A Safe Bet for a Sweet Deal
Competitiveness thanks to quality assurance
As one of the leading sugar and food companies in Europe and with operations all over the world, the Südzucker AG Group prioritizes quality: To ensure that this is reflected in its products, the group uses modern, technical systems and reliable, automated processes. This applies from the manufacturing process to the intralogistics processes – which involve removing the sugar bags and pails, which are loaded on euro palettes, from storage in the high-bay warehouse – right through to the loading of the freight trucks docking in the loading bay. This is made possible by competent partners such as the sensor experts Leuze. Working together with Südzucker, an efficient safety solution was tailored to the company's specific application. As a result, the clout and competitiveness of the Ochsenfurt location is constantly growing.

On its journey to becoming the sugar that is ultimately removed from storage in the high-bay warehouse and loaded into freight trucks, a beet must first pass through numerous stages: The first of which is the weighing process. Each day during a sugar campaign from September to January, several thousand metric tons of beet are delivered to the Ochsenfurt site by regional farmers. First, these beets must be weighed, their soil content estimated and their sugar content determined. As with all internal processes, unloading follows the "safety first" rule. Safety must be ensured at all times, in this case meaning that no one is in the danger zone of the tilting platforms while the freight trucks are being unloaded. This is ensured by multiple MLD protective sensors installed by Leuze. These sensors form part of the safety concept that has been developed for Südzucker by Leuze safety experts. During a sugar campaign, the seven sugar "towers" on the Südzucker factory premises are filled. These towers serve as silos and contain the entire supply until the next harvest.
The next stages in the process are juice extraction, clarification, evaporation and crystallization through to re-use and recycling of the byproducts animal feed, molasses and Carbokalk fertilizer. With approximately 230 employees, the state-of-the-art sugar factory in Ochsenfurt is one of the largest and most important of the group's factories. Located in Germany's Franconia region, the factory specializes in the further processing of crystalline sugar to liquid and paste refined products for use in the food processing industry, apiaries and bakeries. These products include liquid sugar for soft drinks, fondants for filings and glazes on baked goods, and bee feed (APIinvert, APIfonda).
Storage of bags and pails of merchandise
The high-bay warehouse at the Ochsenfurt factory is enormous: It offers over 72,000 storage spaces. The seven aisles can house up to 6000 euro palettes, on which bagged merchandise and pails are stored. The bagged goods in the high-bay warehouse have already been secured to the euro palettes with stretch film to safeguard the merchandise during transportation. Pails of merchandise are secured shortly before they are loaded onto the freight truck. On average, a complete turnover of the warehouse stock takes no more than four weeks.
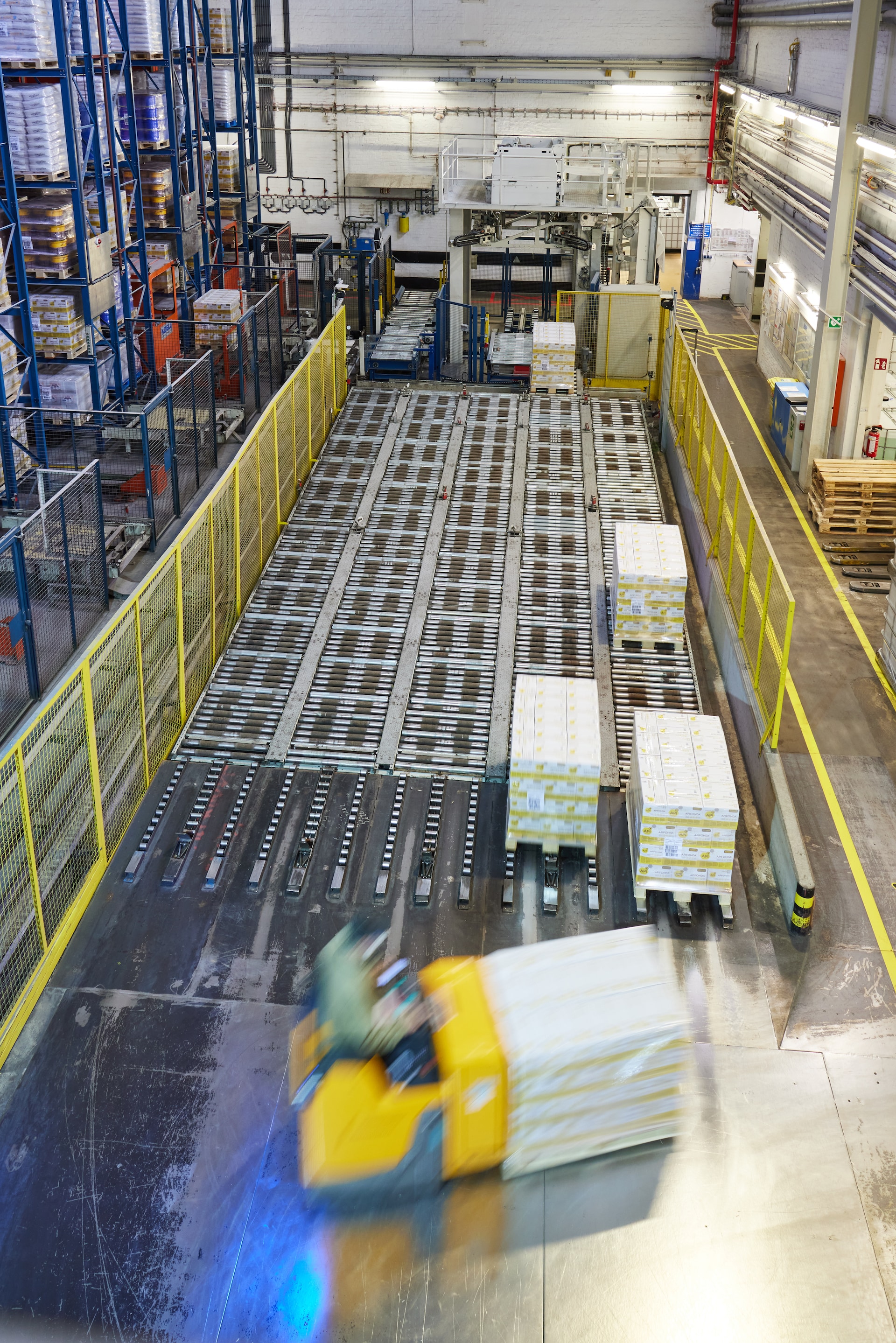
Depending on the quantity of merchandise taken out of storage, between 10 and 25 sugar freight trucks leave the Ochsenfurt factory each day. A maximum of two freight trucks can be loaded simultaneously. The loading process is assisted by up to two electric low lift trucks working simultaneously. When a freight truck docks, the warehouse logistician uses SAP to retrieve the relevant merchandise directly from the high-bay warehouse. The ordered euro palettes arrive at the end of the intralogistics process chain via roller conveyors: a five-track gravity conveyor that is loaded with pallets by a cross conveyor. The five roller conveyors of the gravity conveyor are positioned very close together. The euro palettes to be conveyed that have been safeguarded for transportation are transferred directly to the gravity conveyor and transported to their transfer point. The warehouse logistician determines which of the five conveyors is controlled by entering the respective order. Euro palettes that have not been secured are diverted onto a separate film wrapper before they are supplied. This process is safeguarded by MLD protective sensors from Leuze. Here, these pallets are packaged in film for transport safeguarding so that they too are secured to their euro palette. When the pallets reach the end of the slightly sloping transport system, they are stopped by mechanical brakes. The low lift trucks pick up the pallets at the transfer point, transport them to the docked freight trucks and load them directly.
Traditional safety concepts are often pushed to their limits
In the past, many multiple-track conveyor systems used a single muting light barrier or a photoelectric sensor to safeguard multiple adjacent conveyor lines simultaneously. However, in this type of installation, the muting does not comply with DIN EN IEC 62046 because, if the protective function of the safety light barrier is temporarily suppressed when muting is active, nothing prevents people from entering the danger zone close to a pallet that is being transported out of it, for example by an adjacent transport conveyor. In addition to cost reasons, there are often structural reasons that make it difficult or even impossible to use multiple adjacent muting paths, as is the case at Südzucker. Even "Smart Process Gating," the innovative and more efficient alternative to access guarding that was developed by Leuze back in 2016, could not be used here: This technology, which is patented by Leuze, is based on the Leuze MLC 530 SPG safety light barriers, which make additional muting sensors superfluous. However, Leuze Safety Consultant Dr. Volker Rohbeck quickly realized that even this innovative process could not be applied at this point in the Südzucker factory because, from a structural perspective, it was and remains impossible to position multiple muting or SPG paths next to each other on this multiple-track transport system.
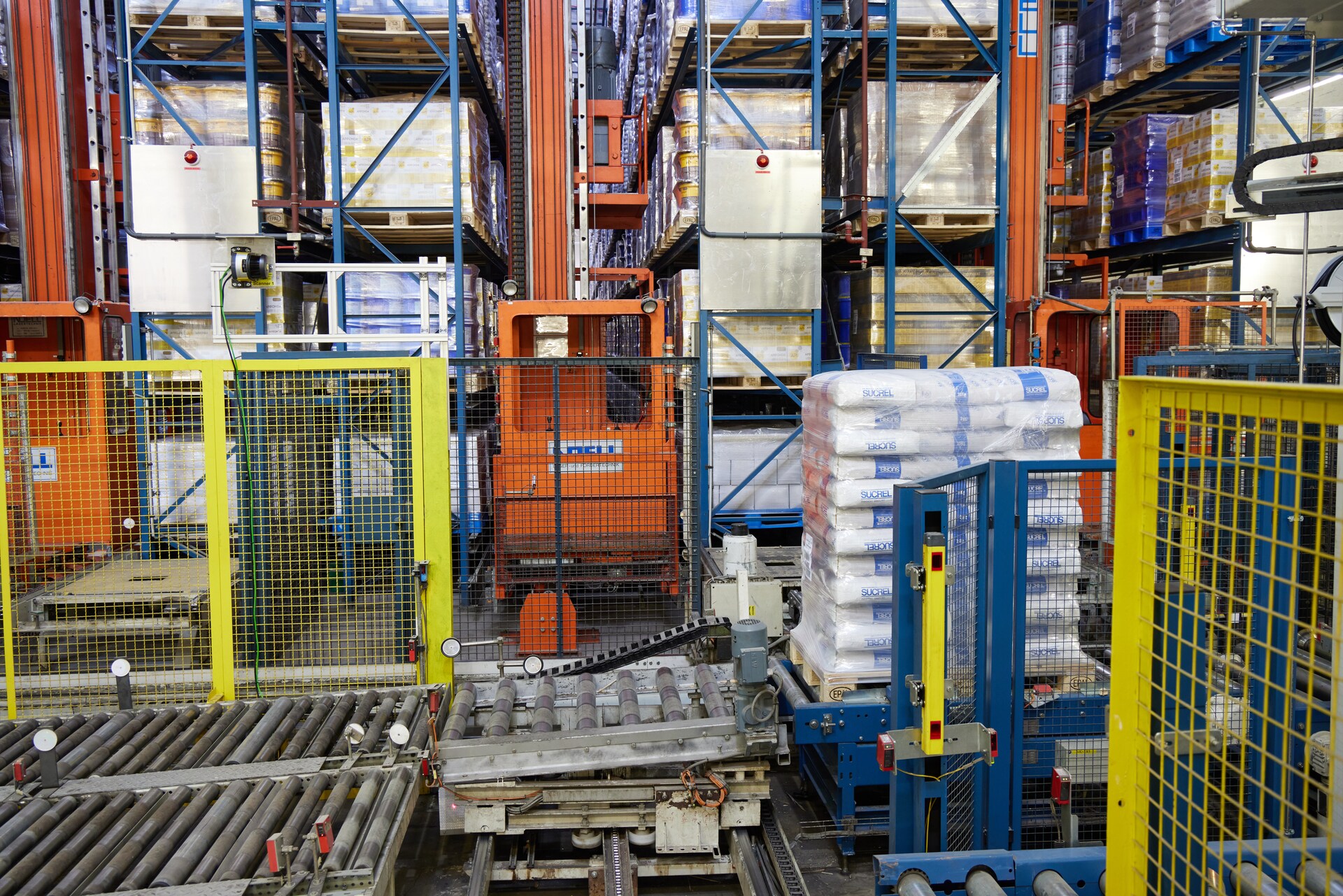
A creative solution was required because it is essential that the area in which pallets are transferred onto the gravity conveyor and the danger zone behind this area are safeguarded against the entry of people by safety technology. Simultaneously, it was important that in each case, the safety solution would only release the conveyor onto which a pallet was most recently output. A new safety concept was required to meet these extended requirements. This concept also needed to offer gapless safety for automatic processes – and at the same time guarantee an efficient material flow as well as high system availability. Therefore, Dr. Volker Rohbeck worked with Dieter Düll, the Master Electrical Engineer at Südzucker who was responsible for the system, to perform a full safety check of the system. Together they looked for new safety solutions that were both safe and efficient and ultimately implemented them. Dieter Düll and Gerald Schmer, who are responsible for automation and electrical technology at the Südzucker warehouse in Ochsenfurt, and Armin Hufnagel, Technical Sales Manager at Leuze, are all delighted with the Leuze sensor solution that was ultimately chosen.
Multiple-track transport system efficiently safeguarded
Now, access guarding of the five-track system for removing pallets from storage at Südzucker is performed by two vertical Leuze RSL 400 safety laser scanners. Together they form a vertical protective field that covers all of the tracks. From the system control, the safety system receives the information about the track onto which the pallet is output and adapts the protective fields of the two laser scanners accordingly shortly before the passage of the pallet. If the transverse side-tracking skate transfers a pallet, the system control is notified of this and a protective field in the size of the pallet and at the corresponding point is selected. After the passage of the pallet, the protective fields of the safety laser scanners are reset to their original size and in doing so fully "close" the conveyor area again. In this way, gapless safety during the transport cycles is ensured. This solution also ensures high reliability and availability. The safety system does not require any additional signals, for example from muting sensors. This means that there are also no system-related structural limitations. The solution is tamperproof and ideal for retrofitting existing systems: The two safety laser scanners are controlled by the safety concept's own pre-programmed compact safety controls and are integrated into the system via two-channel safety outputs. Any necessary adaptations of the software for the compact controls and the configuration of the protective fields of the laser scanners are easy to carry out, optionally also as a Leuze service for the respective application requirements.
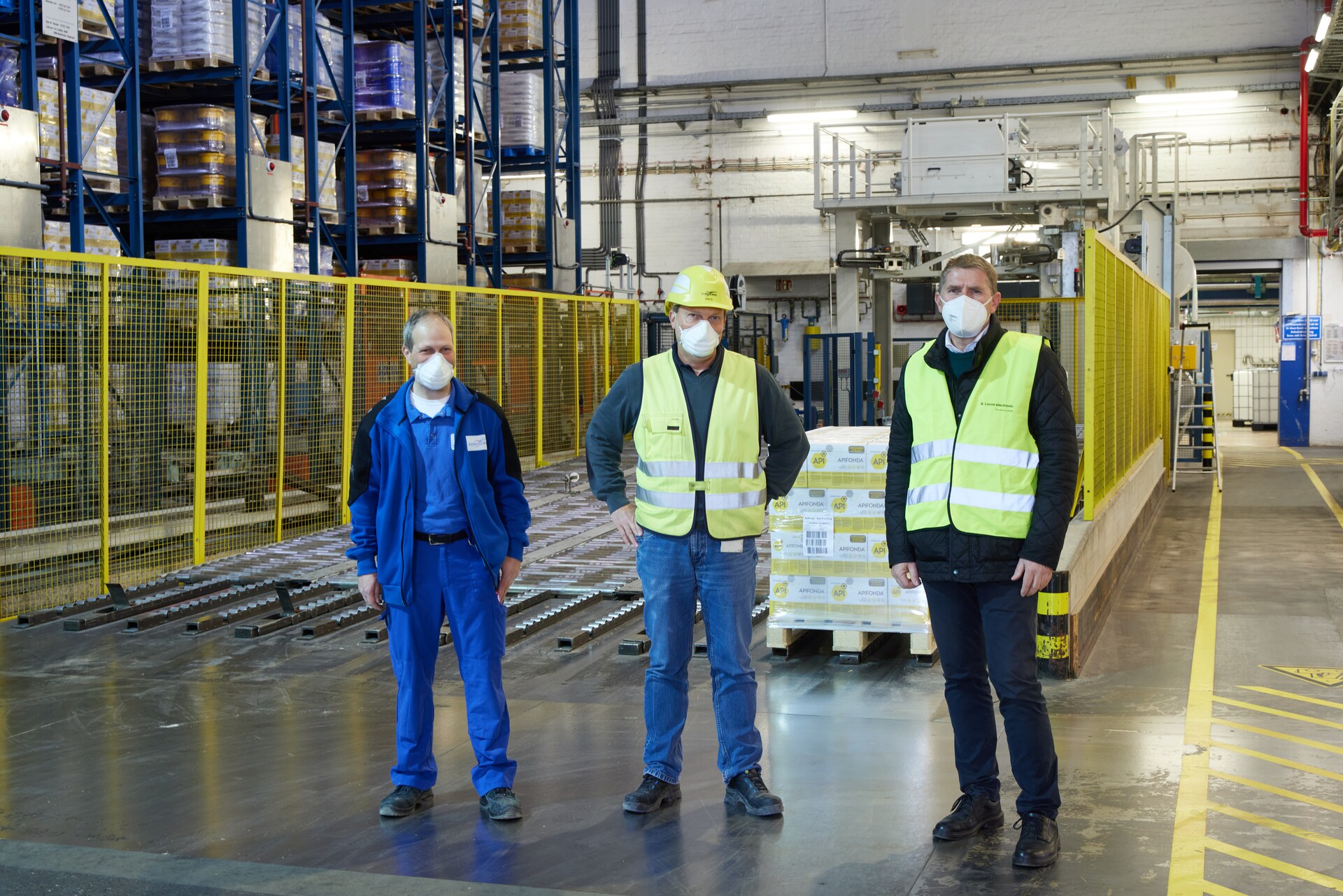
As a reliable partner for efficient sensor solutions, Leuze offers its customers safety products, safety services and safety solutions throughout the machine's entire lifecycle. The Leuze safety experts have comprehensive knowledge of the latest norms and standards and extensive experience in designing safety concepts. They develop efficient, innovative and reliable safety solutions for use in automated environments. Their professional project teams accompany their customers through the entire process – from determination of their specific requirements to safety acceptance. The Leuze safety experts make sure that the safety solution meets the customer requirements and ensure that the project runs smoothly. The safety solutions are based on qualified safety concepts which, if necessary, can also be individually extended or created new. Each solution is individually adapted to the specific system layout and comprises all of the necessary hardware and software components, engineering services such as control programming and configuration in accordance with the project requirements, start-up support, validation of the safety function
and extensive documentation. This saves time and money and guarantees optimum safety. The innovative, intelligent safety concepts offer gapless safety and smooth-running processes even in areas where classic concepts are pushed to their limits.