Integrated connectivity
Wenn in einer Anlage Sensor und Schnittstelle perfekt zusammenspielen, hat das Vorteile für Inbetriebnahme, Maschinenüberwachung und Prozessoptimierung. Leuze ermöglicht das durch ihr Konzept der „integrated connectivity“.
Alles im Sensor
Integrated connectivity oder integrierte Konnektivität bedeuten: Alle relevanten Industrial-Ethernet-Schnittstellen sind in den Sensor integriert und die zentralen Gerätefunktionen darüber verfügbar. Was sich einfach anhört, ist jedoch kein Standard auf dem Markt. Stattdessen bieten Hersteller häufig Geräte ohne Industrial-Ethernet-Schnittstelle an und sparen so Entwicklungsaufwand. In diesem Fall wird die Schnittstelle über ein Gateway zur Verfügung gestellt. Weshalb das nicht die optimale Lösung ist, und warum Anlagenbetreiber mit integrated connectivity von Leuze gleich mehrfach profitieren, zeigen nachfolgende Beispiele. Die Vorteile reichen dabei von der Inbetriebnahme (Device Management) über die Maschinenüberwachung (Condition Monitoring) bis hin zur Prozessoptimierung.
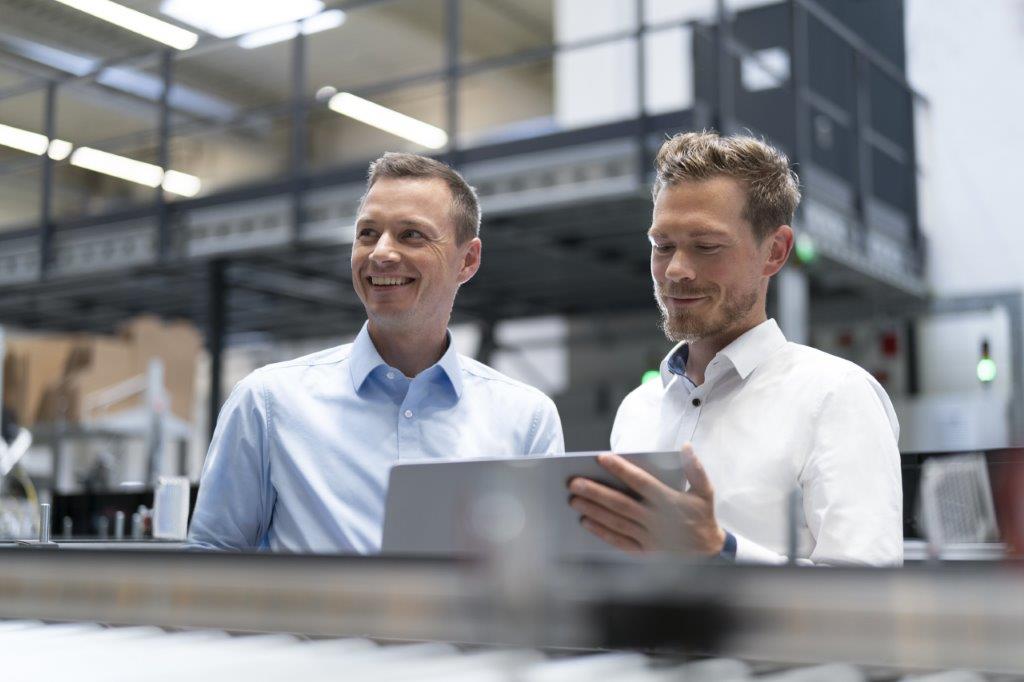
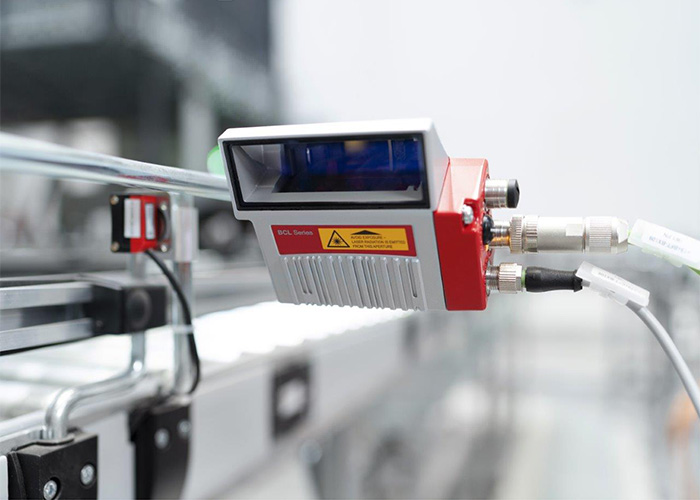
Vorteile von integrated connectivity bei Device Management, Condition Monitoring und Prozessoptimierung
Deutlich schlankeres Anlagenlayout
Leuze bietet Geräte mit integrierten Schnittstellen für PROFINET, Ethernet/IP und EtherCAT an. Wie sehr sich das bereits bei der Inbetriebnahme bezahlt macht, zeigt sich anhand eines beispielhaften Anlagendesigns mit und ohne integrated connectivity. Zunächst ein Blick auf eine Anlage mit Barcodelesern ohne integrierte Schnittstellen: Hier muss jeder Scanner an ein separates Gateway angeschlossen werden – das bedeutet pro Barcodeleser ein zusätzliches Gateway mit eigener Stromversorgung. Der Installationsaufwand und die Kabelmenge sind damit doppelt so groß wie nötig. Außerdem ist die Parametrierung deutlich aufwändiger. Nicht zu vergessen: Durch die erforderlichen Gateways befinden sich deutlich mehr Geräte in der Anlage, die eine Störung verursachen können und die in diesem Fall kontrolliert werden müssen. Im Vergleich dazu dieselbe Anlage mit integrated connectivity: In jedem Barcodeleser ist die Industrial-Ethernet-Schnittstelle bereits integriert. Das macht separate Gateways überflüssig. Vor allem ist die Anlage deutlich übersichtlicher und es sind weniger Kabel erforderlich. Letztendlich lassen sich so auch Störungen schneller beseitigen, weil weniger Geräte geprüft werden müssen.
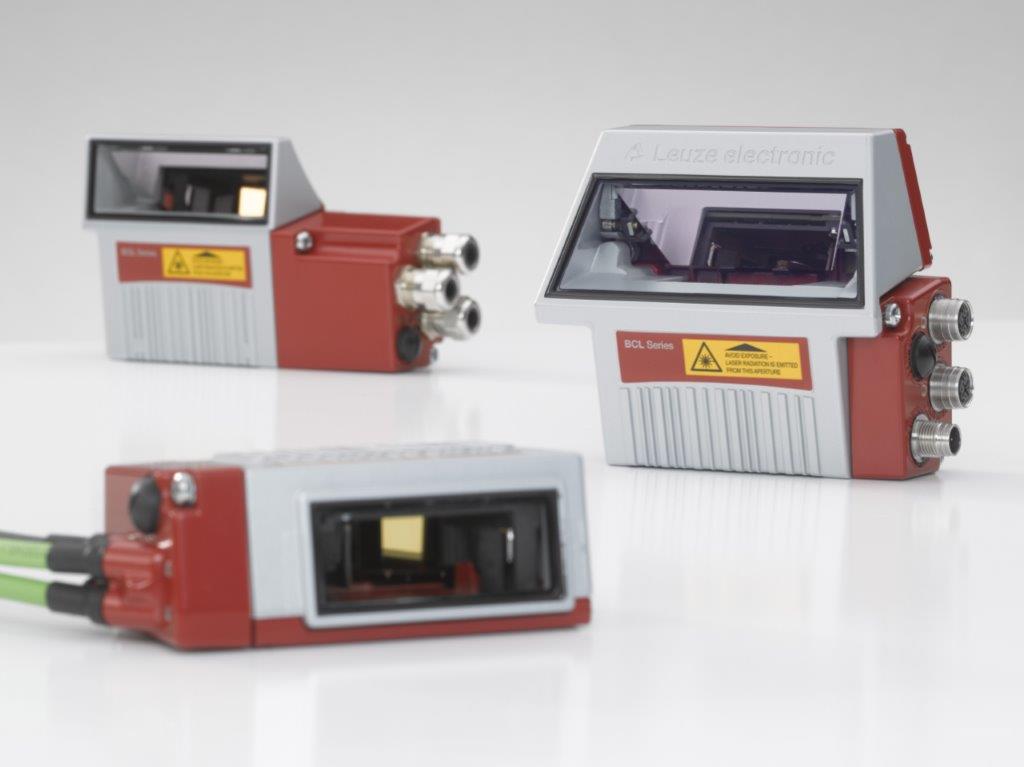
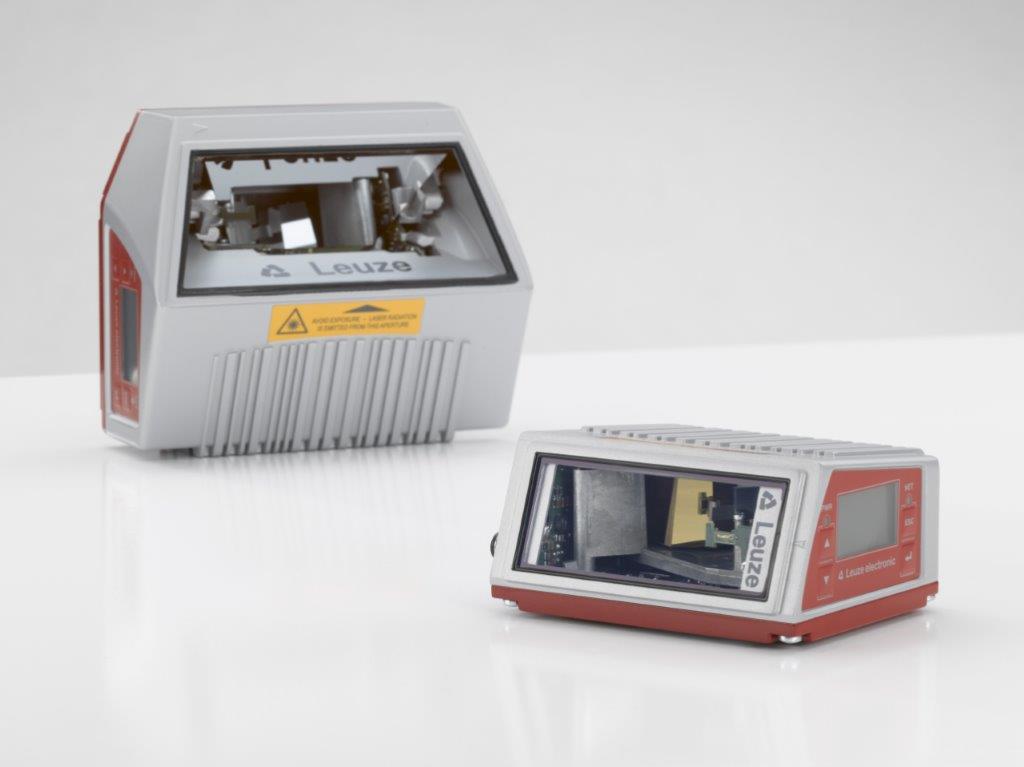
Die Barcodeleser der Serie BCL von Leuze sind mit „integrated connectivity“ ausgestattet.
Switch inklusive
Leuze Sensoren mit integrated connectivity zeichnen sich in einem weiteren Punkt durch eine besonders effiziente Inbetriebnahme aus: Die Geräte enthalten standardmäßig einen Switch, also je einen Ethernet In-Port und einen Out-Port. Anlagenbetreiber sparen dadurch einen externen Switch. Außerdem lassen sich mehrere Geräte deutlich einfacher verkabeln, beispielsweise in einer Ring- oder Linientopologie. Bei einer linearen Verkabelung verbindet der Anlagenbetreiber über die integrierten Switches einen Sensor mit dem nächsten. Erst der letzte Sensor in der Reihe ist mit der Steuerung verbunden. Hier liegt der Nutzen ebenfalls in einem einfacheren Anlagedesign und weniger Kabeln. Geräte ohne integrierten Switch benötigen dagegen einen externen Ethernet-Switch. Zudem müssen Anwender:innen dann jeden einzelnen Sensor über eine Sterntopologie mit dem Switch verbinden und diesen dann an die Steuerung anschließen.
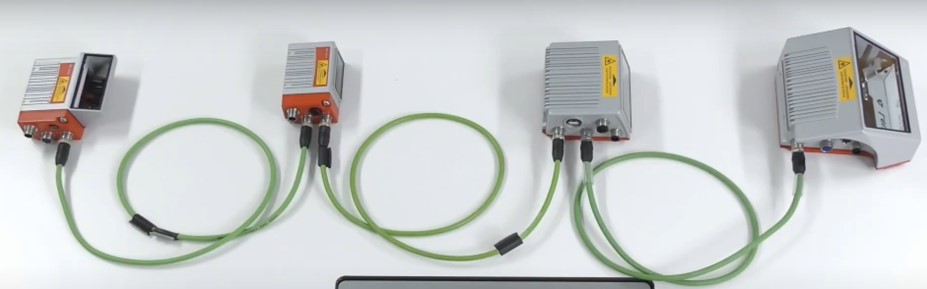
Die Realisierung einer Linientopologie per integriertem Switch reduziert den Verkabelungsaufwand und spart so Zeit und Kosten.
In der gewohnten Steuerungsumgebung
Integrated connectivity bedeutet auch, in der gewohnten Steuerungsumgebung arbeiten zu können. Das ist möglich, weil die gesamte Geräteparametrierung beispielsweise in der GSDML-Datei („Generic Station Description Markup Language“) von PROFINET integriert ist. Viele andere Ethernet-basierte Geräte auf dem Markt müssen dagegen üblicherweise per Webserver parametriert werden. Das ist komplex, weil jeder Hersteller eine eigene Webserver-Version mit einer eigenen Benutzeroberfläche liefert. Als Anwender:in muss man sich jedes Mal neu einarbeiten und die entsprechenden Funktionen finden. Hinzu kommt: Geräte ohne Ethernet, die per Gateway angeschlossen werden, brauchen häufig eine produktspezifische Herstellersoftware zur Parametrierung. Das wiederum kann Probleme bei der Kompatibilität zur eingesetzten Hardware nach sich ziehen. Beispielsweise, wenn der Hersteller seine Software nach einigen Jahren nicht mehr pflegt. Auch hier lohnt sich integrated connectivity gleich mehrfach:
- Anwender:innen bleiben in ihrer gewohnten Softwareumgebung
- Installation von Herstellersoftware und zugehörige Einarbeitung sind nicht erforderlich
- Es wird kein Zugriff auf einen Webserver benötigt
Geräte von Leuze mit integrated connectivity lassen sich sehr einfach parametrieren. Dazu genügt es, über die Steuerung die GSDML-Datei von der Leuze Website zu laden und diese einmalig in die eigene Engineering Software zu kopieren. Anschließend sind die Module im Hardware-Katalog verfügbar. Dabei sind die Gerätefunktionen aussagekräftig beschrieben. Das macht die Parametrierung und Nutzung eines Sensors sehr einfach und das Handbuch in fast allen Fällen überflüssig.
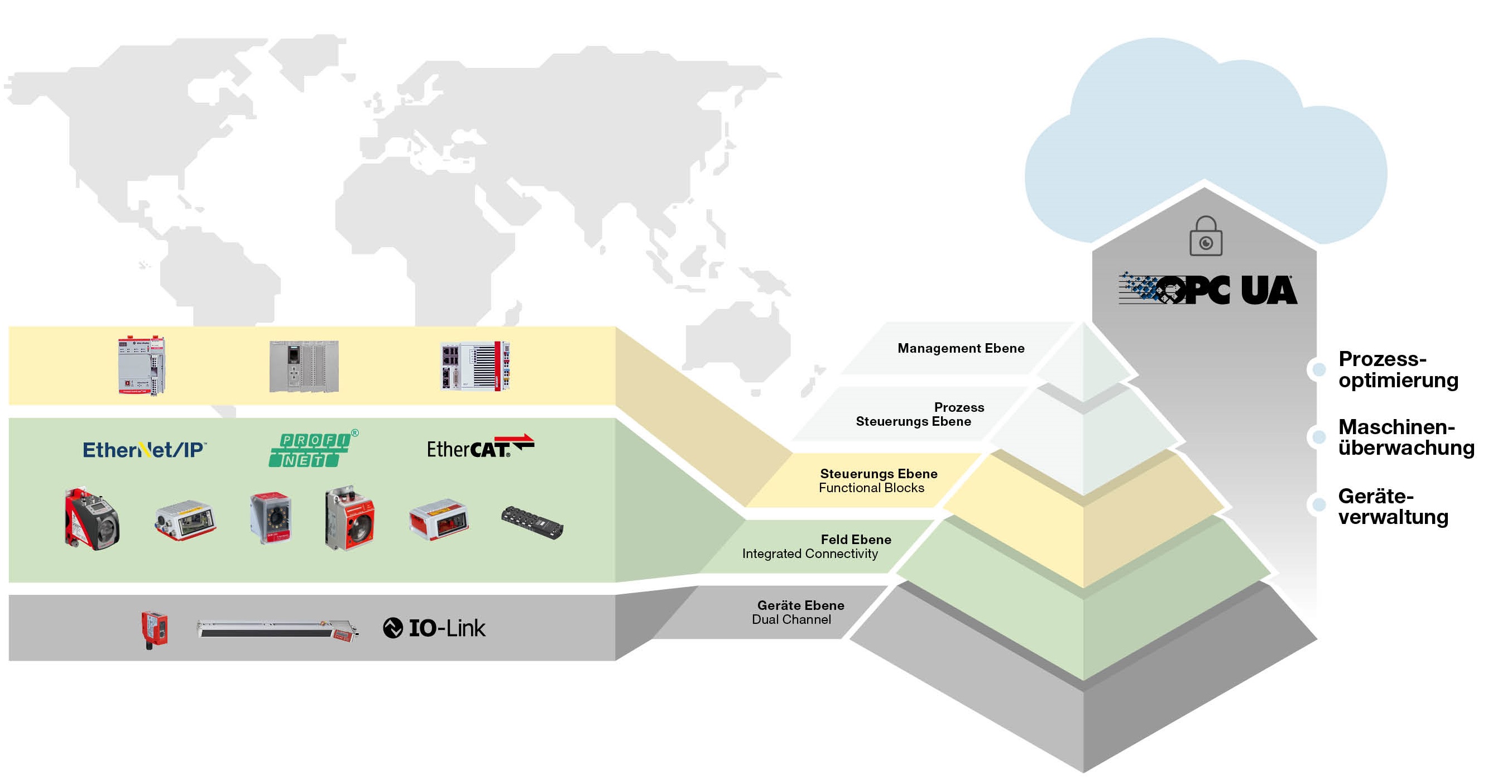
Einfaches Schnittstellen-Management in allen Steuerungs-Welten mit "integrated connectivity".
Der Sensor arbeitet mit
Ein Blick ins Geräteprofil von Sensoren mit integrated connectivity veranschaulicht weitere Erleichterungen bei der Programmierung. Ein Beispiel: Bei den Positionierungssensoren AMS und BPS liefert Leuze nicht nur Positionswerte, sondern auch einen errechneten Geschwindigkeitswert mit. Wer diesen Wert in seiner Anlage benötigt, spart sich die Zeit für eigene Berechnungen. Hinzu kommt: Wer ohne integrated connectivity nur nach bestimmten Barcodes filtern will, muss dies über die Steuerung erledigen. Mit den Leuze Barcodelesern BCL geht das effizienter, denn hier lässt sich nach bestimmten Kriterien vorfiltern. Dadurch werden nur Codes an die Steuerung übertragen, die dem gewünschten Muster entsprechen. Zeit spart nicht zuletzt die Möglichkeit, Profinet-Geräte im Engineering Tool zu duplizieren. Anwender:innen müssen so nur einmal parametrieren und können die Einstellungen danach beliebig kopieren. Selbst bei einem Gerätetausch hilft integrated connectivity: Muss ein beschädigter Sensor getauscht werden, überträgt das System alle in der Steuerung hinterlegten Parameter automatisch auf das neue Gerät. Der Sensor ist sofort einsatzbereit.
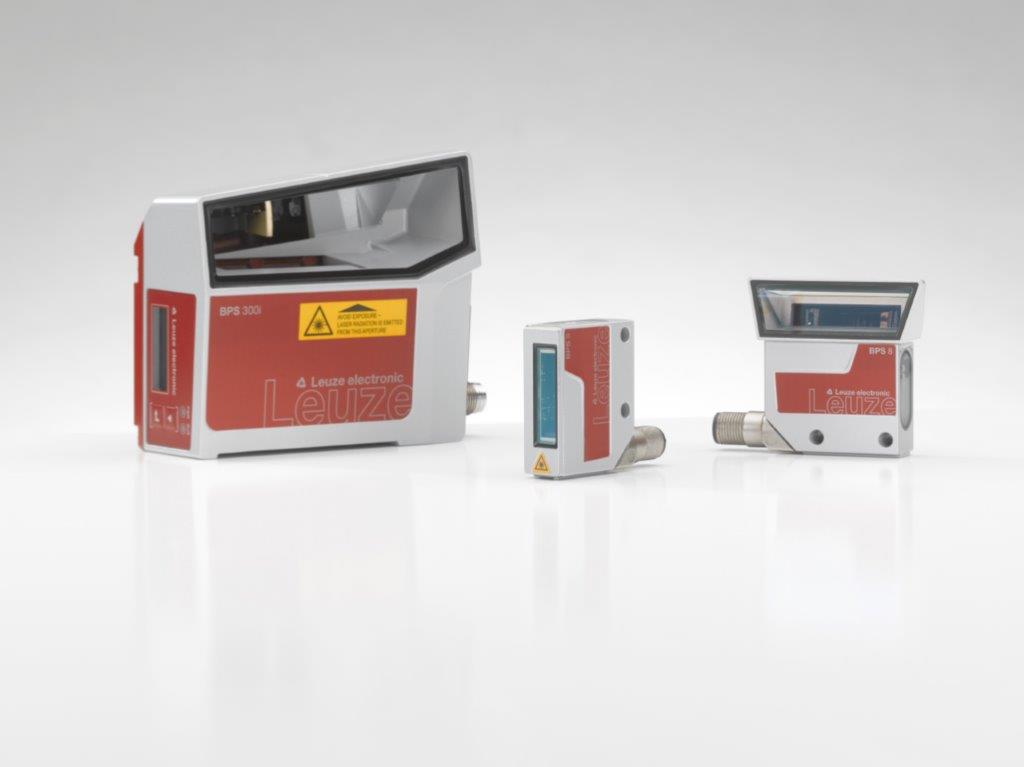
Das Barcodepositioniersystem BPS 300i (links im Bild) ist mit integrated connectivity ausgestattet.
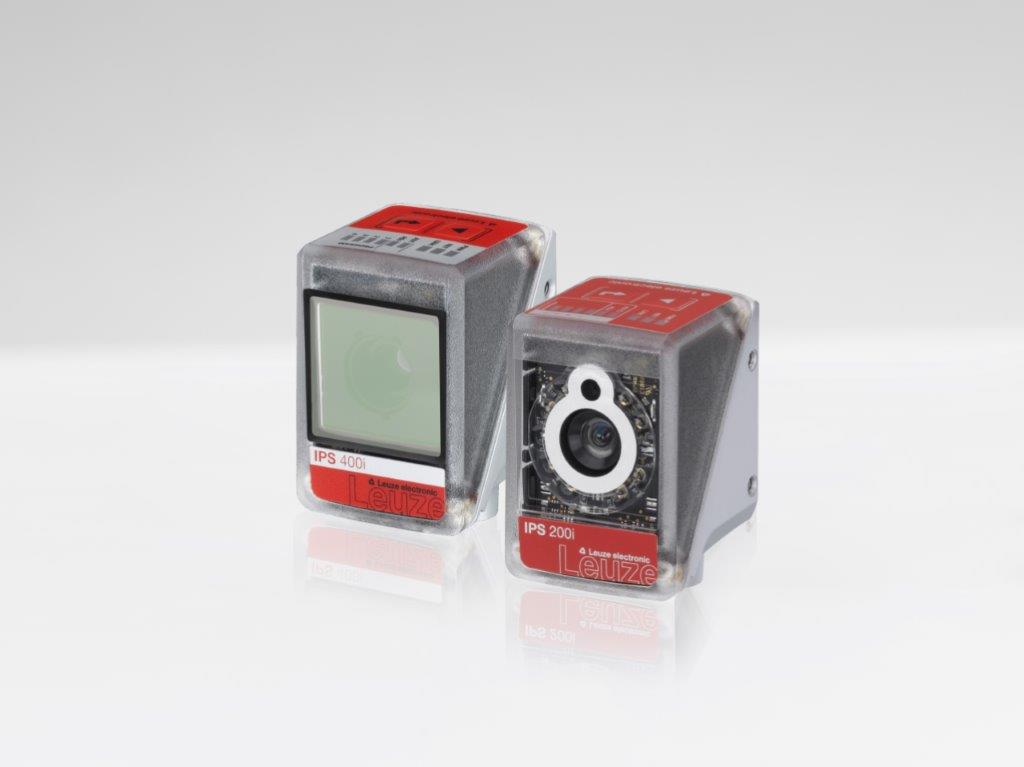
Die Sensoren IPS 200i/400i zur Feinpositionierung in der Intralogistik sind mit integrated connectivity ausgestattet.
Qualität im Blick behalten
Integrated connectivity unterstützt nicht nur bei der Inbetriebnahme, sondern auch bei der Maschinenüberwachung (Condition Monitoring). Anlagenbetreiber brauchen für einen effizienten Betrieb Antworten auf Fragen wie: Läuft die Anlage fehlerfrei? Wann muss ich eine Wartung planen? Antworten darauf gibt es dank integrierter Schnittstelle. Sie überträgt über die Industrial Ethernet-Kommunikation nicht nur die eigentlichen Prozesswerte, sondern auch Diagnosedaten, die in der Steuerung verfügbar sind. So lassen sich über einen Barcodeleser alle identifizierenden Daten auslesen, um das Gerät zu verwalten. Dazu zählen etwa die Seriennummer oder die Software/Hardware-Version des Sensors. Darüber hinaus gibt es jedoch etliche Diagnoseparameter, etwa die Zahl der IO-Lesungen und der NIO-Lesungen. Insbesondere liefert das System in einer Anlage mit Barcodelesern aber auch für jede einzelne Codelesung einen Qualitätsmerker. Dieser gibt Aufschluss über die Qualität der Lesungen. Der Wert liegt in der Regel zwischen 90 und 95 Prozent und lässt sich beobachten, um Abweichungen im laufenden Betrieb festzustellen, zum Beispiel durch Verschmutzung oder mechanische Beschädigungen. Auch Remoteüberwachung ist per OPC UA als zusätzlichem Kommunikationskanal realisierbar. Dies ist einerseits über die Steuerung möglich, lässt sich andererseits jedoch deutlich komfortabler über Leuze Sensoren lösen. Denn auf diese kann direkt per OPC UA zugegriffen werden. Anlagenbetreiber können so parallel zum laufenden Prozess ihre Geräte beobachten. So wissen sie jederzeit, wie gut die Anlage läuft. Falls gewünscht, können diese Daten auch in eine Cloud geladen werden – hierfür gibt es keinerlei Einschränkungen.
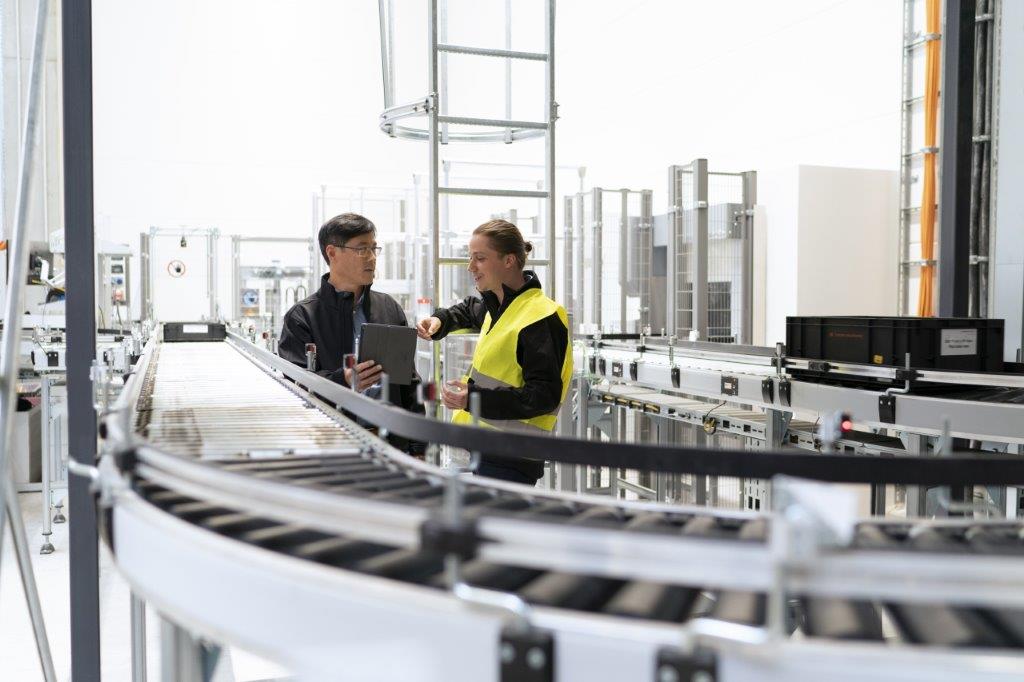

Integrated connectivity bietet Vorteile bei der Inbetriebnahme, Prozesse können optimiert und die Anlage so bestmöglich betrieben werden.
Prozesse einfach optimieren
Wie lassen sich nun Prozesse auf Basis der erhobenen Daten optimieren? Das zeigen stellvertretend zwei Praxisbeispiele anhand von Barcodelesern. Erstes Beispiel: Die Sichtscheibe des Sensors kann verschmutzen. In manchen Anlagen geschieht das erst nach Jahren, in anderen schneller. Um nun zeitnah festzustellen, welcher Sensor verschmutzt ist, lässt sich mittels Datenauswertung per OPC UA ansetzen. Anhand der Daten registriert eine Software die Lesegüte jedes einzelnen Decodiervorganges. Diese schlägt für Barcodeleser mit einer schlechteren Leseleistung eine Wartung vor. Zweites Beispiel: Auch das Etikett selbst kann ein Problem verursachen – etwa, wenn der Code beschädigt oder nicht vollständig gedruckt ist. In dem Fall genügt es nicht, einen einzelnen Sensor zu beobachten, um den Fehler festzustellen. Stattdessen gilt es, das fehlerhafte Etikett über verschiedene Messstationen zu verfolgen, um es zu identifizieren. Auf diese Weise lassen sich ähnliche Auswertungen erkennen und per Identifikationsnummer Rückschlüsse ziehen, um welches Etikett es sich handelt.
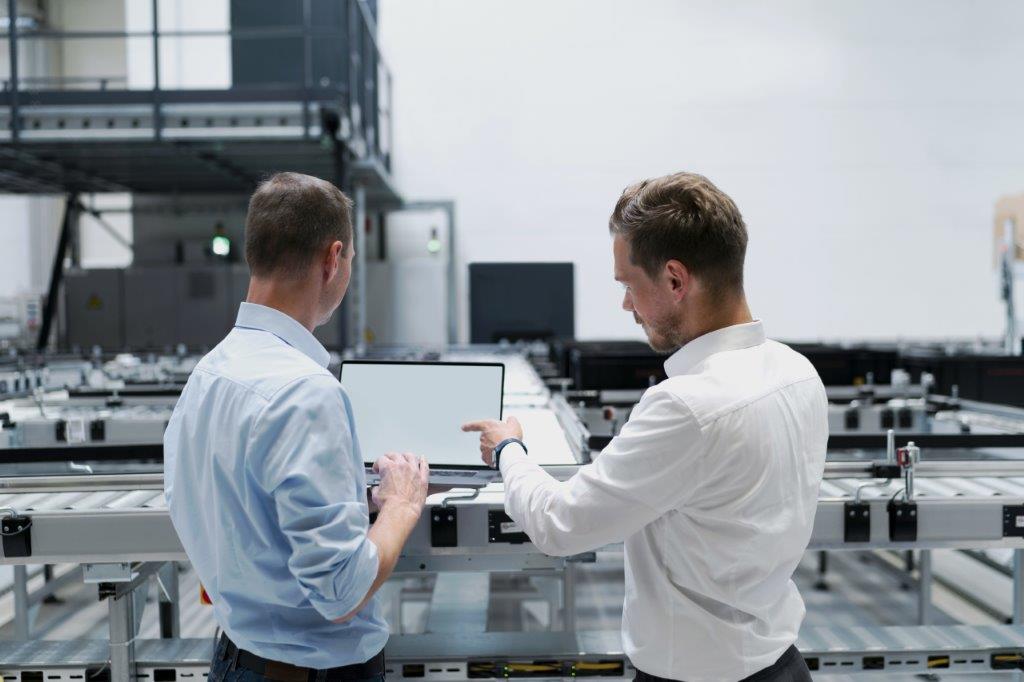
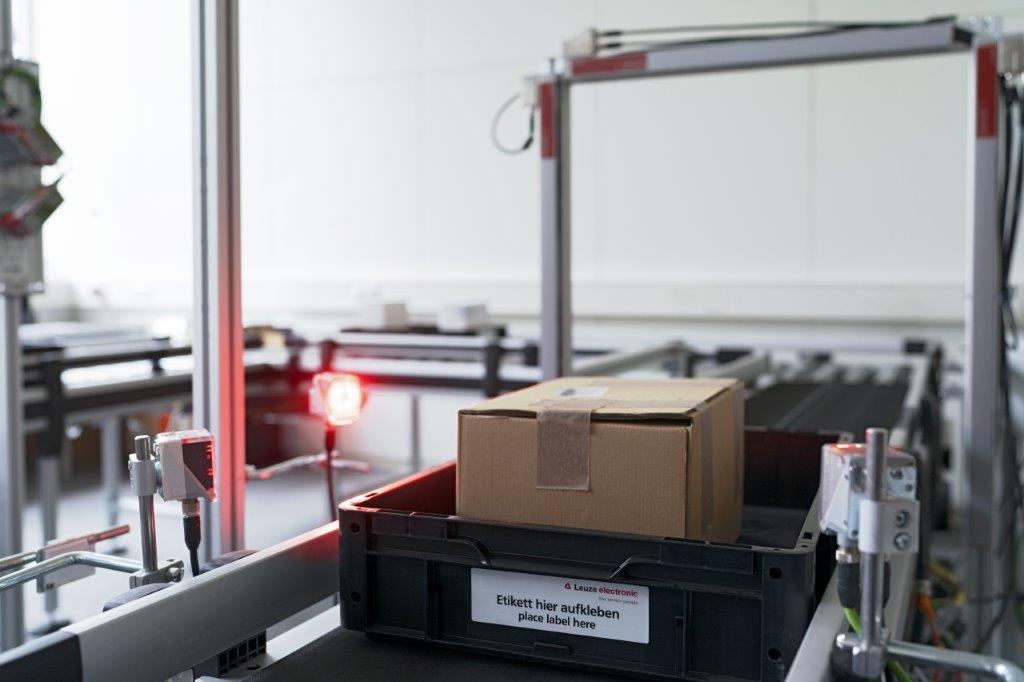
Integrated connectivity für einen optimalen Betrieb der Anlage
Fazit: Effizienter auf drei Ebenen
Integrated connectivity bietet Vorteile auf mehreren Ebenen. Sie trägt zu einer einfacheren Inbetriebnahme bei und liefert Zusatzinformationen zur Maschinenüberwachung. Auf Basis der Informationen lassen sich insbesondere Prozesse optimieren und die Anlage so bestmöglich betreiben. Alle Sensoren, die Leuze für die Feldbus-gesteuerte Automation beispielsweise in der Intralogistik entwickelt, sind mit integrated connectivity ausgestattet. Anlagenbetreiber sparen damit Zeit und Geld.