Sensor solutions for pharmaceutical packaging
In the pharmaceutical industry, packaging processes are usually performed under cleanroom conditions, for example when vials are filled with vaccine doses or blister packaging is filled with tablets. Here, the requirements on hygiene, product safety and reliability are extremely high.
We have supported packaging machine and pharmaceuticals manufacturers for decades and know the challenges of these sectors: Our sensors and the pharmaceutical reflectors specially developed for them are made of high-quality stainless steel and withstand intensive cleaning processes. The 53C series miniature sensors in hygienic design prevent the accumulation of deposits by using housings with smooth contours and no fastening holes, thereby reducing the risk of bacterial carry-overs. To be able to track production batches at all times using pharmacodes or Data Matrix codes, compact code readers such as the DCR 200i in stainless steel housing are a suitable solution. Sensors with integrated IO-Link interface, e.g. the 53C series or our fork sensors, reduce the need for external intervention in machine operation because they enable the sensors to be operated without the cleanroom having to be opened.
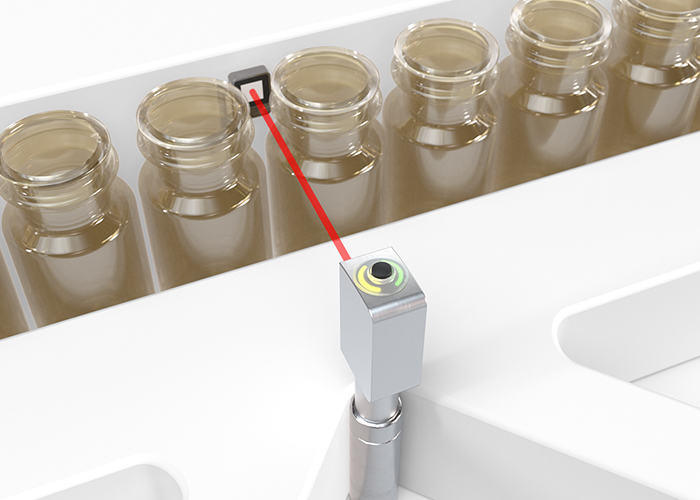
Requirement:
For optimal speed control during transport, vials made of transparent or non-transparent glass must be reliably detected on the conveyor line. Even the smallest gaps must be used. Hygiene requirements are particularly high in aseptic systems.
Solution:
The PRK 53CL1.T3 retro-reflective photoelectric sensors with a small laser light spot, in combination with an MTKS stainless steel reflector, enables high-precision detection and positioning of vials. The compact sensor can be easily integrated even in confined spaces. The sensor and reflector have a hygienic design.
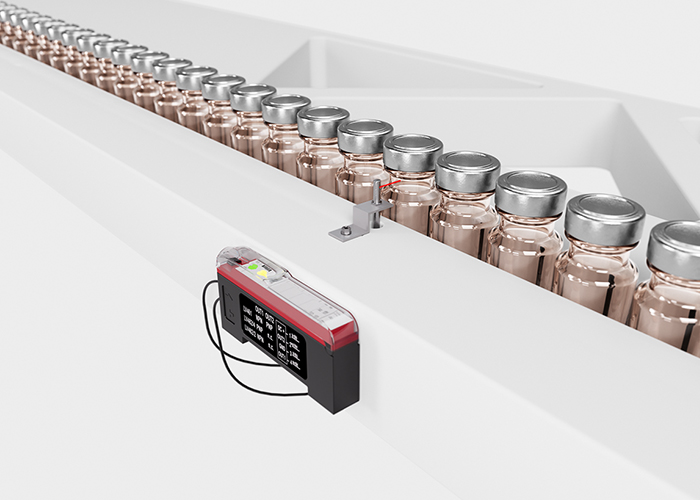
Requirement:
After filling the vials in a packaging machine, the containers are often transported in a constrained space at high speeds and with minimal distance. Due to the constrained space, the sensors used should be particularly small and easy to integrate into the machine.
Solution:
KF plastic fiber optics or GF glass fiber optics with different beam exits and LV 463 amplifiers are a variable solution for the detection of vials. Glass fiber optics are particularly well suited for high ambient temperatures. The amplifiers, which can be conveniently set via the menu, are available with analog output as well as IO-Link interface.
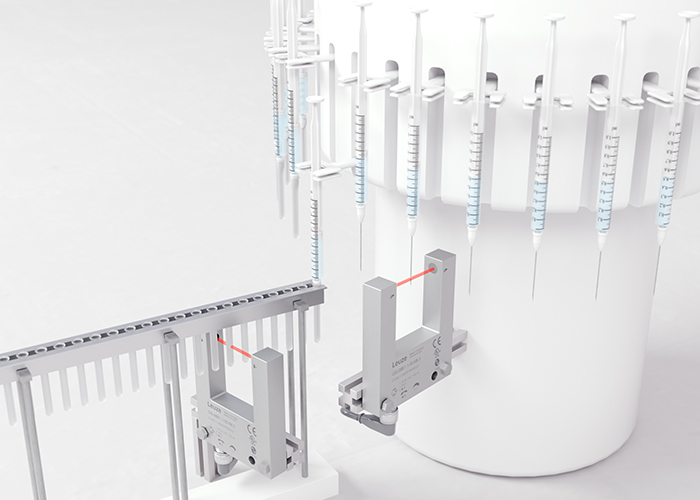
Requirement:
Hanging disposable syringes are transported to an assembly station at high speeds via a feeder unit. Plastic caps are to be fitted on the disposable syringes at this station. In addition, the very thin needles of the syringes are to be reliably detected.
Solution:
The GSL 08B laser fork photoelectric sensor detects even thin syringe needles. The V4A stainless steel housing is suitable for clean rooms and ECOLAB certified, making it ideal for areas with strict requirements regarding hygiene and resistance to cleaning agents. The sensors operate reliably in a temperature range between –25 °C and 60 °C.

Requirement:
In a tube filling and sealing machine, a paste-like product is filled into tubes. During the process, it is important that the plastic tubes are aligned precisely after filling so that the tube fold is pressed in exactly the right place. Space is usually constrained in these machines.
Solution:
The compact KRT 3C contrast sensor saves a lot of space during mounting. It highly precisely detects contrast markers of different colors even on round objects with a short response time of just 50 µs. A time-saving format change can be implemented via the IO-Link interface. For higher requirements, the KRT 55 is available in a stainless steel housing.
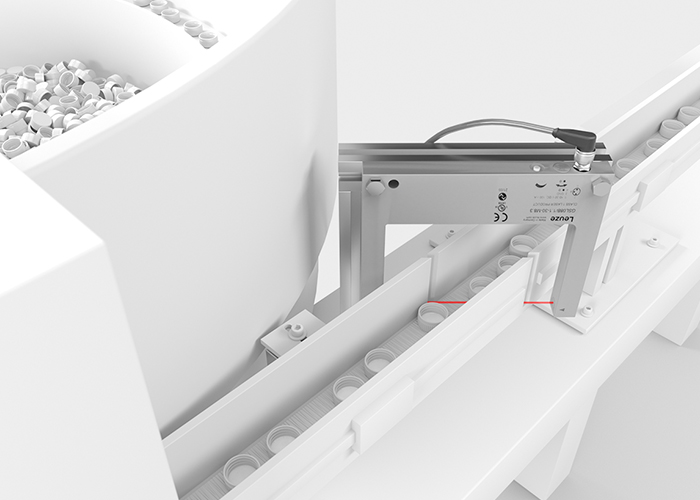
Requirement:
After filling the vials or bottles, other small parts such as caps, locking rings or dosing aids are required, which are often fed to the machine via vibratory conveyors. For the detection of small parts, specially optimized sensors should be used.
Solution:
GS 08B or GSL 08B fork sensors in stainless steel housings with laser light are easy to integrate and reliably detect small objects and even the smallest gaps. Alternatively, KF plastic fiber optics with a suitable LV amplifier can be used to detect small parts.
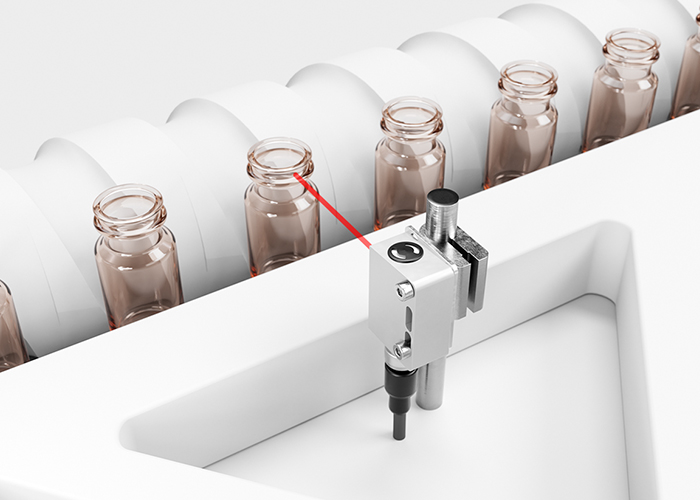
Requirement:
A screw conveyor adapted to the vials is used for collision-free infeed of the vials into the downstream machine. The rotation of the screw in the background requires very precise background suppression from the sensor when detecting the vials.
Solution:
The special V-optics integrated in the HT55C.V diffuse sensor enable very precise background suppression. At the same time, partially transparent objects can be reliably detected. The compact sensor in the stainless steel housing of the 55C series meets the high degree of protection IP 69K.
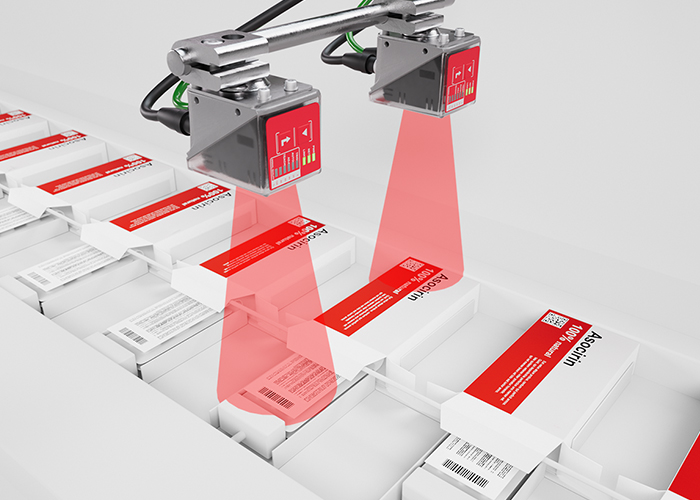
Requirement:
When packaging blisters in folding boxes, it must be ensured that the correct package insert is in the box. For this purpose, both codes on the folding box and the package insert must be read and compared with each other in the process.
Solution:
Two DCR 200i camera-based sensors are used to ensure that the package insert is assigned to the folding box. The sensors can reliably decode Data Matrix codes or Pharmacodes. The code content is output via an Industrial Ethernet interface.
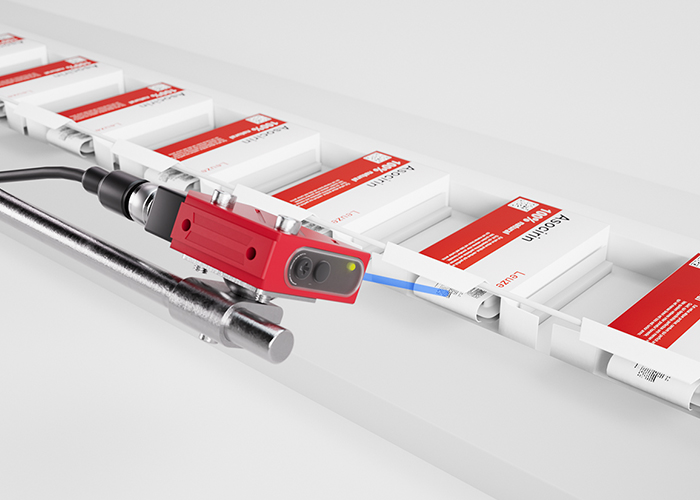
Requirement:
When packaging tablet blisters in folding boxes, it must be ensured that the package insert is also packed. Since the package insert is made of paper, it can be reliably detected with the aid of a luminescence sensor.
Solution:
The LRT 8 luminescence sensor detects luminescent materials by means of UV illumination. Thanks to its small design, it is easy to integrate. Different operating ranges, light spot sizes, and filters make these sensors flexible in use.
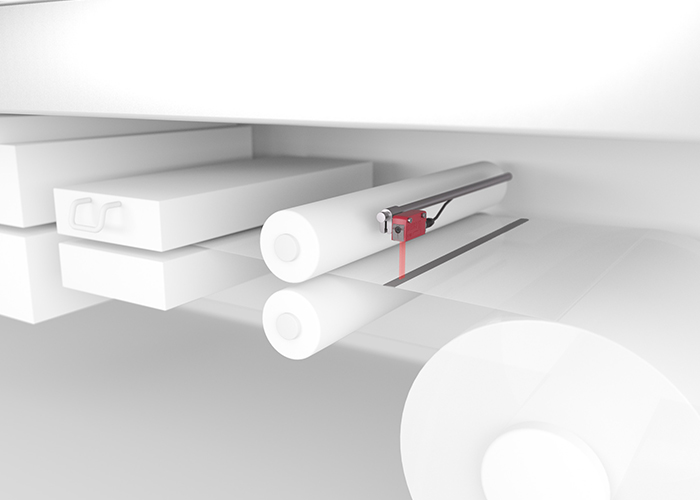
Requirement:
Splices on forming films must be reliably detected for a safe process and must be discharged in the subsequent process. The detection of the splices should be independent of color and surface as much as possible.
Solution:
The KRT 3C, KRT 18B or KRT 55C contrast sensors are optimized for detecting splices. The color of the adhesive tape and the background is adapted using the teach button. The IGSU14E SD ultrasonic fork sensor detects splices independently of color on sealing films with different printing.
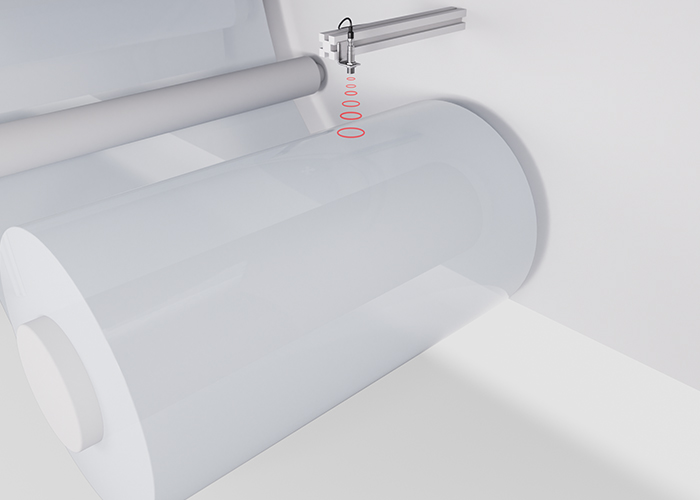
Requirement:
Plastic film for forming blisters is provided in large rolls. To ensure uniform and even unrolling, the roll is often motor-driven. This requires a permanent distance signal from a sensor to determine the diameter.
Solution:
DMU 318 or DMU 418 ultrasonic distance sensors have been developed for precise distance measurement. They provide an analog signal as information on the roll diameter. Alternatively, measuring sensors of the ODS 9 series with different measurement ranges can be used. The integrated IO-Link interface offers further possibilities.
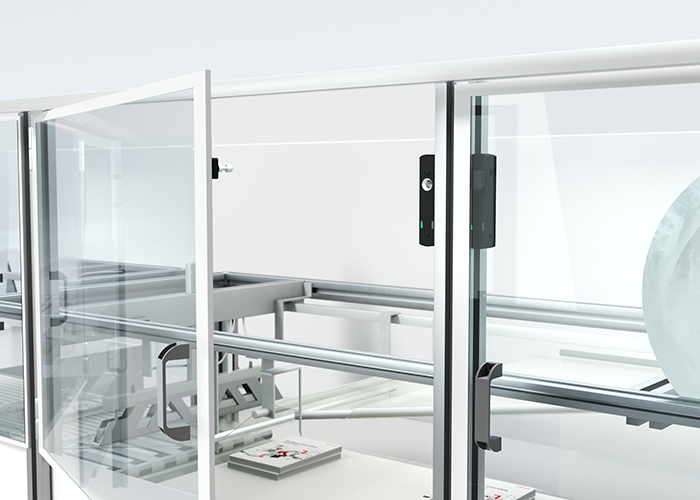
Requirement:
Safety doors on fast-running machines in pharmaceutical packaging must be monitored by safety switches with a locking device to prevent unintentional access and to stop the process only at defined points. The accessibility to the machine should not be impaired in the process.
Solution:
The L250 and L300 safety locking devices keep safety doors locked until the control sends an electrical release signal. Thanks to their RFID-coded actuators, they offer optimum protection against manipulation. The optional emergency stop and command buttons make it easier to set up the complete safety function.