Leuze SmartID-Edge
Maximum transparency of object and process data through intelligent, secure identification at edge level
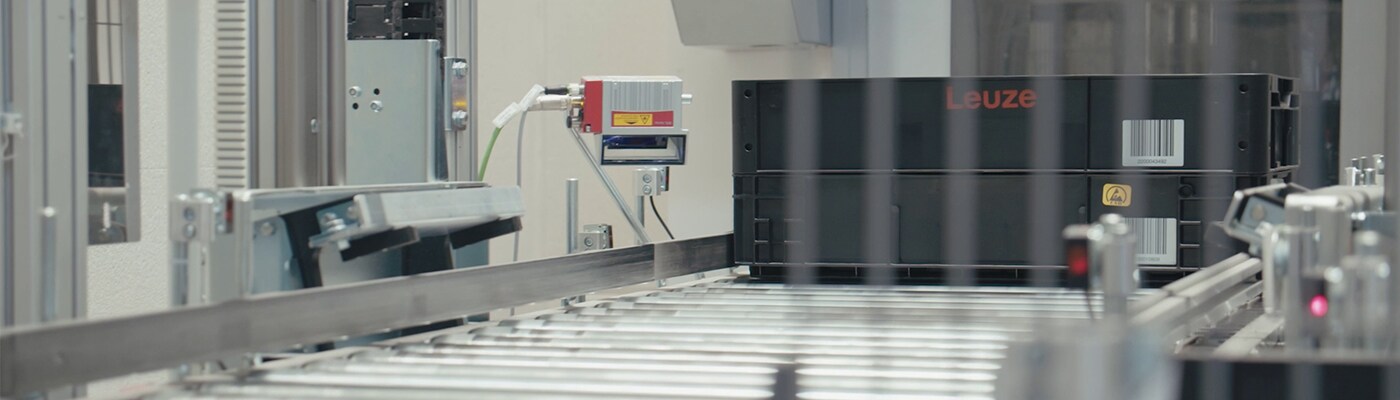
Leuze SmartID-Edge controls a network of identification systems and sensors for track-and-trace requirements in production and the supply chain. Secure communication between 1D scanners or 2D camera systems takes place at edge level using OPC UA and full integration of the AutoID Companion Specification.
The advantage: Each object to be identified is not only represented by its code, but also mapped on a virtual tag in the edge system. Further process, status and sensor information can then be assigned to the virtual tag. This data is available in real time across all processes. Data exchange is even synchronized across network boundaries. This means that all information for continuous process tracking is instantly available at field level. This relieves the burden on higher-level IT systems such as MES.
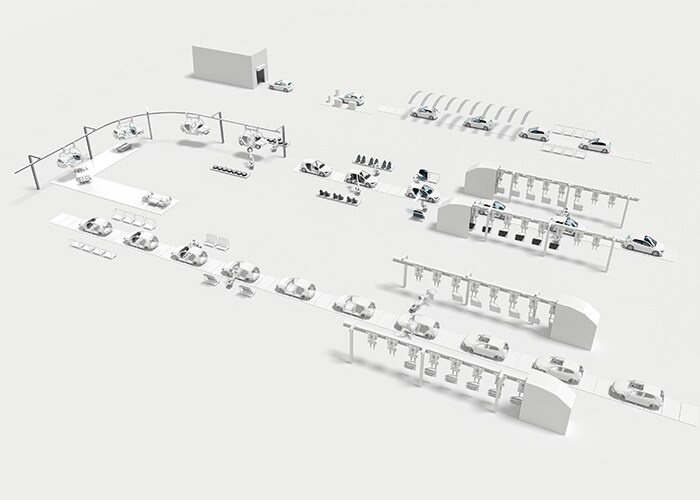
Digitization and networking are central topics of our time. In the industrial environment, they shape concepts such as Industry 4.0 and the Industrial Internet of Things (IIoT). Networking plays a particularly crucial role in today’s automation systems in production and logistics. The goal here is to be able to call up the production processes’ exact status at any time and to keep a complete overview of the production-relevant data at field level. This involves key questions such as: How can users efficiently achieve maximum transparency in their production processes? And how secure is the communication between the network participants?
Multiple requirements for efficient identification
Modern automation systems in production or intralogistics have a number of control systems, sensors and actuators. These are networked with each other via Ethernet-based communication or fieldbus systems and can exchange data. Sensors generate event-based signals to activate production processes or provide measurement values to monitor correct production processes and quality requirements. AutoID systems such as 2D camera systems and RFID readers identify objects, load carriers and containers in production and in the material flow.
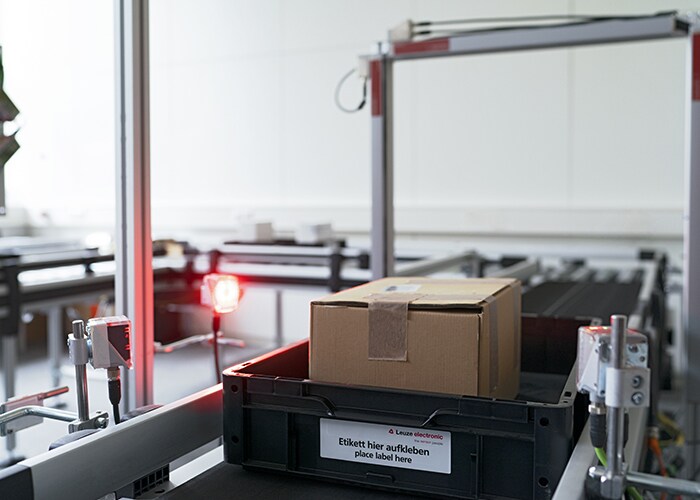
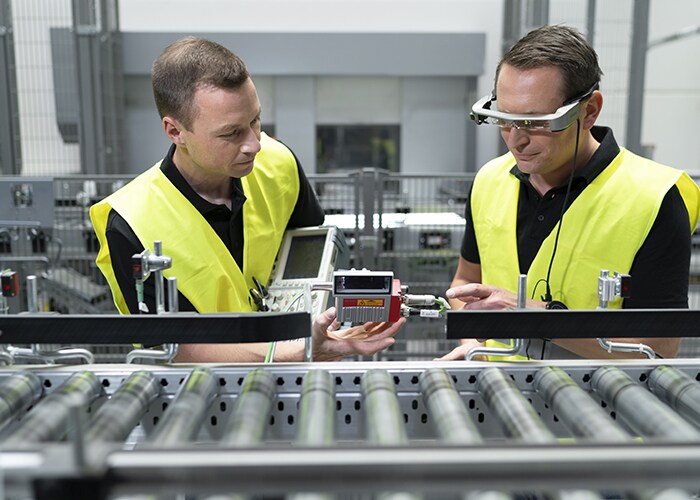
Modern identification systems typically need to be able to handle variable amounts of data and different code systems, depending on the object to be identified. With classic 1D/2D codes, however, these possibilities are limited because standardized bar codes such as a Global Trade Item Number (GTIN) only provide a defined, unchangeable and rather small amount of data. Furthermore, a bar code always requires access to a higher-level IT system such as MES or ERP, where the complete data record that the bar code represents is stored. RFID benefits from the flexibility of the data carriers (‘tags’) used, in addition to the physical principle’s other advantages. These usually have a freely programmable electronic memory – this means that product and process data required for specific situations can be stored directly on the object. For economic or technical reasons, however, it is not always practical or possible to use RFID. Frequent changes of media from bar code to RFID are also undesirable in continuous production processes because they result in increased effort in automation processes and data handling.
SmartID-Edge: Using data more intelligently
This is where the SmartID-Edge concept from Leuze comes in. It uses standardized RFID mechanisms to process and store identification data while retaining the classic optical bar code technology. This is achieved by linking RFID data structures and command sets with standard bar code scanners and camera-based scanners using OPC UA as the data exchange standard and a fully integrated AutoID Companion specification. Each physical bar code is assigned a virtual RFID tag, which is stored in a database on an edge server. Data is exchanged at field level exclusively between the bar code devices and the edge server. The system’s control system, for example a PLC, has no access to the edge server – the PLC can only access the bar code identification systems, although these behave like RFID systems.
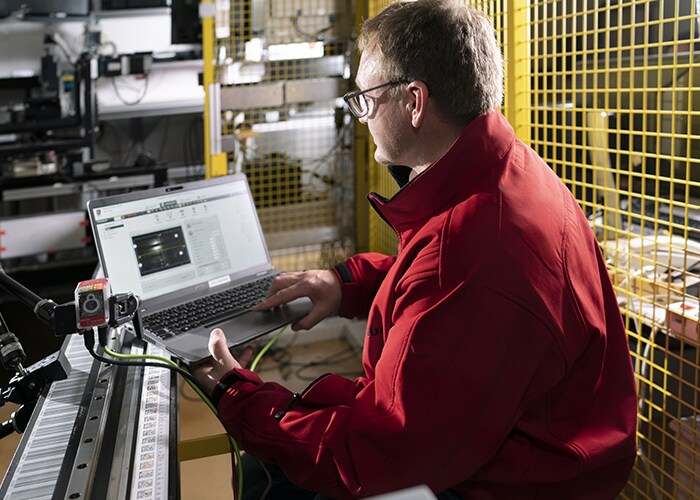
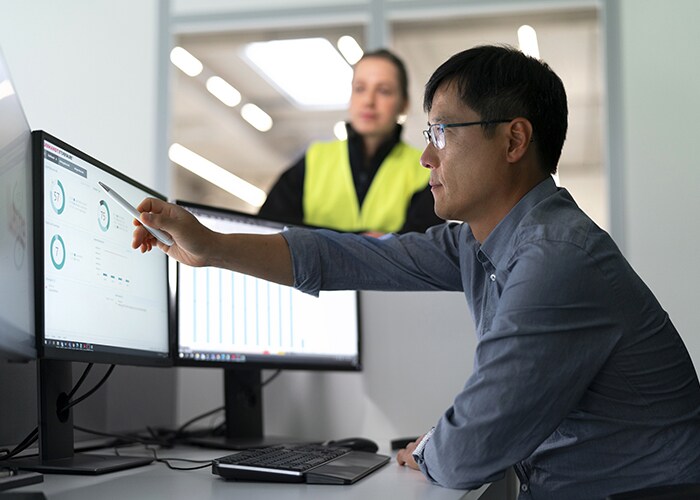
This opens up unprecedented possibilities for enriching data when identifying objects in the production process: In addition to the unique object ID, status information about the identification system as well as reading quality and other process and status data can be stored in a data record. This data record can be accessed directly in real time at field level. Queries to MES and ERP systems are no longer necessary, which relieves data traffic in the networks and frees up system resources at the IT level. Multiple local sensor and AutoID networks can be synchronized via distributed edge servers. This means that all identification events are available throughout the network at all times. Linking these local events with the associated information stored in the edge database over the entire production lifecycle thus provides the basis for the digital twin. This can even be achieved within a supply chain with different suppliers and plants by expanding the edge server with an API and cloud connection. This allows logistics to work more efficiently, eliminates manual data entry and avoids complex system transitions in business software (ERP).
Maximum security
Measures for secure communication are essential for trouble-free, smooth use of networked systems. Here, the SmartID-Edge solution offers several integrated security mechanisms. Modern automation components and identification systems with communication via Ethernet-based interfaces or fieldbuses such as ProfiNet, Ethernet/IP or EtherCAT have integrated web servers. The web servers allow convenient access to the devices in the local network. To meet the high requirements for adaptability, precision and performance, any necessary updates to the device firmware must be fast, reliable and secure. Recognized functional improvements can thus be implemented without replacing the device and new functions can be implemented automatically. At the same time, it must be ensured that only authorized firmware is loaded into the device and that the data transfer cannot be manipulated. These requirements for secure data transmission are becoming fundamental cornerstones of modern automation systems that communicate locally in networks and via cloud systems, not least due to the EU’s Cyber Resilience Act.
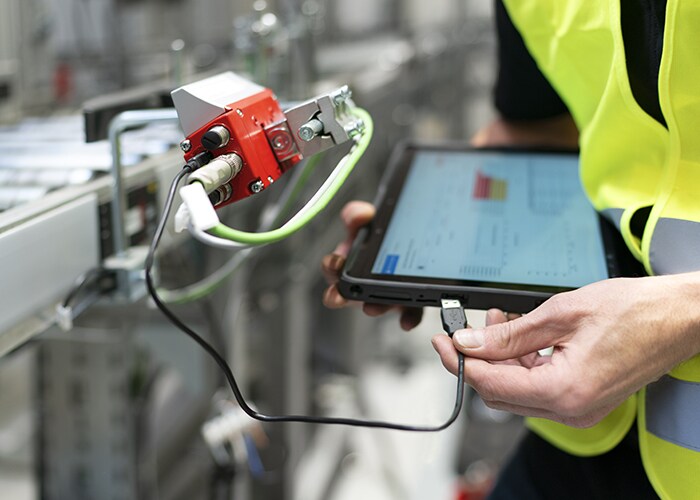
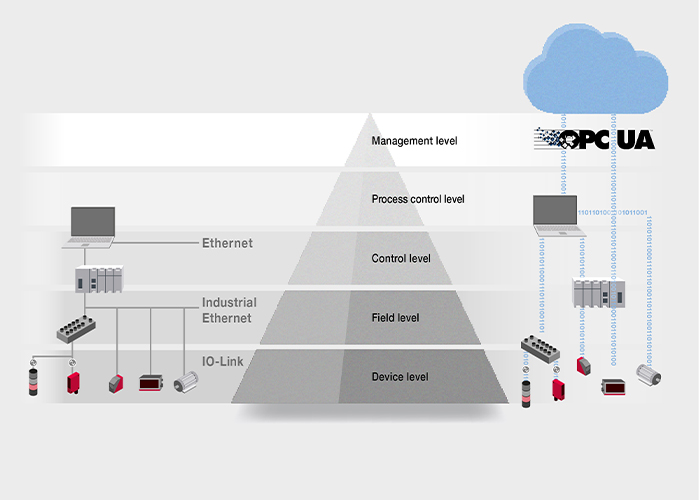
OPC UA provides an interoperable, Ethernet-based communication platform that features integrated end-to-end encryption. In addition, the OPC UA Device Interface Specification Part 100 defines a vendor-independent procedure for performing and managing software updates. The direct loading procedure is recommended for devices with limited hardware resources. The new software is transferred as a file archive, whereby each file is checked by its specific header and installed immediately after unzipping. After a final check, the device is restarted. All communication via OPC UA and thus also the software download are secured by exchanging certificates between client and server. Automated certificate exchange via an external Global Discovery Server (GDS) ensures central management of applications and certificates in the entire OPC UA network. Communication between the network participants therefore meets the highest security requirements: Data cannot be manipulated. This ensures that each device is always operated with the latest and, above all, exclusively original firmware.
Summary
SmartID-Edge offers a powerful platform for networking identification systems at field level. The special concept of data handling using edge servers and virtual data carriers offers maximum transparency in track-and-trace applications as well as efficient access to object and process data at every point in the supply chain in real time. It also meets the high requirements for cyber resilience thanks to its integrated security mechanisms.
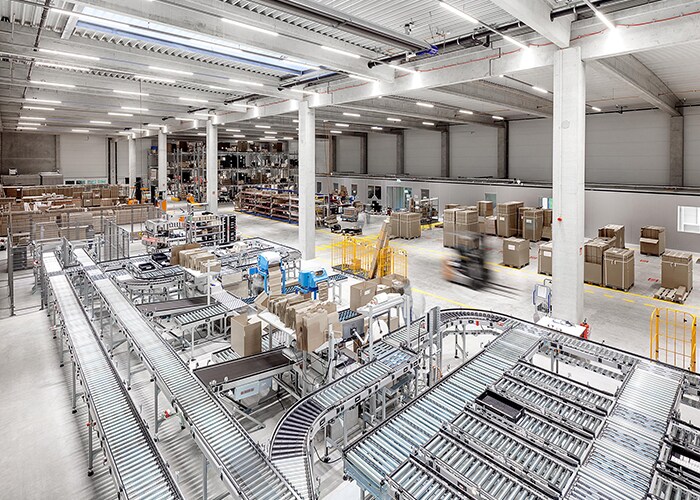