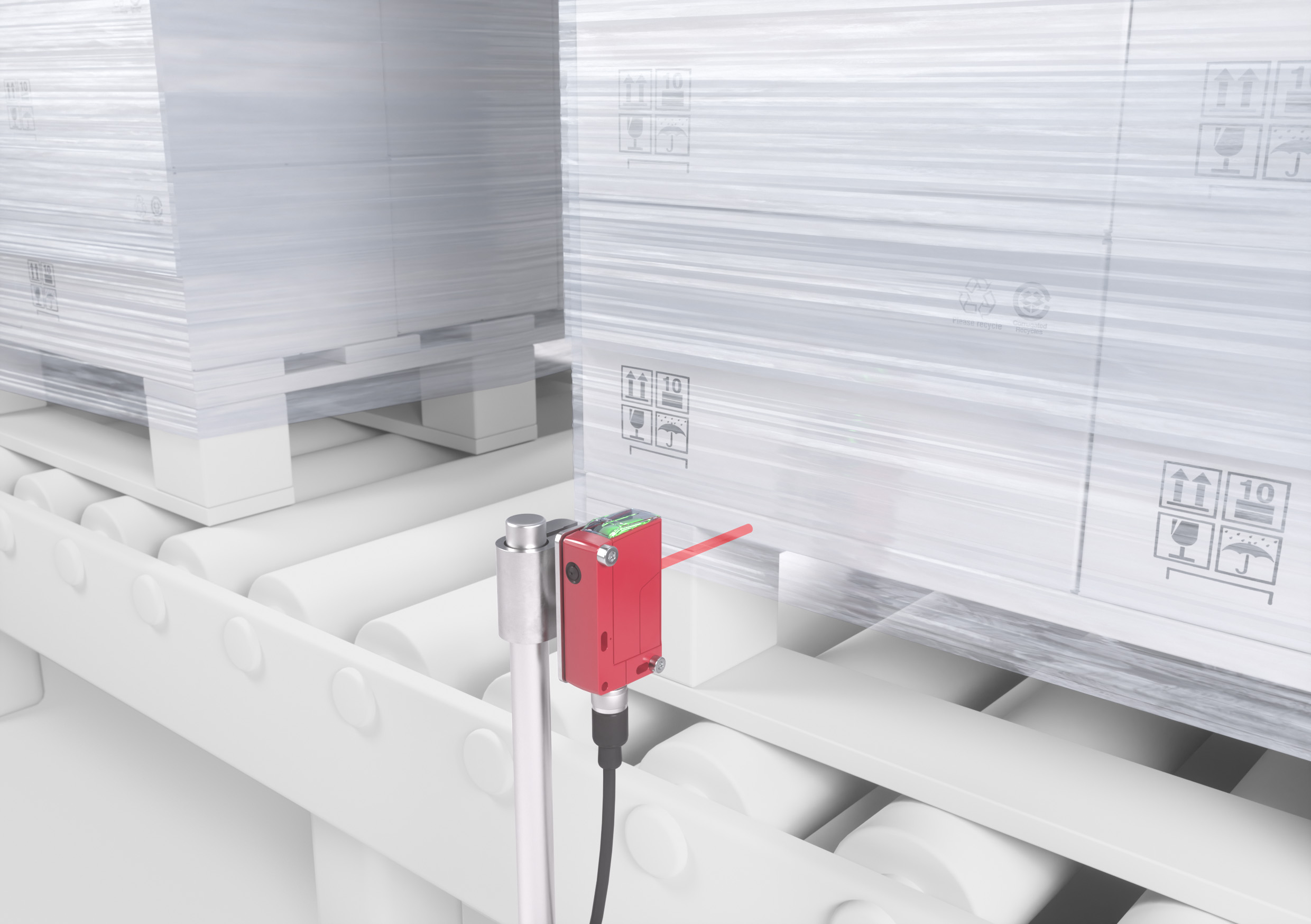
Requirement:
The film-wrapped or shrink-wrapped pallets should be reliably detected over the entire pallet length. The sensor used must not generate any switching errors.
Solution:
The PRK 46C.D retro-reflective photoelectric sensors are optimized for use on roller conveyors. They offer high functional reliability especially for film-wrapped and shrink-wrapped pallets. The sensors with a degree of protection IP 69K are mechanically very robust and very reliable due to the high function reserve with an operating range of 16 m.
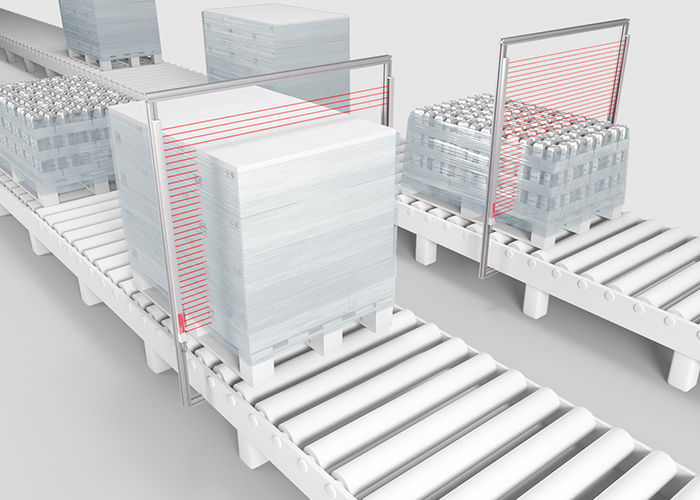
Requirement:
Before a loaded pallet can be conveyed into the conveyor system or into an automatic storage system, the external dimensions and any projecting edges of the pallet must be checked.
Solution:
The CSL 710 switching light curtains or the CML 720i measuring light curtains check the dimensions of the loaded pallet during transport. Different resolutions and measurement field lengths as well as several configurable outputs allow the devices to be optimally adapted to the application.